Figures & data
Figure 1. Developed from text by Timo Rissanen (Citation2007), these fashion design processes were developed before 3D software was readily available for fashion design. They articulate some of the design-prototyping processes commonly used in industry.
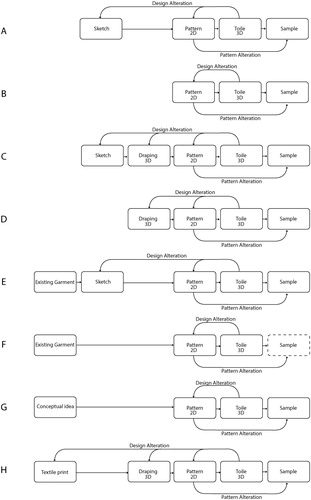
Figure 2. Diagrams showing, for comparison, (A) the basic fashion design process (developed from Rissanen’s (Citation2007) categorisations), (B) a basic zero-waste design process without 3D tools and (C) a basic zero-waste design process using 3D tools. Diagram courtesy of Author.
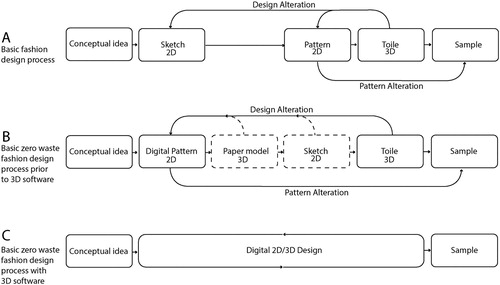
Figure 3. Diagram of a simplified zero-waste design process that is utilised by students during zero-waste workshops that involve 3D software. The integrated digital 2D/2D design process allows for rapid design development with a lower level of perceived risk. Diagram courtesy of Author.

Figure 4. Diagram of a simplified zero-waste design process that was utilised in the industry context described. An existing (physical or digital) pattern can be input into the 3D software and new iterations developed. Digital samples can replace line drawings used in garment specification, and give a highly accurate representation of the real-life outcome. Diagram courtesy of Author.

Figure 5. Diagram of a simplified zero-waste design process that integrates 3D draping into the development of innovative forms. 3D tools can effectively be used to augment existing physical tools while achieving zero-waste outcomes. Diagram courtesy of Author.

Figure 6. Zero + One zero-waste coat as developed through a Drape – Digitise pattern – Digital 2D/3D design – Sample design process. Left is the digital sample, middle is the zero-waste pattern developed alongside the digital sample, and right is the Final sample. Images courtesy of Author, except right image: courtesy of Bonny Beatty.
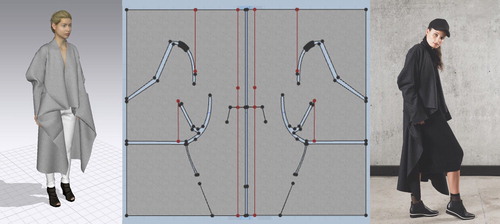
Figure 7. Diagram of a simplified zero-waste design process used for zero-waste whole garment weaving. The use of 3D software enabled the development and visualisation of highly innovative weave-able forms, reducing the risk of wasting time on the loom. Diagram courtesy of Author.

Figure 8. Examples of whole garment weaving digital prototypes as developed through Conceptual Idea – Digital 2D/3D design – Fabric Construction – Sample design process. The 2D pattern, 3D form, 2D textile surface and structure are partially or fully developed through this process. Images courtesy of Author.
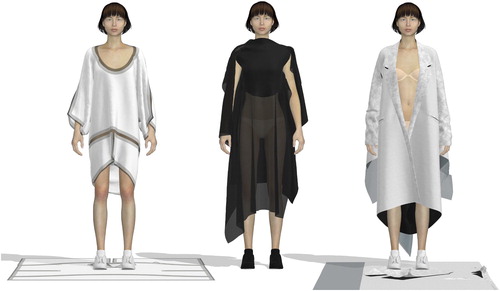
Figure 9. In addition to Rissanen’s (Citation2007) eight design processes, these explore the impact of 3D software in the development of a hybrid, simultaneous and holistic 2D/3D design process. This hybridises the multiple iterative steps of 2D sketching, 3D draping, 2D pattern cutting, and 3D toileing, into a single 2D/3D design process. Diagram courtesy of Author.
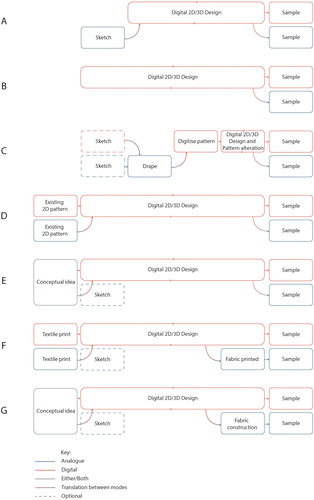