Figures & data
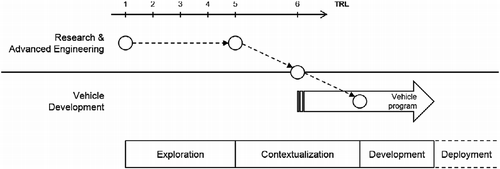
Table 1 List of available LCA results of cars.
Table 2 Example of an expansion strategy in taking the Environment dimension into account.
Table 3 Environmental indicators communicated by car manufacturers.
Table 4 Environmental indicators and flows used in six publications from the automotive sector.
Table 5 Results for the four groups of dendrograms.
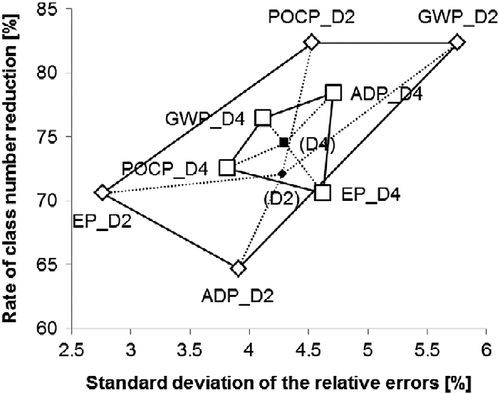
Table 6 Description of the vehicles' clusters for the manufacturing step.
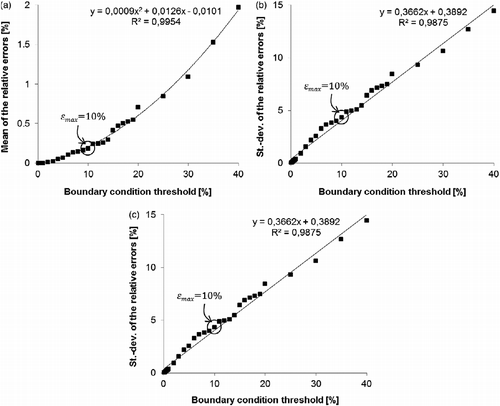
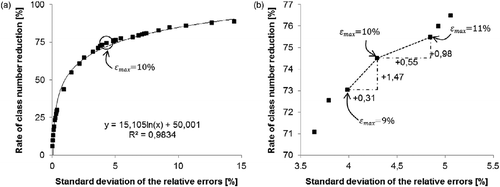
Table 7 List of the omitted vehicles for the 10 simulations.
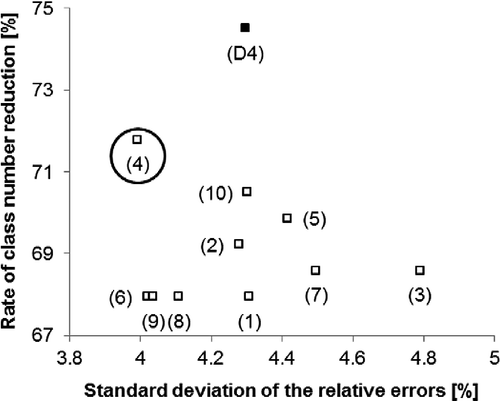
Table 8 Description of the vehicles' clusters for the manufacturing step of the simulation (4).
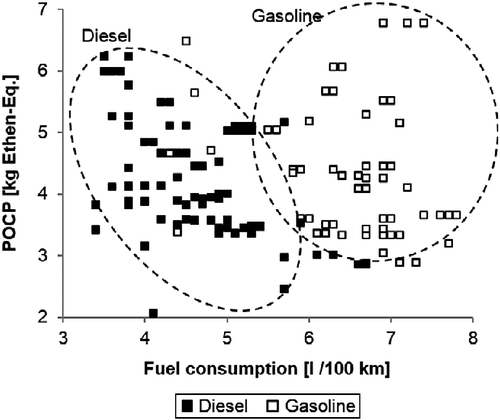