Figures & data
Figure 3. Pore size distribution of pyrolysed polycarbosilane, phenolic resin and phenolic resin after BO
infiltration.
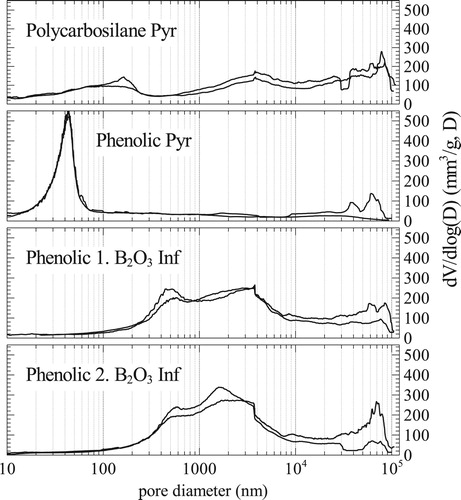
Figure 6. Viscosity in dependence of temperature at three different shear rates for different melts.
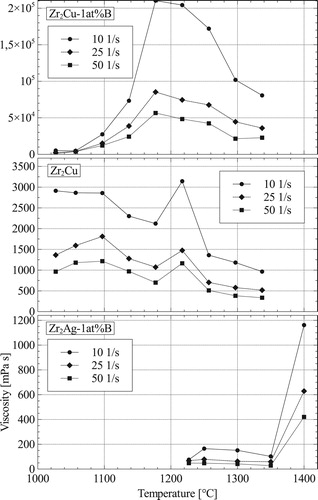
Register now or learn more
Open access
Figure 3. Pore size distribution of pyrolysed polycarbosilane, phenolic resin and phenolic resin after BO
infiltration.
Figure 6. Viscosity in dependence of temperature at three different shear rates for different melts.
People also read lists articles that other readers of this article have read.
Recommended articles lists articles that we recommend and is powered by our AI driven recommendation engine.
Cited by lists all citing articles based on Crossref citations.
Articles with the Crossref icon will open in a new tab.