Figures & data
Table 1. Weighting function for SG using second-order polynomial and 5 data points.
Figure 8. Grid-independency for wall pressure distribution along the upper and lower lines of the symmetric plane.
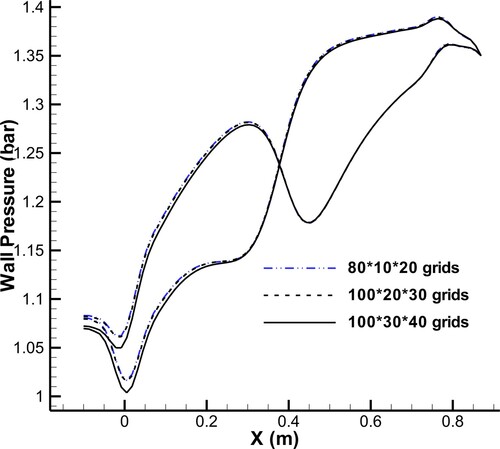
Figure 10. Three geometries with the same centre-line curvature and different cross-sections, and (a) their corresponding pressure distributions along the upper and lower lines of the symmetry plane, and (b) average pressure of cross-section.
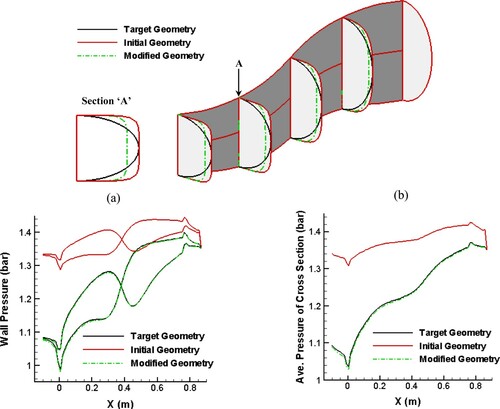
Figure 11. Evolution of geometries and their corresponding pressure distributions from the initial guess to the target geometry.
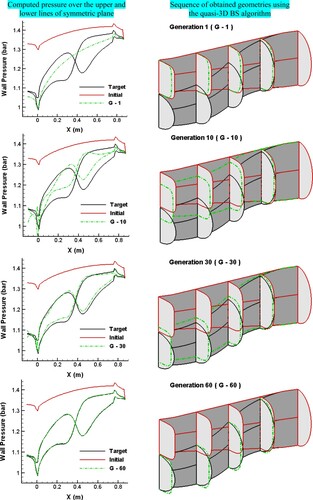
Figure 13. Results of inverse design with similar cross-sectional profiles (n = 2) for the initial and target geometry using an equally angled grid and radial spines after 150 geometry corrections.
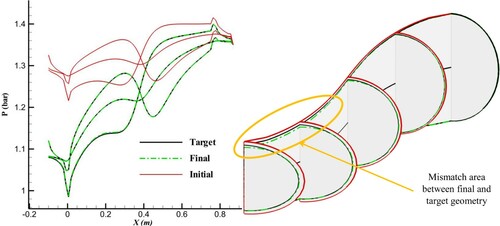
Figure 14. Results of inverse design with similar cross-sectional profiles (n = 4) for the initial and target geometries using an equally angled grid and radial spines after 150 geometry corrections.
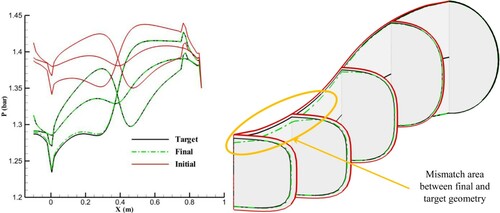
Figure 15. Results of inverse design with different cross-sectional profiles for the initial guess (n = 6) and target geometries (n = 2) using an equally angled grid and radial spines after 150 geometry corrections.
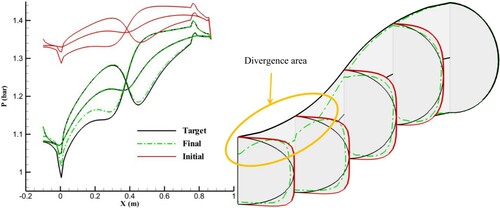
Figure 16. Results of inverse design with different cross-sectional profiles for the initial guess (n = 6) and target geometries (n = 2) using radial spines after 200 geometry corrections.
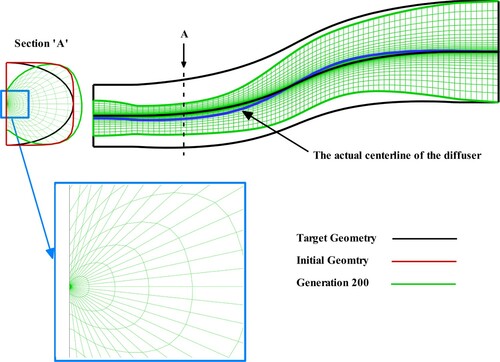
Figure 17. Results of inverse design with similar cross-sectional profiles (n = 2) for the initial and target geometries using an equally angled grid and vertical spines after 200 geometry corrections.
