Figures & data
Figure 1. Illustration of the discrepancies observed when comparing experimental data to results from numerical models of moisture transfer in porous material.
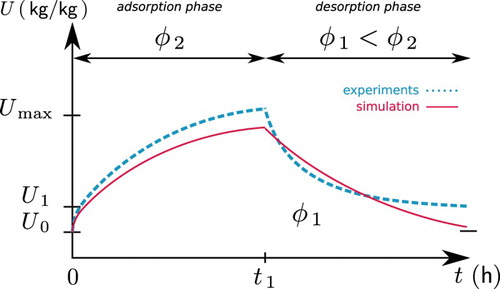
Figure 3. Sensors of relative humidity and temperature (a) and wood fibre samples (b) with white acrylic seal and with aluminium tape.
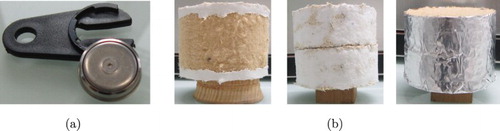
Table 1. A priori dimensionless material properties of wood fibre from [Citation23,Citation33].
Table 2. Possible designs according to the experimental facility.
Figure 4. Variation of the criterion Ψ for the four possible single-step designs (a) and as a function of the sensor position X for the OED (b), in the case of estimating one parameter.
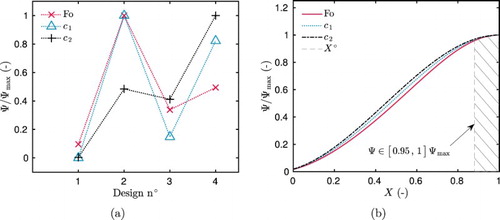
Figure 6. Variation of the criterion Ψ for the 16 possible designs (a) and as a function of the sensor position X for the OED (b), in the case of estimating one parameter.
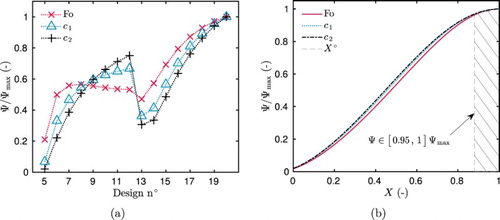
Figure 7. Sensitivity coefficients Θ for parameters ,
and
for the OED (design 20) (a), design 12 (b), design 5 (c) and design 13 (d) (
).
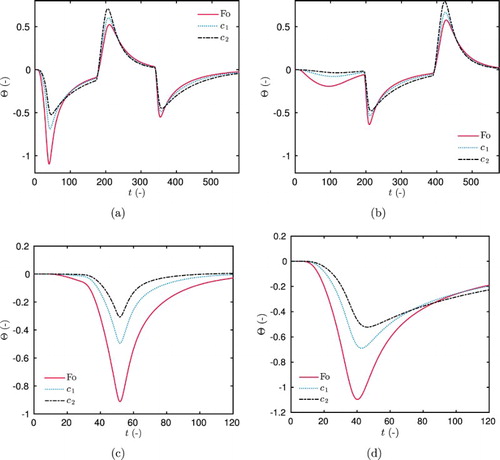
Figure 8. Variation of the criterion Ψ for the four possible designs of single step of relative humidity (a) and as a function of the sensor position X for the OED (b), in the case of estimating the couple of parameters .
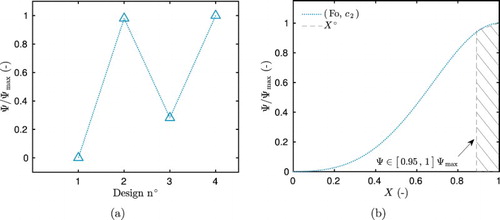
Figure 9. Variation of the criterion Ψ for the 16 possible designs of multiple steps of relative humidity (a) and as a function of the sensor position X for the OED (b), in the case of estimating the couple of parameters .
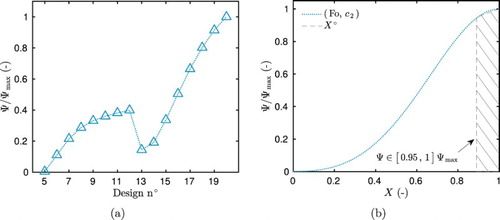
Table 3. Synthesis of the tests carried out with the expression of the cost function.
Figure 10. Residual between the measured data and numerical results for both experiments (a) and number of computations of the direct problem (b) for the different definition of the cost function .
