Figures & data
Figure 1. Time series chart of the prevalence of obesity (BMI > 30) among adults, ages 18+, 1975–2020, in Slovakia. Source: Riley (Citation2022).
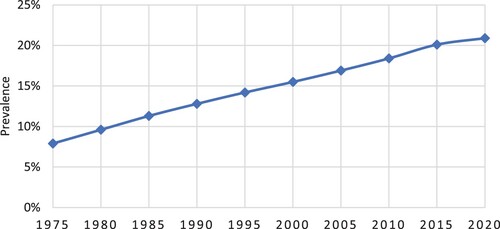
Figure 2. Minimal space required to change the position of the body in the bed comfortably from a centred position: 1TD – to turn in one side, 2TD – to turn in two sides (Wiggermann et al. Citation2017).
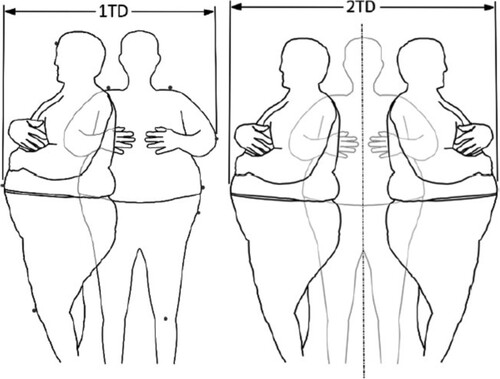
Table 1. Mechanical properties of lamellae (Réh et al. Citation2019).
Figure 4. Scheme of the three-point bending test of the lamella (CEN Citation1993).
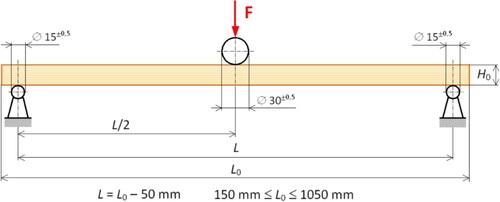
Table 2. Parameters to design the lamella thickness.
Table 3. Descriptive statistics of 225 bariatric respondents.
Figure 6. Force and bending diagrams: (a) spruce wood (h = 20 mm), (b) beech wood (h = 15 mm). The dashed line shows the result of the FEM simulation.
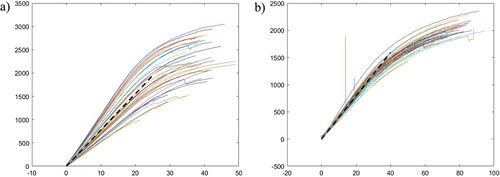
Table 4. Bending characteristics of bed lamellae.
Figure 9. Deflection in three-point bending of beech lamella (board) (board thickness h = 15.3 mm, loading force F = 2500 N).
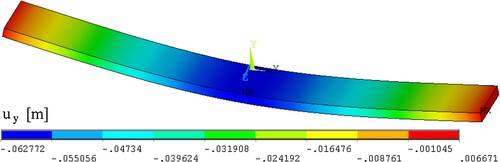
Figure 10. Tensile stress in the fibre direction in the three-point bending of beech lamella (board) (board thickness h = 15.3 mm, loading force F = 2500 N).
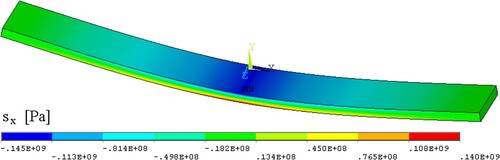