Figures & data
Table 1. Chemical composition of the investigated SAWS (wt%).
Figure 2. XRD of the as-received slag welding flux. CaF2 (F); Mullite (M); Rutile (R); Al2O3 (Al); (Mn2O3)3MnSiO3 (B); Periclase (P); Quartz (Q); Cristobalite (C).
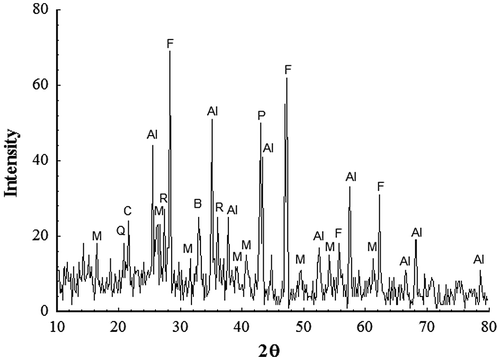
Figure 5. XRD patterns of powder samples of 1% RH sintered for 1 h at the indicated temperatures. D–diopside; J-jacobsite; C-corundum; M-MgAl2O4; P-pyrope; S-SiO2 Z-Ca1.82 Al3.64 Si0.36O8.
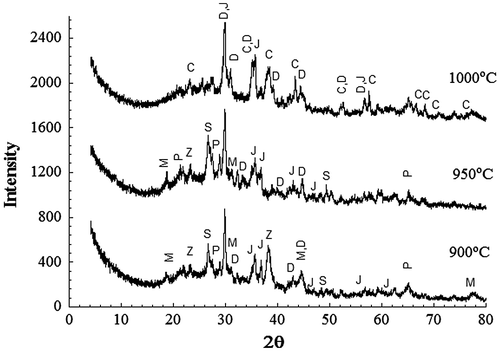
Figure 6. XRD patterns from powder samples of 20% RH sintered for 1 h at the indicated temperatures. D–diopside; J-jacobsite; C-corundum; M-MgAl2O4.
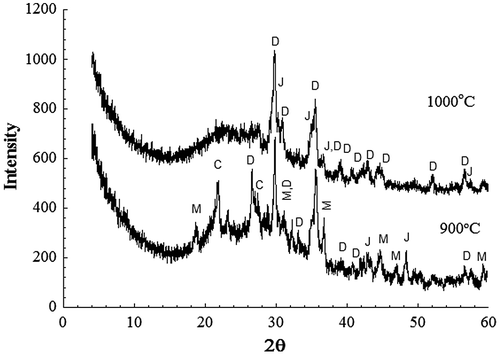
Figure 7. Image aspects of the porous glass–ceramic structures containing 20% RHs and sintered at various temperatures (a) 900 °C, (b) 975 °C, (c) 1000 °C and (d) 1000 °C at 6% RH.
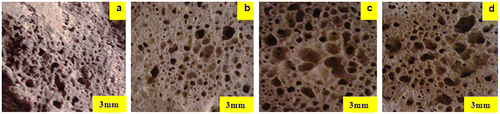
Table 2. Quantitative elemental composition of the crystals in Figure 8.
Table 3. Quantitative elemental composition of the crystals in Figure 9.
Figure 11. Magnetization curves of porous glass–ceramic containing 20% RH and sintered at 1000 °C for 1 h.
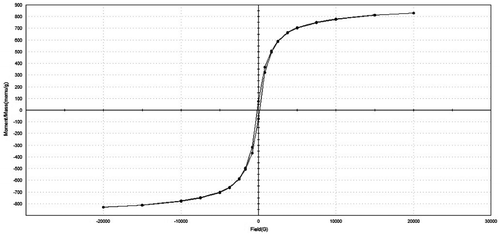