Figures & data
Figure 1. Evolution of the LS3DP process and its feasible processes for LS3DP represented by C3DP. (A) Classification of 3D printing processes and their representative processes. (B) Feasible LS3DP processes represented by C3DP and their respective percentages. (3DP: 3D printing; SLA: stereolithography apparatus; DLP: digital light processing; 3SP: scan-spin-selective photocure; CLIP: continuous liquid interface production; SLS: selective laser sintering; DMLS: direct metal laser sintering; SLM: selective laser melting; EBM: electron beam melting; SHS: selective heat sintering; MJF: multijet fusion; FFF: fused filament fabrication; FDM: fused deposition modelling; SCP: smooth curvature printing; MJM: multijet modelling; LOM: laminated object manufacture; SDL: selective deposition lamination; UAM: ultrasonic additive manufacturing; LMD: laser metal deposition; LENS: laser engineered net shaping; DMD: direct metal deposition; GMAW: gas metal arc welding; Respective percentages: statistical results of the use of 3D printing processes by institutions or research groups in the field of construction, percentage using MEX, BJT and DED) [Citation1,Citation57].
![Figure 1. Evolution of the LS3DP process and its feasible processes for LS3DP represented by C3DP. (A) Classification of 3D printing processes and their representative processes. (B) Feasible LS3DP processes represented by C3DP and their respective percentages. (3DP: 3D printing; SLA: stereolithography apparatus; DLP: digital light processing; 3SP: scan-spin-selective photocure; CLIP: continuous liquid interface production; SLS: selective laser sintering; DMLS: direct metal laser sintering; SLM: selective laser melting; EBM: electron beam melting; SHS: selective heat sintering; MJF: multijet fusion; FFF: fused filament fabrication; FDM: fused deposition modelling; SCP: smooth curvature printing; MJM: multijet modelling; LOM: laminated object manufacture; SDL: selective deposition lamination; UAM: ultrasonic additive manufacturing; LMD: laser metal deposition; LENS: laser engineered net shaping; DMD: direct metal deposition; GMAW: gas metal arc welding; Respective percentages: statistical results of the use of 3D printing processes by institutions or research groups in the field of construction, percentage using MEX, BJT and DED) [Citation1,Citation57].](/cms/asset/ea013c1f-47fa-48cc-9d9f-969b6e854ecf/nvpp_a_2346821_f0001_oc.jpg)
Figure 2. Available printing materials and their property space maps for LS3DP. (A) Young's modulus versus density. (B) Strength versus density.
Note: the strength of the cement-based, granular, ceramic, regolish material and metallic, wood-based and polymer materials are the compressive strength and tensile strength.
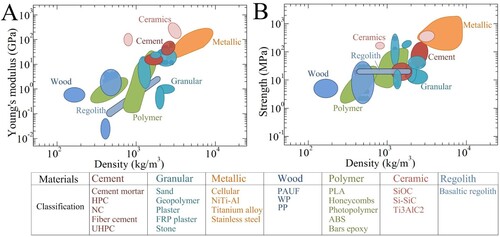
Figure 3. Classification of 3D printing equipment and their core printing actuator for LS3DP represented by C3DP. (A) 3D printing equipment commonly used for construction and their respective percentages (gantry, truss, robotic arm and tower, usually with 3, 3, 6 and 4 DOFs respectively). (B) Specific 3D printing equipment for construction (vehicle robotic arm, cable-positioning and truss robotic arm, usually with 6, 6 and 6 DOFs respectively). (C) Classification of printing heads for the LS3DP equipment for construction (heating extrusion, pressure extrusion, screw extrusion and welding deposition).