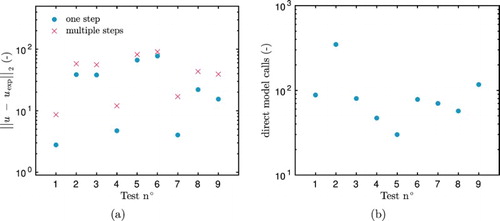
Figure 11. Comparison of the numerical results with the experimental data (a–b) and their confidence interval for the single-step (a) and the multiple-step (b) experiments (test 1). Comparison of the residual for the single-step (c) and multiple-step (d) experiments.
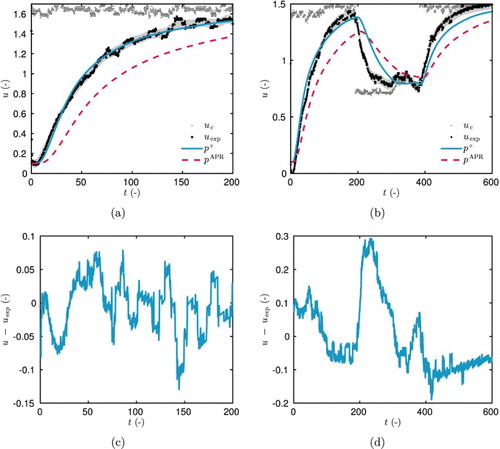
Figure 12. Convergence of the parameter estimation, for the test 1 as a function of the number of iterations (a) and number of computations of the direct model (b).

Figure 13. Probability density function approximated for the estimated parameters, computed using the sensitivity of single-step (c) and a multiple-step (a–b) experiments.
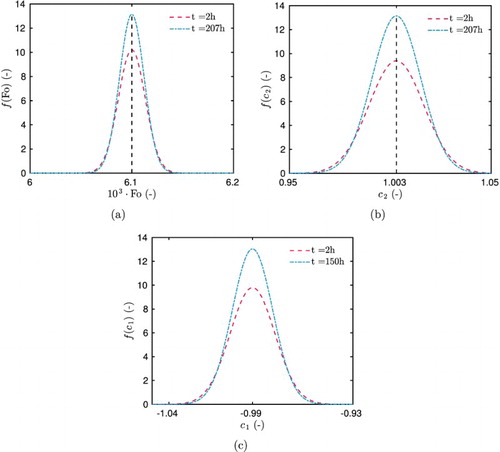
Figure 14. Variation of the criterion Ψ for the 16 possible designs for the adsorption coefficients (a) and the desorption coefficients (b).
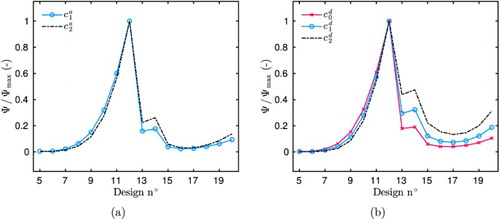
Table 4. Synthesis of OED for the estimation of one or several parameters when the model account for hysteresis.
Figure 17. Comparison of the numerical results with the experimental data (a) and their residual (b).
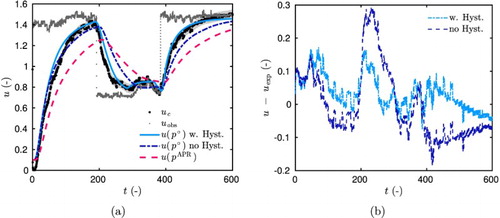
Figure 18. Variation of the sorption coefficient c according to time (a) and according to the computed field u (b).
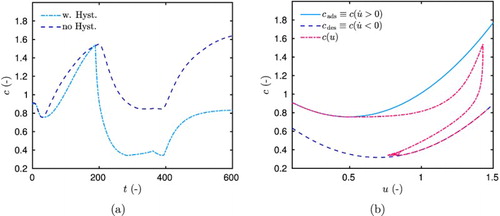
Table
Table
Figure A1. Time variation of the field u (a) and of the sorption capacity c (b) for the model with hysteresis and the regularised one.
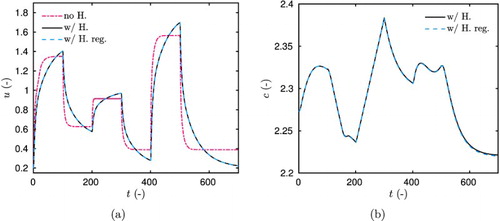
Figure A2. Variation of the sorption capacity c with the field u (a) according to the case study. Time variation of the error (b) for the fields u and c between the model with hysteresis and the regularised one.
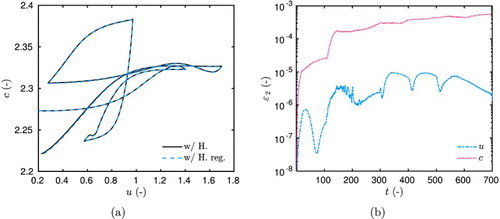