Figures & data
Table 1. Evolution of yield stress with plastic strain
Figure 1. (Color online). Comparison of experimentally obtained stress–strain curves with the simulation of a combined isotropic/kinematic hardening plasticity model.
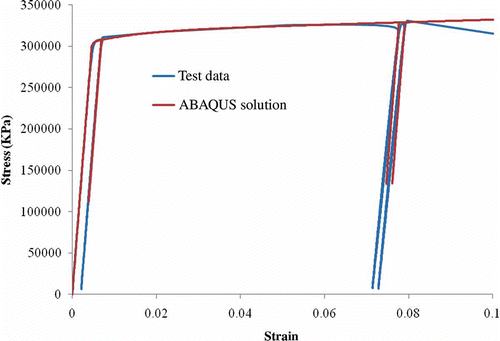
Figure 4. (Color online). Load–displacement comparison for elastic indentation simulation into a specimen with r s = 18 μm and h s = 30 μm.
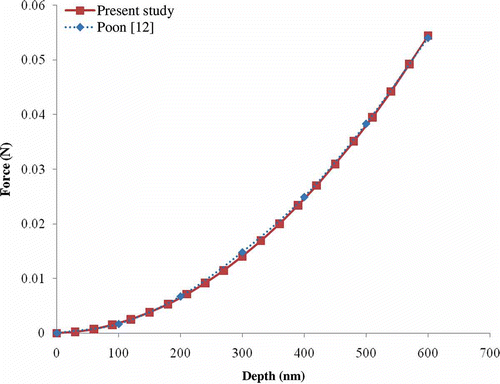
Figure 5. (Color online). Load–displacement comparison for elastic indentation simulation into a specimen with varying indenter tip radii, ρ (30, 705, 120, 150 and 200 nm).
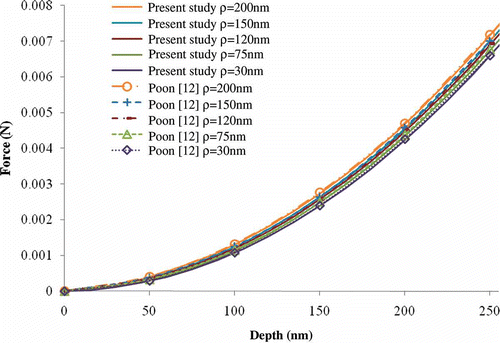
Figure 6. (Color online). Load–displacement curves for elastic indentation simulation into a specimen with r s = 18 μm and varying h s (18, 30, 42, 60, 92 and 120 μm).

Figure 7. (Color online). Comparison of the simulations using different 2D axisymmetric finite element meshes in elastoplastic indentation.
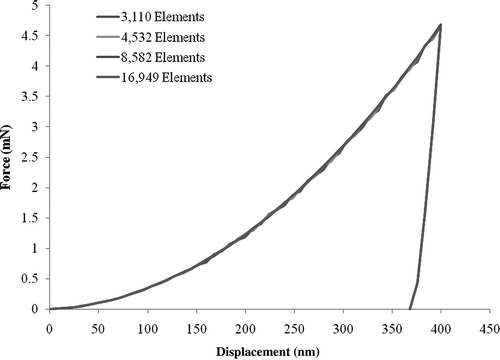
Figure 10. Local top surface details of the modified 3D finite element mesh configured to improve interaction with Berkovich indenter.
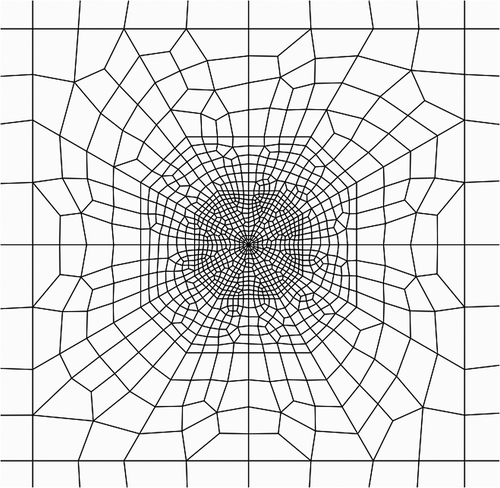
Figure 12. (Color online). Comparison of load–displacement curves for 2D and 3D conical indentations.