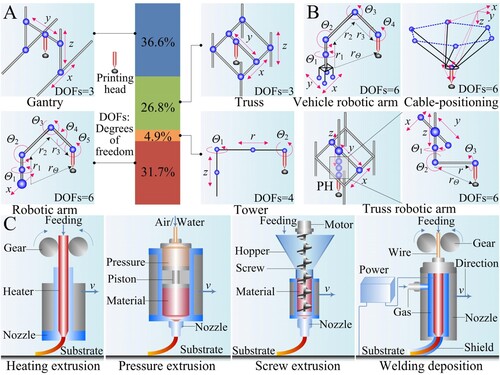
Figure 4. Core control technologies and their control equations for LS3DP represented by C3DP. (X: Shape of the printed layer or structure; f: Printing control equation for LS3DP; P: Printing control; S: 3D Spatial control; M: Printing control; X0: Other factors affecting the shape of the printed layer or structure; Δ: Deviation control; H: Scale of printing structure; V: Speed of movement for printing head; W: Angular speed of rotation for printing head; R: Nozzle diameter; F: Extrusion pressure; v: Extrusion speed; D: Standoff distance; u: Flow rate; tg: Time gap; T: Extrusion temperature; TA: Ambient temperature; h: Layer resolution; w: Extrusion width; h0: other factors that affect the h; w0: other factors that affect the w; hs: Layer resolution set by software; ws: Extrusion width set by software; Vx: Speed of movement in the x direction for printing head; Vy: Speed of movement in the y direction for printing head; Vz: Speed of movement in the z direction for printing head; ρ: Density of the material using LS3DP; E: Elastic modulus of the material using LS3DP; C: Compressive strength of the material using LS3DP; Δp: Path deviation; Δs: Shape deviation).
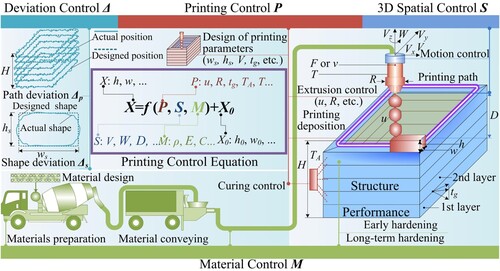
Figure 5. Statistical analysis and disruptive cases of LS3DP for construction. (A) Statistical analysis of the construction mode of LS3DP and its quantitative indicators (the construction mode includes printed components + assembly and on-site printing; quantitative indicators include VL, VT and RV; most quantitative indicator data are not directly available, but are approximations obtained through estimation, which can be estimated by referring to the method in the literature [Citation142]). (B) China's first polymer 3D printed bridge, the Shanghai Putuo Bridge (the length, width and height of the 3D printed bridge are 15.3, 3.8 and 1.2 m respectively). (C) Quanzhou 3D printing bridge (the length, width and height of the 3D-printed bridge are 17.5, 3.2 and 3.2 m respectively). (D) World's longest polymer 3D printed bridge, Chengdu Bridge (the total length of the bridge is 66.8 m, of which the 3D printed part is 21.6 m long, the widest section is 8 m and the highest section is 2.7 m). (E) The largest single-story 3D printed building in China, the Visitor Service Center of Nanjing Jiangbei New Area Civic Center (the building area is 286 m2 and the height is 5.2 m). (F) A single-story 3D printed building in China, the 3D Daichuang Activity Center of Nanjing (the building area is 98.5 m2 and the height is 5.6 m). (G, H and I) China's first integrated 3D printed habitable and deliverable two-story building (the building area is 52.8 m2 and the height is 6 m [Citation143]). (Here, the data are based on the statistics of application projects, the same project can be completed by multiple organisations, and the same organisation can also adopt different application modes. Projects using the first application mode can be printed as a whole and then assembled on site; projects using the second application mode are not always printed in whole on site; there are also partial components that are printed on-site or indoors and then assembled. CI: Cincinnati Incorporated; ORNL: Oak Ridge National Laboratory; TJU: Tongji University; SCG: Shanghai Construction Group; SCR: Shanghai Coin Robotics; MB: Mighty building; RO: ROYAL3D; TU/e: Eindhoven University of Technology; LU: Loughborough University; USC: University of Southern California; UGent: Ghent University; TUD: TU Dresden; ETH: ETH Zurich; Winsun: Yingchuang Building Technique; LAG: Liaoning Architecture GreenPrint; NJK: Nanjing Kenyo; SEU: Southeast University; HSG: Henan Space Grey; HEBUT: Hebei University of Technology; CSCEC: China State Construction Engineering Corporation; JTT: Jianyanhua testing (Hangzhou) Technology; ZHA: Zaha Hadid Architects; SMC: Shimizu Corporation; MIT: Massachusetts Institute of Technology; AIS: AI SpaceFactory; BHLT: Beijng Huashang Luhai Technology; THU: Tsinghua University; CIIC: CIIC (Tianjin) Technology; TAM: Twente Additive Manufacturing; B3D: BUILDERA 3D; MU: Monolite UK/ D-shape).
