Figures & data
Table 1. Properties of carbon black grades used in the study.
Table 2. Additives used for mathematical migration modelling.
Figure 6. Signal of the 90° MALLS detector of Printex® 80 (50 µg l–1) overlaid with the solvent blank (black dots) and the calculated radii of gyration per elution time (grey dots).
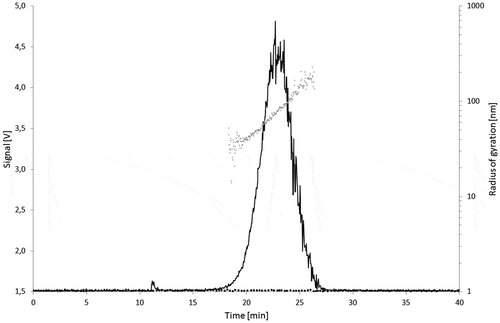
Figure 7. Signal of the 90° MALLS detector of Printex® 85 (50 µg l–1) overlaid with the solvent blank (black dots) and the calculated radii of gyration per elution time (grey dots).
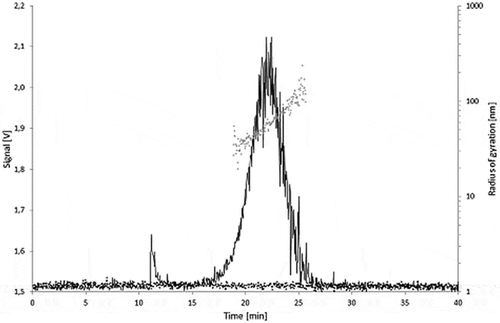
Figure 8. Fractograms of the LDPE migration samples: 5.0% Printex® 80 in LDPE, 5.0% Printex® 85 in LDPE and LDPE blanks of the isooctane (24 h/40°C) and 95% ethanol (10 days/60°C) migration samples.
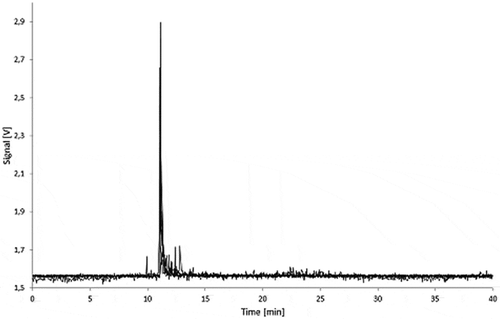
Figure 9. Fractograms of the LDPE migration samples: 5.0% Printex® 80 in LDPE, 5.0% Printex® 85 in LDPE and LDPE blank of 3% acetic acid (10 days/60°C) migration samples.
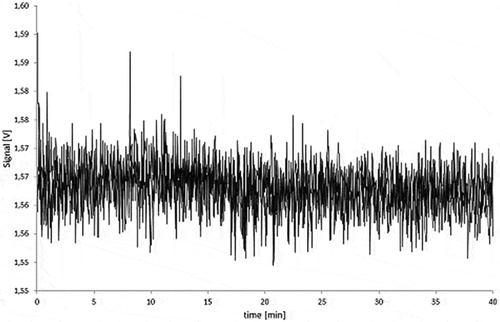
Figure 10. Fractograms of the PS migration samples: 5.0% Printex® 80 in PS, 5.0% Printex® 85 in PS and PS blanks of the isooctane (24 h/40°C), 95% ethanol (10 days/60°C) migration samples.
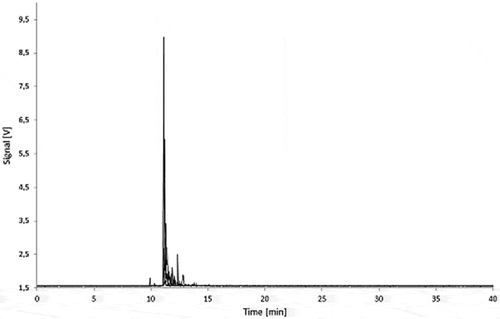
Figure 11. Fractograms of the PS migration samples: 5.0% Printex® 80 in PS, 5.0% Printex® 85 in PS and PS blank of 3% acetic acid (10 days/60°C) migration samples.
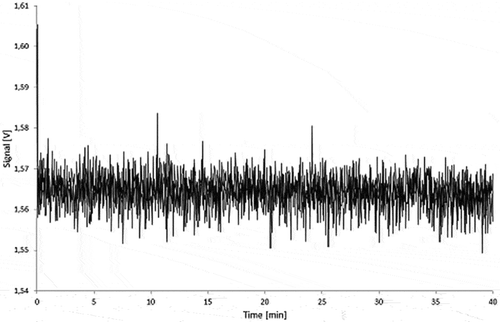
Figure 12. 5.0% Printex® 85 in LDPE migration sample (10 days/60°C in 95% ethanol): untreated (black) and spiked with 50 µg l–1 of Printex® 85 (grey).
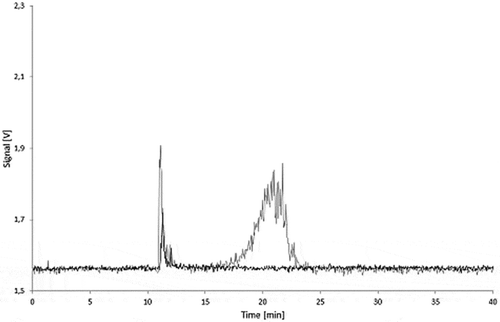
Figure 13. 5.0% Printex® 80 in PS migration sample (24 h/40°C in isooctane): untreated (black) and spiked to 25 µg l–1 with Printex® 80 (grey).
