Figures & data
Table 1. W–input values for manual control process.
Table 2. The parameters used in the application of a controller.
Table 3. The parameters calculated in control application.
Figure 13. Variation of net pushing forces developed by a constant 100 N load and five different springs in the operation interval.
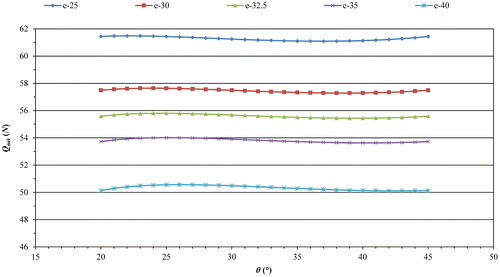
Figure 14. Variation of per cent error in the net pushing force developed by a constant 100 N load and five different springs in the operation interval.
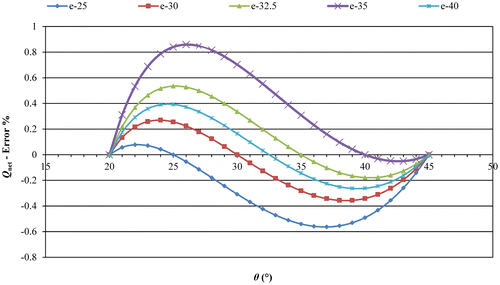
Table 4. The equal error parameters.
Figure 15. Angle θ 1 calculated using Equal Error Distribution Method and the resulted Q net values.
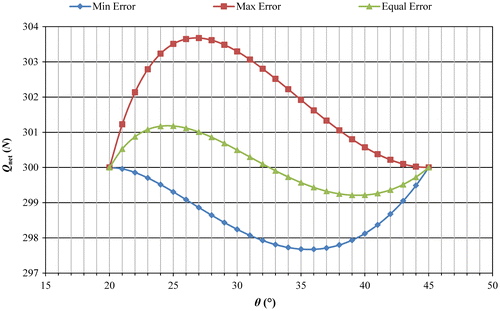