Figures & data
Figure 2. (a, b) The FE model of the multi-layer LPBF process and (c) laser scanning pattern during.
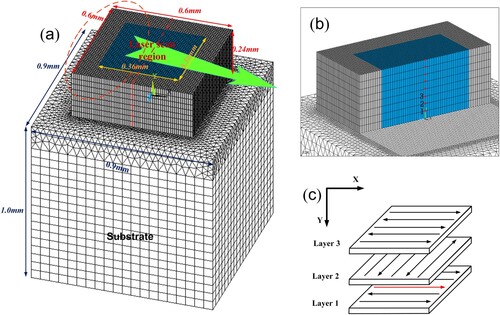
Table 1. Finite element simulation process parameters.
Table 2. Material parameters of solid Invar.
Table 3. Thermal property parameters of solid Invar.
Figure 4. (a) Invar alloy LPBF single pass scanning forming sample diagram. (b) The 16th group of samples melt track morphology.
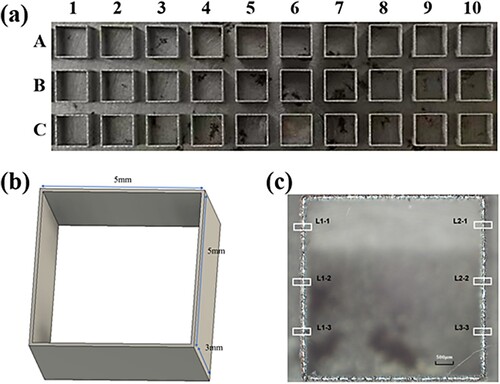
Table 4. Laser processing parameters for single tracks simulation and printing.
Figure 5. Numerical simulation and experimental values of the width of the melt track of stabilized working layer during LPBF of Invar alloy power process using different laser power (V = 800 mm/s) (a) and scanning speed (P = 140 W) (b).
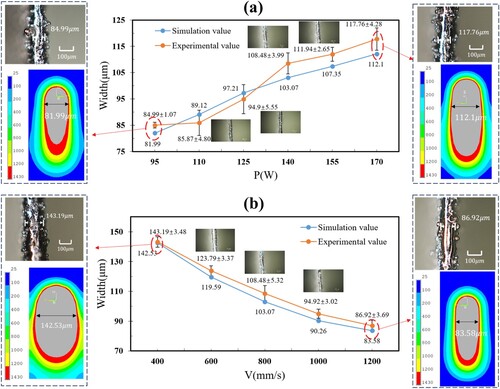
Table 5. Layer-by-layer optimization results.
Figure 9. Comparison between layer-by-layer optimized process parameters and mono process parameters.

Table 6. LPBF cubic fabricating process parameters.
Data availability statement
The data that support the findings of this study are available from the corresponding author [Y. Zhang], upon reasonable request.