Figures & data
Figure 1. (a) Ti-Ta and Ti-Ta-Cu compositions were additively manufactured using the SLM technique with increasing energy densities, and the effect of the print energy densities was studied on the porosity, compression behaviour, microstructure, phase analysis, and Vickers microhardness. (b) Image of the build plate after SLM processing explaining the study design.
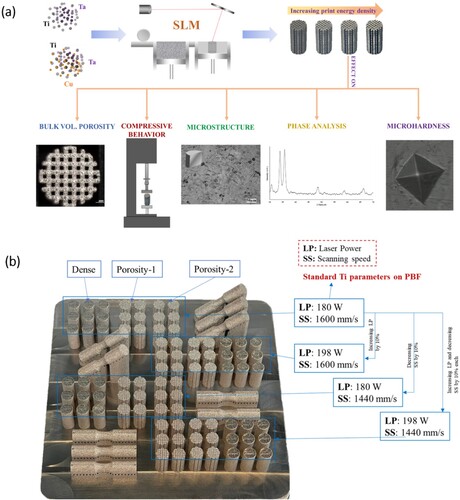
Table 1. Laser power and scanning speed and respective energy densities used for printing Ti6Al4 V, Ti3Al2 V, Ti3Al2V + 3Cu, Ti3Al2V + 10Ta & Ti3Al2V + 10Ta + 3Cu compositions on the powder bed fusion.
Figure 2. Effect of compositional variation: Ti64, Ti32, Ti32Cu, Ti32Ta, and Ti32TaCu. All compositions are printed using the same printing parameters on an SLM machine. (a) Pore images for Porosity-2 samples for all compositions. Ti64 and Ti32Cu display distorted pore boundaries with higher amounts of partially melted powder particles on the pore edges. The highest pore sizes were observed for Ti32 and Ti32TaCu. (b) Schematic representation of the melt-pool for all compositions during laser melting operation. A wider and shallower melt-pool resulted in higher strut size and lower porosities for Ti32Cu-54 compared to Ti32-54 due to the high thermal diffusivity of Cu. For Ti32Ta-54, the melt pool was wider and deeper than that for Ti32-54 due to excellent laser absorption of Ta increasing the melt pool temperature and reducing the viscosity. A synergistic effect of Ta and Cu in Ti32TaCu-54 resulted in a smaller and narrower melt-pool than Ti32Ta-54 and Ti32Cu-54; Ta and Cu negated their individual effect in Ti32. It is to be noted that the schematics shown are for better interpretation of the discussions and do not represent results from any simulations. (c) Microstructural images along the build direction for all compositions. Ti64 and Ti32 show α′ laths with prior β grain formation; higher amounts of prior β grain formation in Ti64 than Ti32. Ti32Cu microstructure showing melt-pool impressions/fusion boundaries with keyhole porosities formed due to balling effect. Ti32Ta and Ti32TaCu display pronounced melt-pool impressions with unmelted and partially melted Ta particles. (d) represents projected values at 10 and 25% porosities for elastic modulus and compressive yield strength from linear trendlines from experimental values. Note that the bars do not have error bars since these are extrapolated values from linear fit obtained from average modulus and yield strength numbers for varying porosities (Supplemental Figure S1); the extrapolation method is used to eliminate the porosity variation parameter and better understand the effect of composition on the mechanical properties. Cu addition primarily acts as a strength enhancer, with no effect on modulus. Ta addition results in higher modulus values with no effect on strength. The synergistic effect of Ta and Cu addition enhances both modulus and strength.
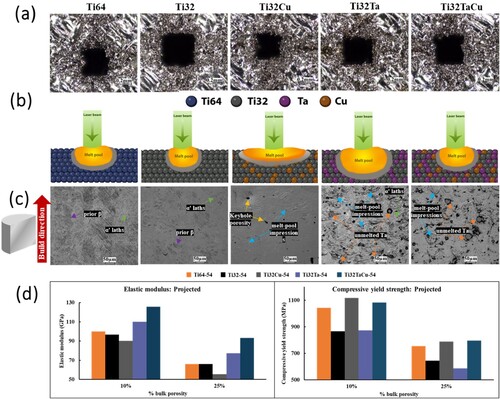
Table 2. Consolidated data for porosity, elastic modulus, compressive yield strength, and deviation of as-printed diameter of cylindrical structures from designed values for all compositions, for Dense, Porosity-1, and −2 groups.