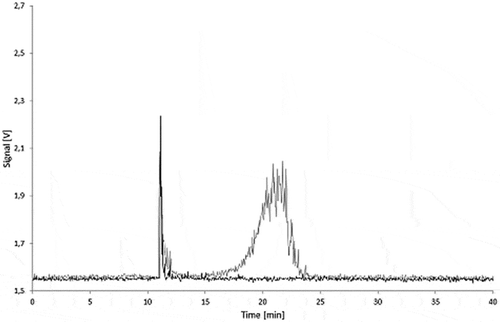
Figure 14. Sequential dilution of Printex® 80: blank, 10, 25, 50, 100 and 250 µg l–1; signal of the 90° MALLS detector.
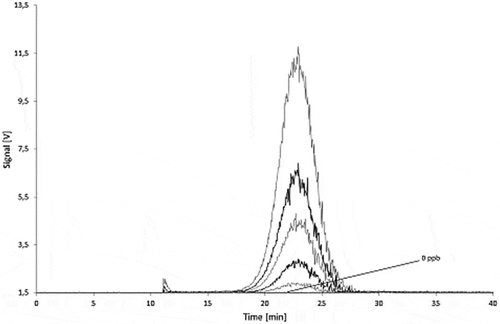
Figure 15. Sequential dilution of Printex® 85: blank, 10, 25, 50, 100 and 250 µg l–1 signal of the 90° MALLS detector.
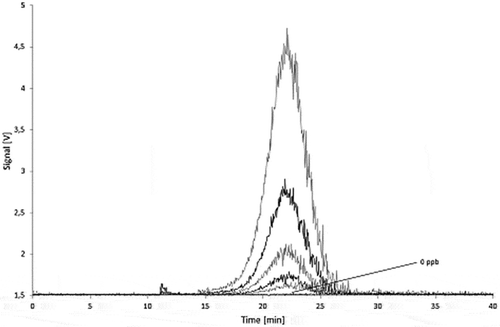
Figure 16. Calibration curve for Printex® 80: total MALLS output versus concentration of standard (1000 µl injections) with relative standard deviations.
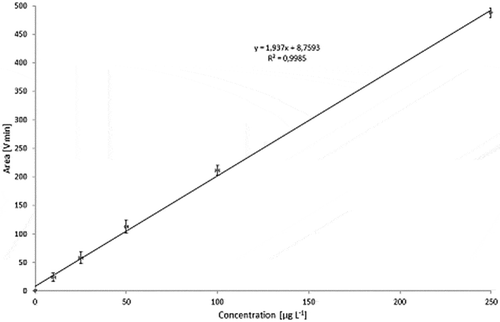
Figure 17. Calibration curve for Printex® 85: Total MALLS output versus concentration of standard (1000 µl injections) with relative standard deviations.
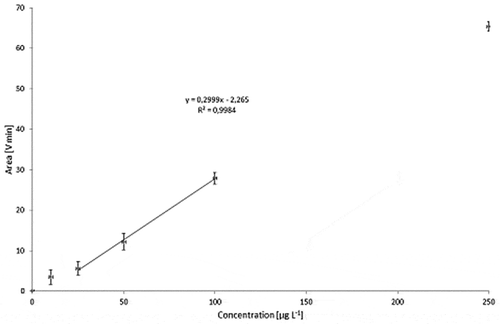
Figure 18. Stability of a Printex® 80 dispersion in 95% ethanol: signal of the 90° MALLS detector of a freshly prepared dispersion (black) and of a dispersion stored for 10 days at 60°C (grey).
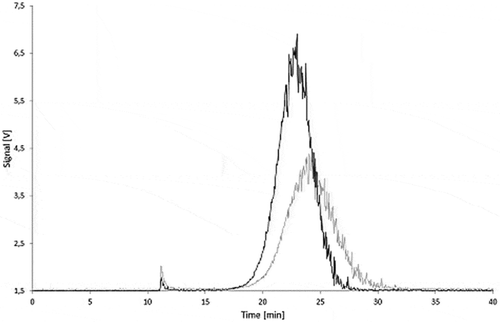
Figure 19. Stability of a Printex® 85 dispersion in 95% ethanol: signal of the 90° MALLS detector of a freshly prepared dispersion (black) and of a dispersion stored for 10 days at 60°C (grey).
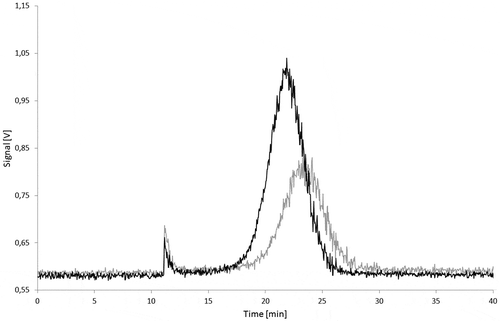
Table 3. Stability of carbon black in 95% ethanol at migration conditions (1000 µl injections of 100 µg l−1 dispersions).
Table 4. Stability of carbon black in isooctane and 3% acetic acid at migration conditions (1000 µl injections of 100 µg l−1 dispersions).
Table 5. Migration modelling of three additives in relation to their molecular size (plaques 3 mm, 5% additive concentration, 10 days/40°C, K = 1, surface to volume ratio 6 dm2 kg−1).
Table 6. Comparison of diffusion coefficients at 25°C obtained according to Simon et al. (Citation2008) with that according to the modelling guideline (Simoneau Citation2010).