Figures & data
Figure 1. (a) Schematic of FDM process; (b) Geometry of the hot-end channel and boundary conditions of the computational model.
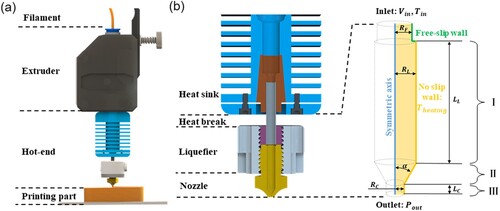
Table 1. Dimensions of INTAMSYS HT400 hot-end.
Table 2. Identified parameters for the constitutive model.
Table 3. Material properties adopted in the simulation.
Figure 3. Measured and predicted feeding force at different feeding rates. The predictions are conducted for various and generated using two models: (a) the GNF model and (b) the viscoelastic model.
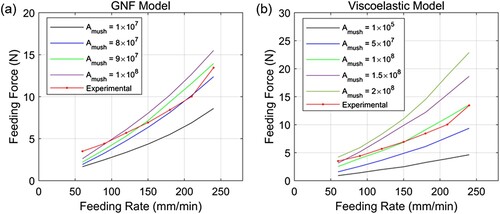
Figure 4. Influence of different on the simulation results for the liquid phase fraction and temperature distribution at different
.

Figure 6. Feeding force response with the GNF model (c) and viscoelastic model (e) under the step velocity input (a). Feeding force response with the GNF model (d) and viscoelastic model (f) under the trapezoidal velocity profile (b).
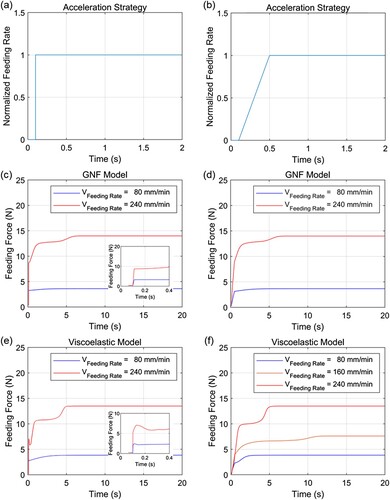
Figure 7. Distribution for solid-liquid phase, streamline and each component of the stress tensor at a feeding rate of 60 mm/min.
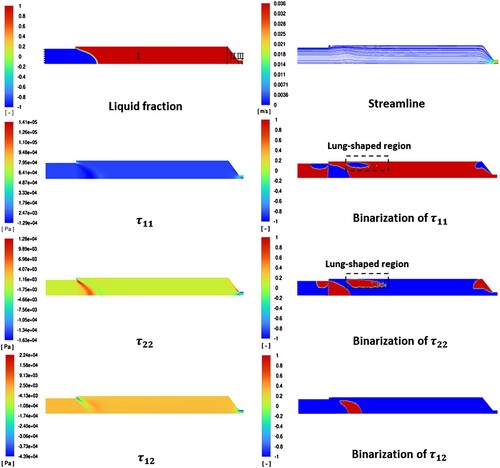
Figure 8. Comparison of distribution for normal stress difference and shear stress
at different feeding rates.
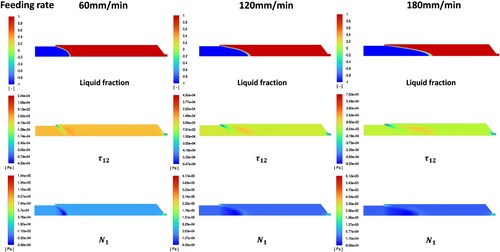
Figure 9. Curves about the area integral at the outlet for the normal stress difference and each stress tensor component versus the feeding rate.
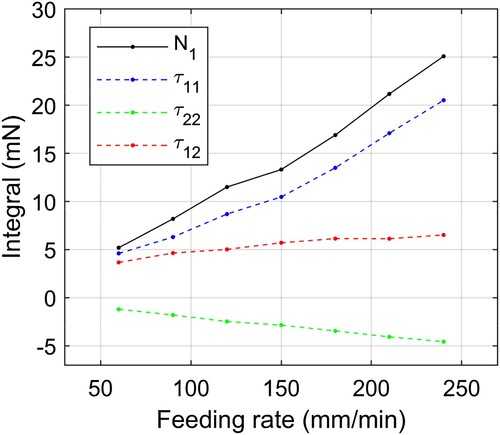
Data availability statement
The data that support the findings of this study are available from the corresponding author, [YX], upon reasonable request.