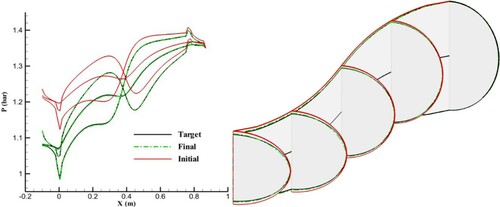
Figure 18. Results of inverse design with similar cross-sectional profiles (n = 4) for the initial and target geometries using an equally angled grid and vertical spines after 200 geometry corrections.
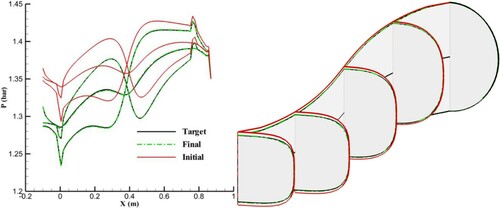
Figure 19. Results of inverse design with different cross-sectional profiles for the initial guess (n = 6) and target geometry (n = 2) using an equally angled grid and vertical spines after 200 geometry corrections.
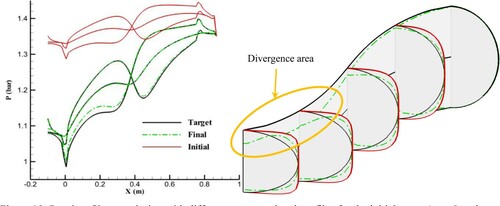
Figure 20. Results of inverse design with similar cross-sectional profiles (n = 2) for the initial and target geometries using an equally angled grid and horizontal spines after 200 geometry corrections.
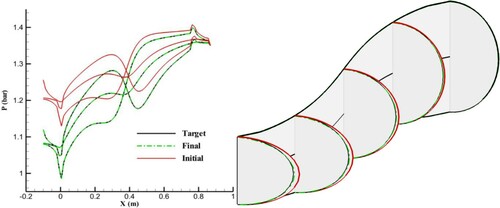
Figure 21. Results of inverse design with similar cross-sectional profiles (n = 4) for the initial and target geometries using an equally angled grid and horizontal spines after 200 geometry corrections.
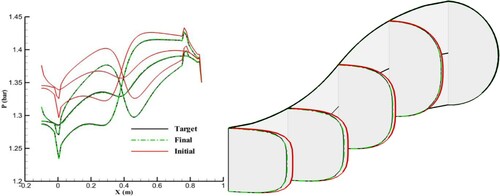
Figure 22. Results of inverse design with different cross-sectional profiles for the initial guess (n = 6) and target geometry (n = 2) using an equally angled grid and horizontal spines.
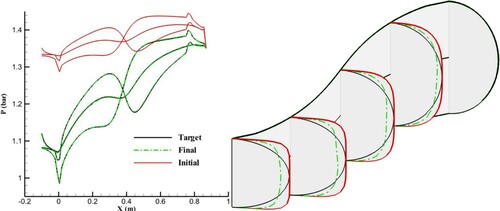
Figure 23. Comparison of wall pressure distributions for the target and final geometry with an equally angled grid along the lateral lines of the wall at various sectors.
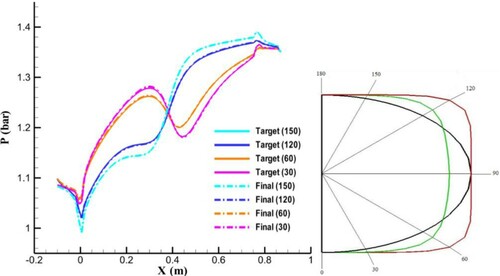
Figure 24. Comparison of streamline-based and equally angled grid generation for the initial guess and target geometry with the same cross-sectional profile.
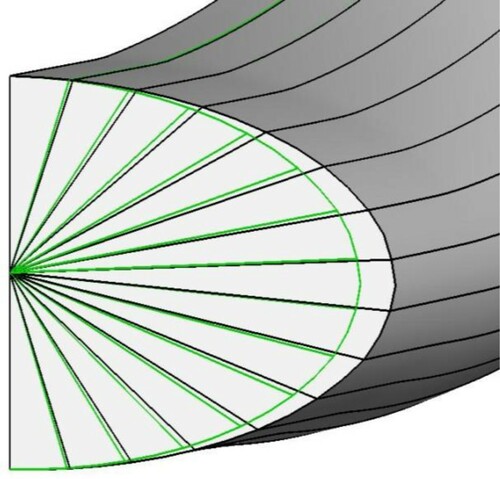
Figure 25. Comparison of equally angled (a) and streamline-based (b) grid generation for the initial guess and target geometry with different cross-sectional profiles.