![Figure 5. Statistical analysis and disruptive cases of LS3DP for construction. (A) Statistical analysis of the construction mode of LS3DP and its quantitative indicators (the construction mode includes printed components + assembly and on-site printing; quantitative indicators include VL, VT and RV; most quantitative indicator data are not directly available, but are approximations obtained through estimation, which can be estimated by referring to the method in the literature [Citation142]). (B) China's first polymer 3D printed bridge, the Shanghai Putuo Bridge (the length, width and height of the 3D printed bridge are 15.3, 3.8 and 1.2 m respectively). (C) Quanzhou 3D printing bridge (the length, width and height of the 3D-printed bridge are 17.5, 3.2 and 3.2 m respectively). (D) World's longest polymer 3D printed bridge, Chengdu Bridge (the total length of the bridge is 66.8 m, of which the 3D printed part is 21.6 m long, the widest section is 8 m and the highest section is 2.7 m). (E) The largest single-story 3D printed building in China, the Visitor Service Center of Nanjing Jiangbei New Area Civic Center (the building area is 286 m2 and the height is 5.2 m). (F) A single-story 3D printed building in China, the 3D Daichuang Activity Center of Nanjing (the building area is 98.5 m2 and the height is 5.6 m). (G, H and I) China's first integrated 3D printed habitable and deliverable two-story building (the building area is 52.8 m2 and the height is 6 m [Citation143]). (Here, the data are based on the statistics of application projects, the same project can be completed by multiple organisations, and the same organisation can also adopt different application modes. Projects using the first application mode can be printed as a whole and then assembled on site; projects using the second application mode are not always printed in whole on site; there are also partial components that are printed on-site or indoors and then assembled. CI: Cincinnati Incorporated; ORNL: Oak Ridge National Laboratory; TJU: Tongji University; SCG: Shanghai Construction Group; SCR: Shanghai Coin Robotics; MB: Mighty building; RO: ROYAL3D; TU/e: Eindhoven University of Technology; LU: Loughborough University; USC: University of Southern California; UGent: Ghent University; TUD: TU Dresden; ETH: ETH Zurich; Winsun: Yingchuang Building Technique; LAG: Liaoning Architecture GreenPrint; NJK: Nanjing Kenyo; SEU: Southeast University; HSG: Henan Space Grey; HEBUT: Hebei University of Technology; CSCEC: China State Construction Engineering Corporation; JTT: Jianyanhua testing (Hangzhou) Technology; ZHA: Zaha Hadid Architects; SMC: Shimizu Corporation; MIT: Massachusetts Institute of Technology; AIS: AI SpaceFactory; BHLT: Beijng Huashang Luhai Technology; THU: Tsinghua University; CIIC: CIIC (Tianjin) Technology; TAM: Twente Additive Manufacturing; B3D: BUILDERA 3D; MU: Monolite UK/ D-shape).](/cms/asset/d23557fd-8b06-4a94-b01d-5de534151342/nvpp_a_2346821_f0005_oc.jpg)
Figure 6. Multifunctional 3D printing processes for LS3DP. (A) Multiscale 3D printing. (B) Multimaterial 3D printing. (C) Multiprocess (or hybrid) 3D printing.
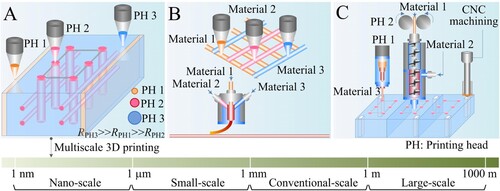
Figure 7. Multiscale multifunctional ink and sustainable materials for LS3DP. (A) Directions for material and structure enhancements. (B) Routes to expanding the printable materials space. (C) Methods for integrated design and printing of materials and structures. (D) Pathways for the development of sustainable materials and structures.
