Figures & data
Table 1. Mass ratio of the developed epoxy bio-composites
Plate 3: SEM Image of snail shell derived HAp particles.
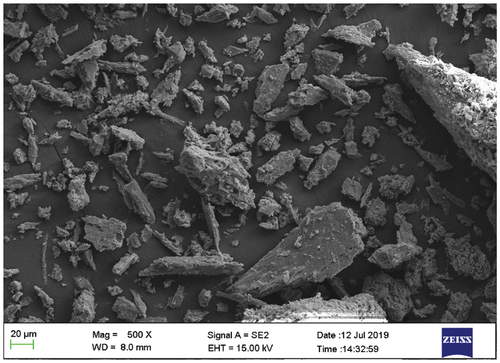
Table 2. XRD diffraction peaks of snail shell-derived HAp particles
Figure 1. Influence of snail shell-based HAp particles on the tensile stress–strain curve of the developed bio-composites and the control.
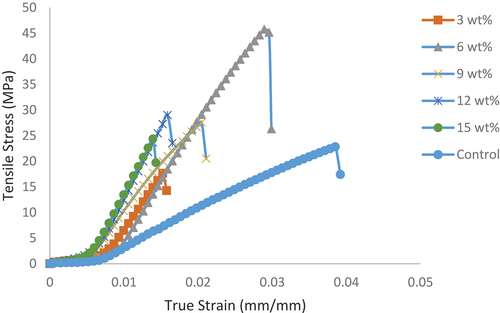
Figure 2. Effect of the addition of snail shell-based HAp particles on the tensile properties of epoxy bio-composites.
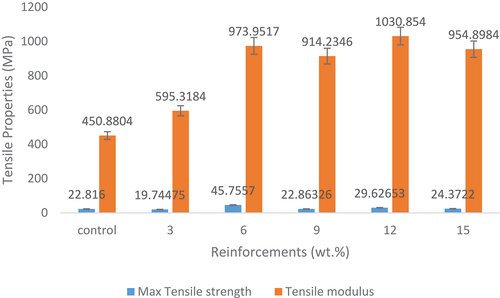
Figure 3. Tensile strain at maximum tensile strength of the control and snail shell-based HAp reinforced samples.
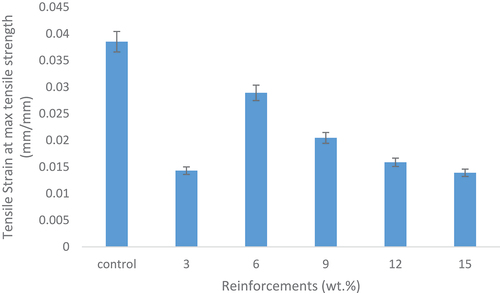
Figure 5. Flexural strain at maximum flexural strength of the control and snail shell-based HAp reinforced samples.
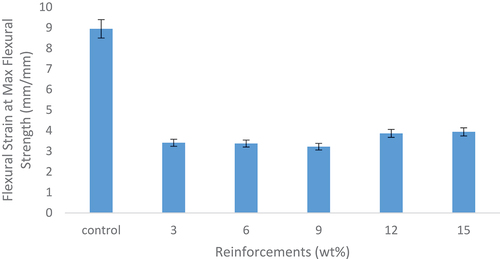
Figure 6. Effects of the addition of snail shell-based HAp particles on hardness property of the samples.
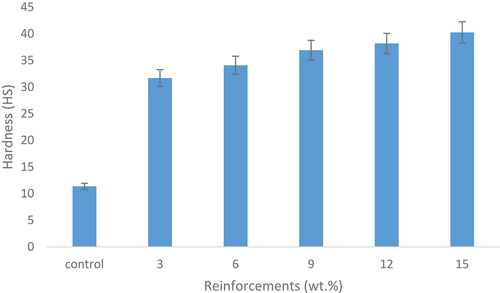
Figure 7. Effect of the addition of snail shell-based HAp particles on the impact energy of the developed bio-composites and the control.
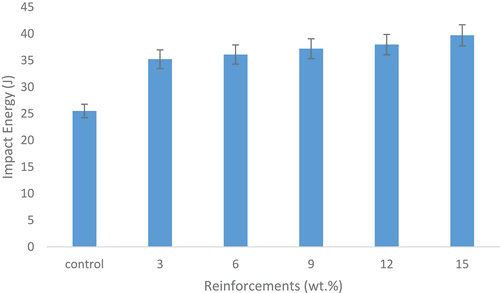
Plate 6: Bio-composite sample with 3 wt.% snail shell derived HAp.

Plate 7: Bio-composite sample with 6 wt.% snail shell derived HAp.
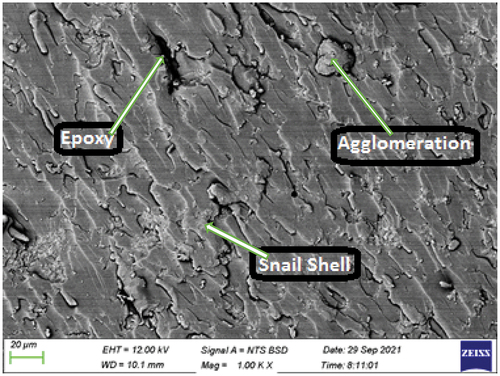
Plate 8: Bio-composite sample with 9 wt.% snail shell derived HAp.
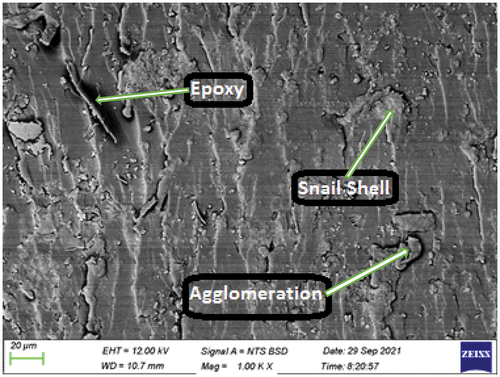
Plate 9: Bio-composite sample with 12 wt.% snail shell derived HAp.
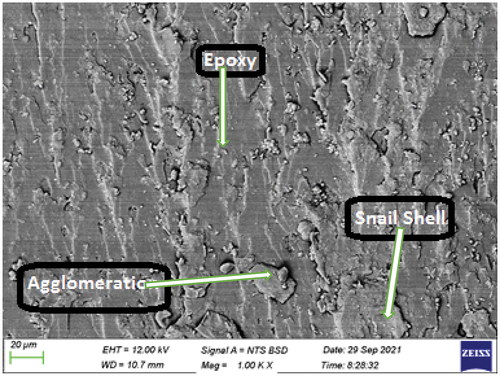
Plate 10: Bio-composite sample with 15 wt.% snail shell derived HAp.
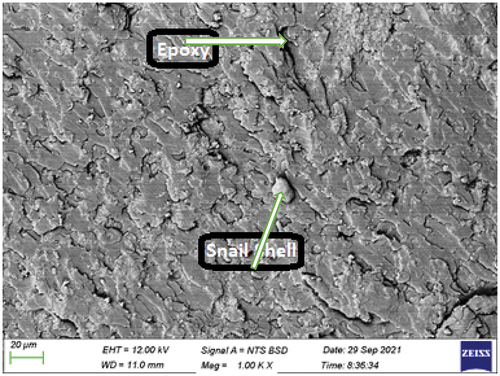