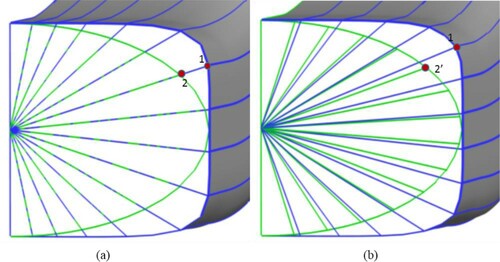
Figure 26. Comparison of wall pressure distributions for the target and final geometry with streamline-based grid along the wall streamlines
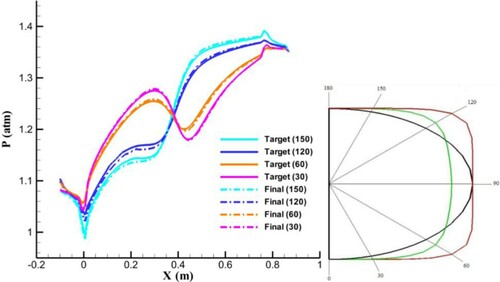
Figure 27. Results of inverse design with different cross-sectional profiles for the initial guess (n = 4) and target geometry (n = 2) using the streamline-based grid and horizontal spines after 200 corrections.
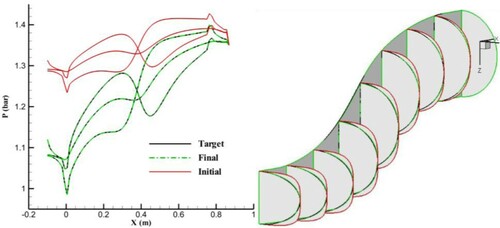
Table 2. Conditions for convergence and unique solution for the inverse design of the s-shape diffuser.
Figure 28. Optimum pressure distribution along the upper and lower lines of the symmetry plane of an S-duct as a TPD for quasi-3D inverse design.
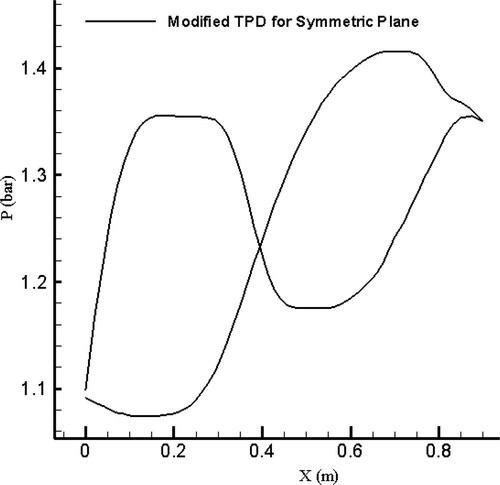
Figure 29. Symmetric plane of the quasi-3D designed S-duct corresponding to the optimum pressure distribution.
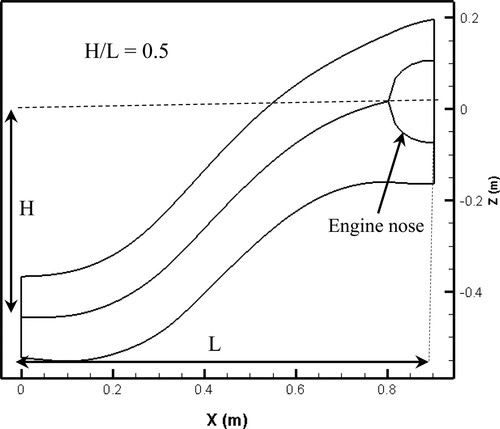
Figure 32. Streamlines and flow separation corresponding to the plane adjacent to the symmetry plane (section D) for the quasi-3D designed S-duct.
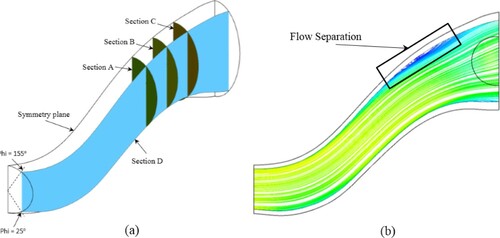
Figure 38. Contours of stagnation pressure in various axial positions for the quasi-3D and 3D designed S-ducts.
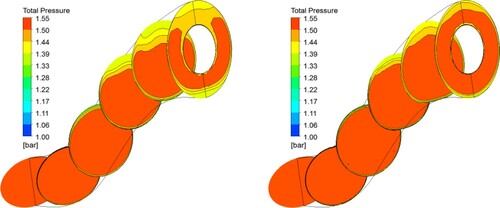
Table 3. Comparison between quasi-3D designed S-duct performance and 3D designed.