Figures & data
Figure 1. Robohand: the hand that was the inspiration for the development of the global community. Image reproduced with permission from Brod Marsh on behalf of Robohand Australia see http://www.robohand.net/wp-content/uploads/2013/03/2013-03-29-11-10-58-b.jpg, i.e., the copyright holder.
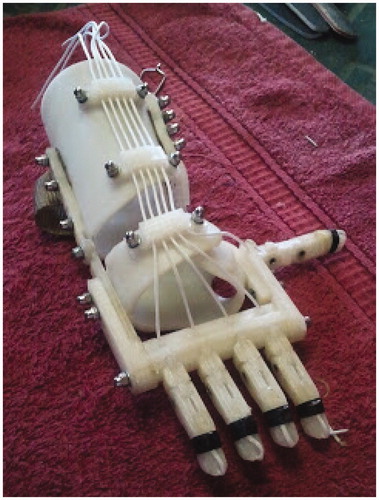
Figure 2. Examples of 3D-printed upper limb prostheses (a) Andrianesis’ Hand: an externally powered forearm prosthesis. Andrianesis and Tzes [Citation1], with permission of Springer. (b) Gosselin’s hand: a body powered forearm prosthesis. Original source: Laliberte et al. No changes made. Reproduced under creative commons attribution 3.0 [3]. (c) Cyborg beast: a body-powered hand prosthesis. Published with permission of Zuniga [Citation21]. (d) Handiii COYOTE: an externally powered forearm prosthesis. ©exiii, Inc. published with permission [Citation34]. (e) IVIANA 2.0: a passive forearm prosthesis. Published with permission of Evan Kuester [Citation37]. (f) Scand: a passive adjustable forearm prosthesis. Original source http://www.instructables.com/id/3D-Printing-Prosthetic-Hand-Make-it-Real-Challen/Scott Allen. No changes made. Reproduced under creative commons attribution 3.0 [Citation57].
![Figure 2. Examples of 3D-printed upper limb prostheses (a) Andrianesis’ Hand: an externally powered forearm prosthesis. Andrianesis and Tzes [Citation1], with permission of Springer. (b) Gosselin’s hand: a body powered forearm prosthesis. Original source: Laliberte et al. No changes made. Reproduced under creative commons attribution 3.0 [3]. (c) Cyborg beast: a body-powered hand prosthesis. Published with permission of Zuniga [Citation21]. (d) Handiii COYOTE: an externally powered forearm prosthesis. ©exiii, Inc. published with permission [Citation34]. (e) IVIANA 2.0: a passive forearm prosthesis. Published with permission of Evan Kuester [Citation37]. (f) Scand: a passive adjustable forearm prosthesis. Original source http://www.instructables.com/id/3D-Printing-Prosthetic-Hand-Make-it-Real-Challen/Scott Allen. No changes made. Reproduced under creative commons attribution 3.0 [Citation57].](/cms/asset/c17c036f-668e-47b5-af76-f4608d4a55bd/iidt_a_1253117_f0002_c.jpg)
Table 1. General specifications and mechanical specifications of the 3D-printed hand prostheses.
Figure 3. Almost two-thirds of the devices are forearm prostheses from which slightly more than half of the devices are externally powered.
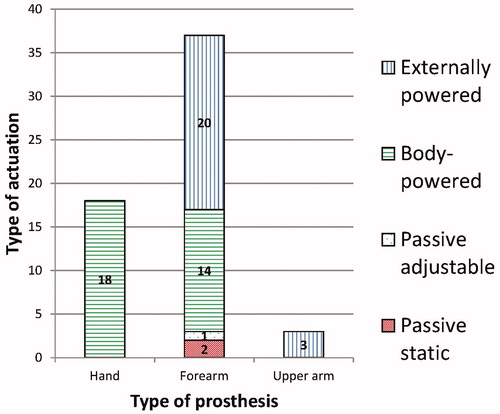
Figure 4. Slightly more than half of all the prostheses are body powered from which slightly more than half of the devices are controlled by the wrist.
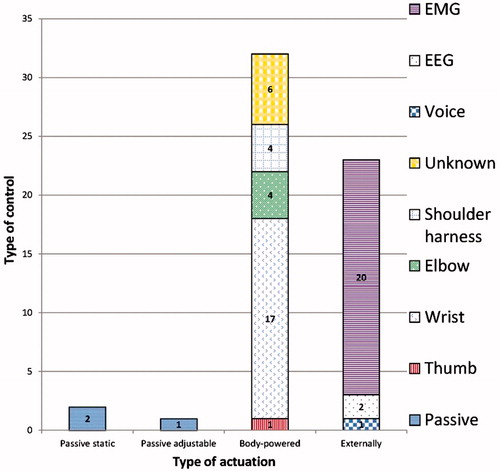
Table 2. Weight of the 3D-printed hand prostheses. Only 11 of the 58 3D-printed upper limb prostheses specified their weights.
Figure 5. More than half of the actuated hands have an equal force between the fingers. Slightly more than a third of the hands have fingers with independent force due to a separate motor for each finger. Only a small number of the hands have a mechanical linkage system to distribute the force along the fingers.
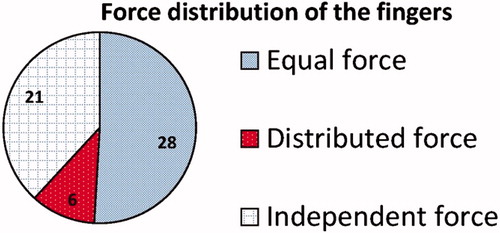
Figure 6. The type of flexor used to close the prosthesis. The majority of the hands use cables or cords to close the hand. The remainder of the hands use mechanical linkages and one uses compressed air.
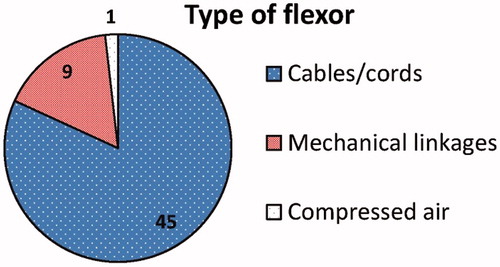
Figure 7. The type of extensor used to open the prosthesis. Almost two-thirds of the hands use elasticity in the form of elastic cords or bands or compliant mechanisms to open the hand automatically.
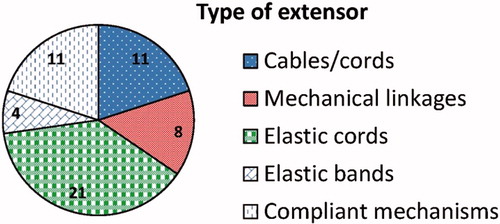
Table 3. Kinematic specifications of the 3D-printed hand prostheses.
Figure 8. The various fabrication methods used to print the prostheses. The majority of the devices are made using FDM technology
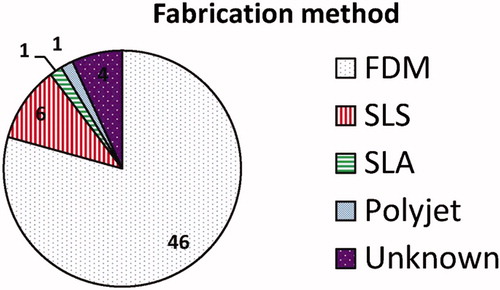
Table 4. Print specifications of the 3D-printed hand prostheses. The first part of the table shows the 3D-printed upper limb prostheses found in scientific literature and the second part of the table shows the devices found with the internet search.