Figures & data
Table 1. Physical and chemical parameters of lithium grease.
Table 2. ZnO nanoparticles content.
Table 3. Si3N4 nanoparticles content.
Table 4. Mixed nanoparticles content.
Table 5. Mixed nanoparticles content.
Figure 6. (a) Friction coefficient vs time at different ZnO contents; (b) Wear scar diameter of steel balls at different ZnO contents.
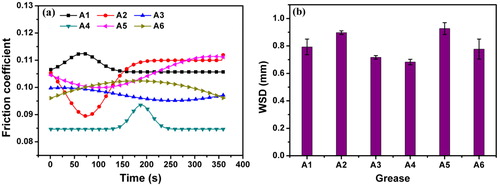
Figure 7. (a) Friction coefficient vs time at different Si3N4 contents; (b) Wear scar diameter of steel balls at different Si3N4 contents.

Figure 8. (a) Friction coefficient vs time at different ZnO-Si3N4 contents; (b) Wear scar diameter of steel balls at different ZnO-Si3N4 contents.
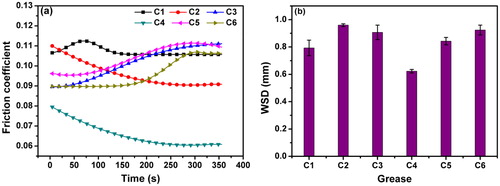
Figure 9. Average reduction (%) of friction coefficient and wear scar diameter of lubricating greases with single and composite nanoparticles.

Figure 10. Wear scar morphology of (a), (c), (e) base grease and (b), (d), (f) composite nanoparticles-based grease.
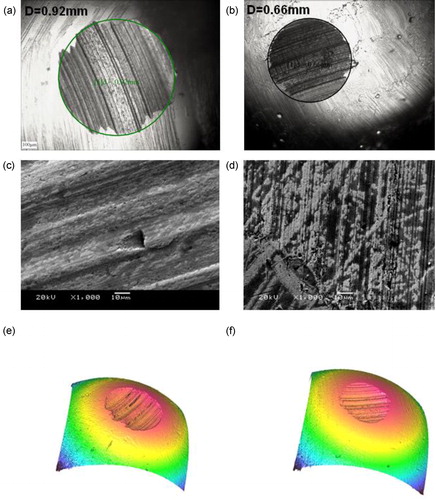
Figure 11. (a) SEM images of wear surface by using base grease and (b) composite nanoparticles-based grease.

Figure 12. (a) Morphology and (b) original wave crest curve of wear surface by using composite nanoparticles-based grease.

Table 6. Surface element distribution.