Figures & data
Figure 4. Synthetic stress–time data produced by a model consisting of a spring combined with three Maxwell elements for three different displacement rates.
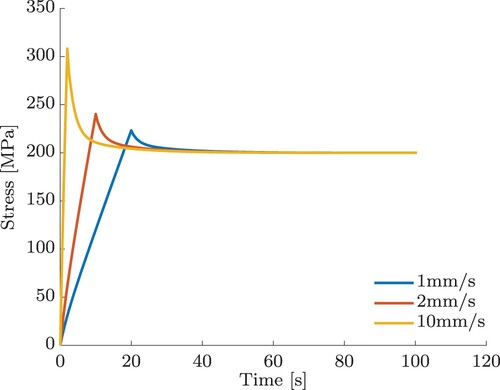
Table 1. Selected material parameters to simulate data.
Table 2. Reconstructed material parameters before and after clustering where the are given in MPa and the
in seconds.
Table 3. Approximated material parameters with similar noisy data, where the are given in MPa and the
in seconds.
Figure 5. Spread of the material parameters for 100 runs with different noise seeds, but same noise level
for
= 10 mm/s.
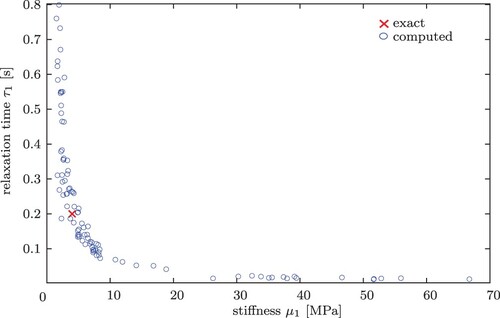
Table 4. Clustered material parameters with noisy data ( mm/s) where the
are given in MPa and the
in seconds.
Table 5. Maximum values of individual stress components (MPa) with slow and fast deformation rates attained at .
Table 6. Clustered material parameters with and without regularization where the are given in MPa and the
in seconds.
Figure 8. Smallest relaxation time determined from 100 runs with (a) no regularization, (b) classical Tikhonov–Phillips regularization and (c) adjusted regularization term.
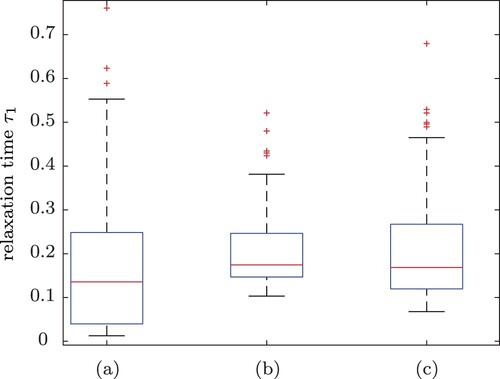
Figure 9. Largest relaxation time for 100 runs with (a) no regularization, (b) classical Tikhonov–Phillips regularization and (c) adjusted regularization term.
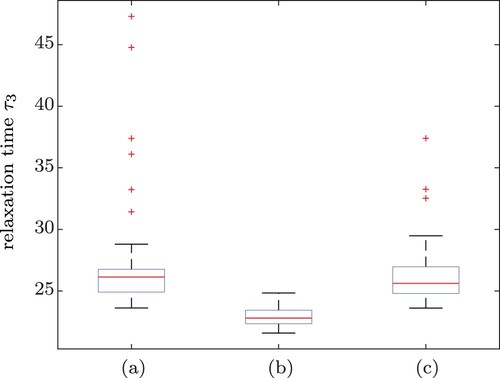