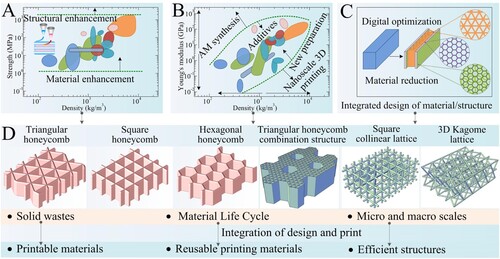
Figure 8. LS3DP equipment for breaking size constraints. (A, B, C and I) Flexible and scalable 3D printing equipment (gantry equipped with robotic arm 3D printing equipment, modular 3-axis adaptive scalable mobile 3D printing equipment [Citation59], mobile swarm [Citation248] collaborative 3D printing robot, and containerised on-site 3D printing mobile factory [Citation59]). (D and E) Horizontal structure 3D printing equipment (horizontal structure multimaterial 3D printing equipment and horizontal structure 3D printing equipment based on printing with follower support via collaborative formwork). (F, G and H) High-rise structure 3D printing equipment (high-rise structure 3D printing equipment with alternate climbing attached to printed structures [Citation59], self-climbing high-rise structure 3D printing equipment [Citation59] and multiple unmanned aerial vehicles carrying cable drive aerial 3D printing robots). (J, K and L) Flexible and multifunctional printing head (the printing head for printing and simultaneous laying of steel reinforcement, the printing head for printing and simultaneous vibrations, and the printing head for printing and external simultaneous compaction).
![Figure 8. LS3DP equipment for breaking size constraints. (A, B, C and I) Flexible and scalable 3D printing equipment (gantry equipped with robotic arm 3D printing equipment, modular 3-axis adaptive scalable mobile 3D printing equipment [Citation59], mobile swarm [Citation248] collaborative 3D printing robot, and containerised on-site 3D printing mobile factory [Citation59]). (D and E) Horizontal structure 3D printing equipment (horizontal structure multimaterial 3D printing equipment and horizontal structure 3D printing equipment based on printing with follower support via collaborative formwork). (F, G and H) High-rise structure 3D printing equipment (high-rise structure 3D printing equipment with alternate climbing attached to printed structures [Citation59], self-climbing high-rise structure 3D printing equipment [Citation59] and multiple unmanned aerial vehicles carrying cable drive aerial 3D printing robots). (J, K and L) Flexible and multifunctional printing head (the printing head for printing and simultaneous laying of steel reinforcement, the printing head for printing and simultaneous vibrations, and the printing head for printing and external simultaneous compaction).](/cms/asset/2f746efb-2c34-406d-8110-28481d96525b/nvpp_a_2346821_f0008_oc.jpg)
Figure 9. Co-printing and feedback control for LS3DP. The core task of LS3DP control is to break through the challenges faced by conventional scale 3D printing and solve the size effect limitations that come with large scale printing. Specifically, it includes the establishment of printing control equations matched with different 3D printing processes, various materials and various equipment, solving the contradiction between accuracy and efficiency, the study of remote collaborative control technology in the whole life cycle of printing, the study of virtual printing and accurate simulation prediction before printing, and the study of monitoring, detection and intelligent control of the whole printing process. With the resolution of these technologies, LS3DP's business model is expected to transform into a global digital cloud 3D printing model, achieving high-precision, high-quality, safe, remote, and fully automated printing.
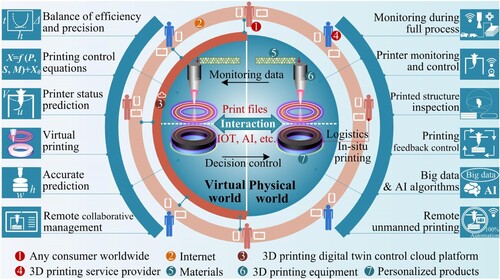
Figure 10. Overall direction of LS3DP. LS3DP can no longer separate material, process, equipment and structural performance, and will develop toward the integration of material and structure, design and construction, and software and hardware.
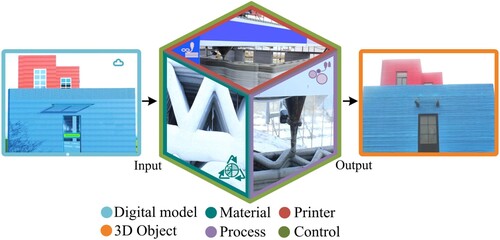
Data availability statement
Data available on request from the authors.