Figure 3. Ti32Ta system printed on SLM with varying energy densities. (a) Pore images for Porosity-2 samples for Ti32Ta compositions. No noticeable effect of varying energy density can be observed. (b) Microstructural images along the build direction for Ti32Ta with energy densities 54–65 J/mm3. Ti32Ta-59H and −65 with higher laser power show lower amounts of unmelted Ta particles and lesser pronounced melt-pool impressions than Ti32Ta-54 and Ti32Ta-59L with laser power. This indicates excellent laser absorption of Ta, resulting in a sensitivity of Ti32Ta composition on laser power rather than the overall energy density. (c) reports plots for elastic modulus and compressive yield strengths. Statistical analyses were done using one-way ANOVA in Minitab Statistical Software (Minitab LLC, PA, USA) for n = 3 and P-value < 0.05 for a significant difference. Pairwise comparisons were conducted using Tukey-Kramer simulations; the statistical difference was marked with an ‘*’. Our results indicate that although laser power affected the microstructure and the resulting porosities, no significant effect was observed on the mechanical properties of Ti32Ta compositions with varying energy densities.
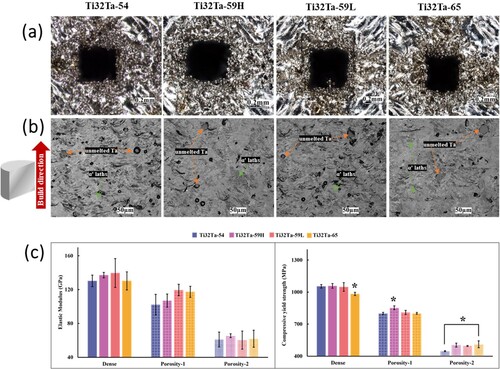
Table 3. Consolidated table for porosity, modulus, and compressive yield strength values for Ti32Ta compositions with varying energy densities.
Figure 4. Ti32TaCu system printed on SLM with varying energy densities. (a) Pore images for Porosity-2 samples for all compositions. (b) Microstructural images along the build direction for Ti32TaCu with energy densities 54–65 J/mm3. Ti32TaCu-54 shows high amounts of unmelted Ta particles compared to other compositions. Ti32TaCu-59H and −59L displayed similar microstructural features. Ti32TaCu-65 showed the least amount of unmelted Ta particles with melt-pool impressions wider compared to Ti32TaCu-54 due to heat dissipation by Cu. (c) reports elastic modulus and compressive yield strengths. Statistical analyses were done using one-way ANOVA in Minitab Statistical Software (Minitab LLC, PA, USA) for n = 3 and P-value < 0.05 for a significant difference. Pairwise comparisons were conducted using Tukey-Kramer simulations; the statistical difference was marked with an ‘*’. Our results suggest that Ti32TaCu composition was sensitive to the overall energy density used for printing rather than the effect of individual parameters such as laser power and scan speed.
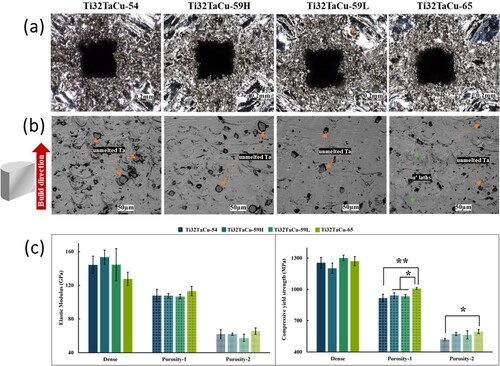
Table 4. Consolidated table for porosity, modulus, and compressive yield strength values for Ti32TaCu compositions with varying energy densities.
Supplemental Material
Download MS Word (707.1 KB)Data availability statement
All raw data for this study has been presented in this manuscript.