Figures & data
Table 1 Properties of utilised JIS type-II fly ash.
Table 2 JIS recycled aggregate specifications.
Table 3 Properties of sand, rubber crumbs and coarse aggregates.
Table 4 Mix proportions and fresh properties.
Figure 3 Compressive strength development from 7 to 91 days for 0% (top), 25% (middle) and 50% (bottom) rubber crumb replacement ratios.
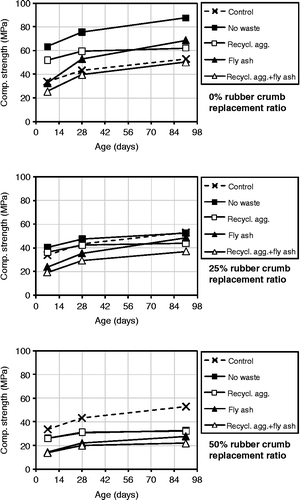