Figures & data
Table 1. Material properties for the test plate.
Table 2. First six natural frequencies of the ‘patch’ plate.
Table 3. Difference in frequencies of an example plate with and without the presence of a ‘patch’.
Figure 2. Convergence plots for (a) fibre, (b) matrix and (c) ‘patch’ moduli without noise in ‘test’ data.
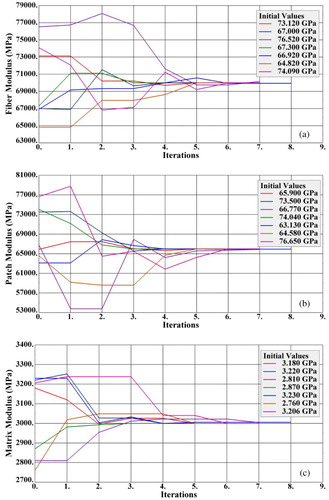
Figure 3. Convergence plots for (a) fibre, (b) matrix and (c) ‘patch’ moduli with noise in ‘test’ data.
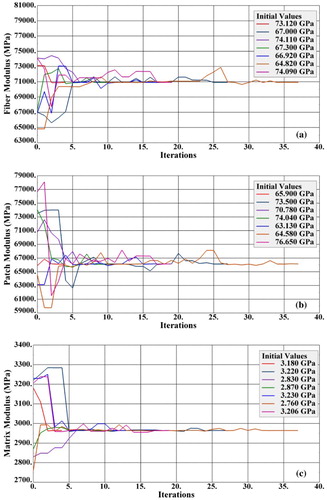
Figure 4. Convergence plots for (a) fibre, (b) matrix and (c) ‘patch’ moduli with a 20% sized patch and having noise in ‘test’ data.
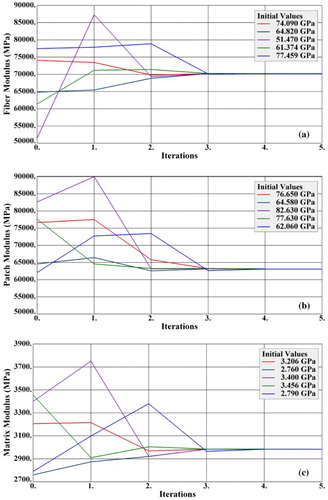
Table 4. Natural frequencies of the ‘patch’ plate and the reference plate.
Figure 11. Convergence curves for the elastic modulus of (a) matrix (b) fibre outside the ‘patch’ and (c) fibre within the ‘patch’.
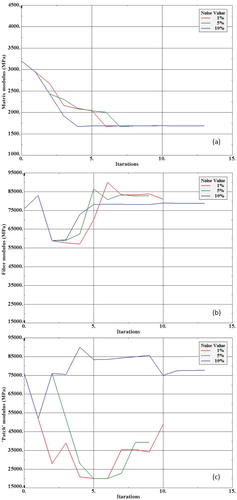