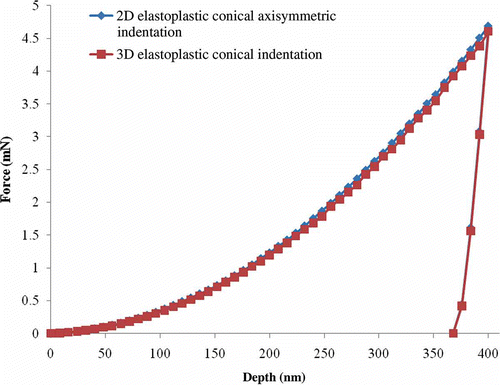
Figure 13. (Color online). Comparison of load–displacement curves for conical and Berkovich indentations.
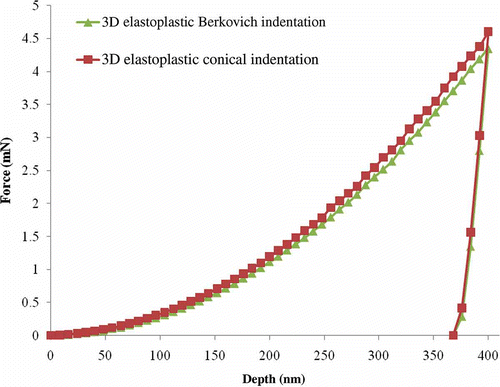
Figure 14. (Color online). Comparison of contact areas computed in conical and Berkovich indentations.
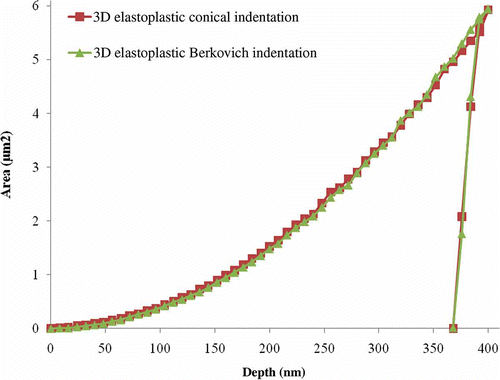
Figure 15. (Color online). Comparison of normalized contact stresses computed for conical and Berkovich indentations.
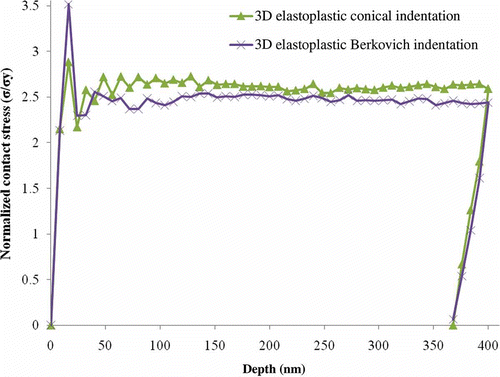
Figure 16. (Color online). Mises stress for (a) 70.3° conical indenter, (b) Berkovich indenter, viewed in plane perpendicular to indenter edge, and (c) Berkovich indenter, viewed in plane of indenter edge. (Figure continued).
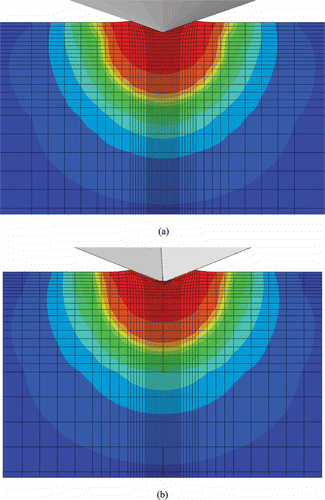
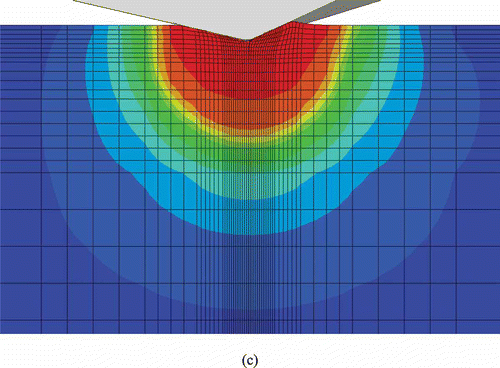