Figures & data
Figure 1. Position of mine and layout of working face: (a) test site position; (b) borehole column diagram of working face; (c) layout of working face; and (h) A-a side.
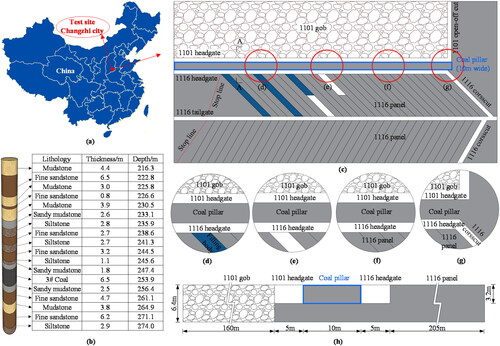
Table 1. The mechanical parameters of model.
Table 2. Calculation coefficient of average height of caving zone.
Table 3. Stress-strain Relationship of gob materials.
Table 4. The mechanical parameters of materials in gob.
Figure 12. Strain-softening model correction: (a) numerical calculation model; (b) stress-strain curves of coal pillar with different width-height ratios; and (c) comparison of stress peaks with different width-height ratios.
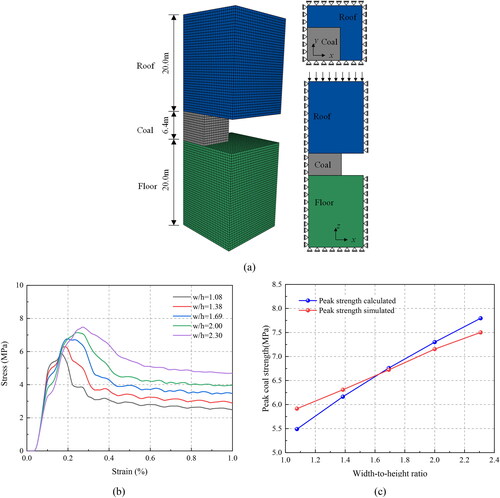
Table 5. The strain-softening model parameters of coal pillar materials.
Figure 13. The validation of global model: (a) GYW80 intrinsically safe surrounding rock stress sensor for mining; (b) the layout of field measured points; and (c) comparison between numerical simulation and field measured results.
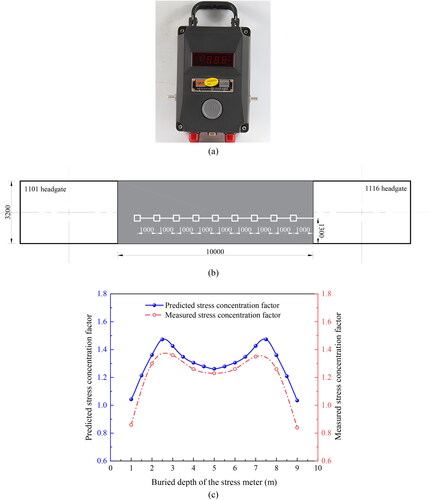
Figure 14. Vertical stress of two ribs during the mining of 1101 panel: (a) the distribution of plastic zone in working face; (b) vertical stress curves inside coal pillar; and (c) vertical stress curves of solid coal side.
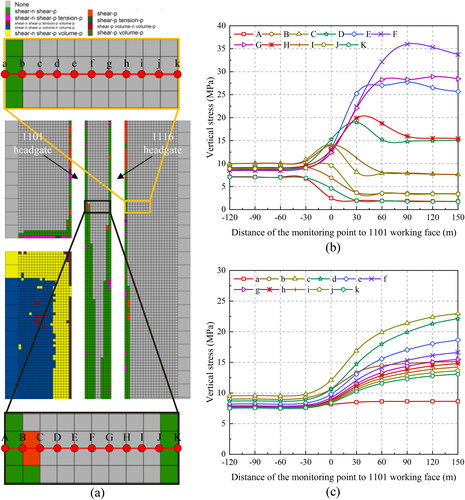
Figure 15. The plastic zone and stress distribution: (a) -120 m; (b) -90 m; (c) -60 m; (d) -30 m; (e) 0 m; (f) +30 m; (g) +60 m; (h) +90 m; (i) +120 m; and (j) +150 m.
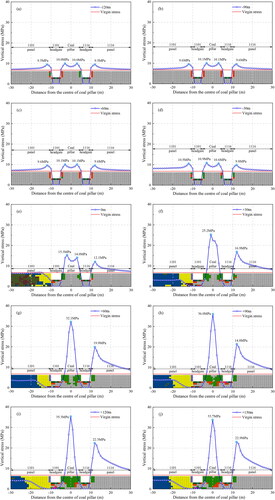
Figure 16. Stope of stress distribution during mining 1116 panel: (a) filling 160 m in stage I; (b) filling 300 m in stage I; (c) filling 160 m in stage II; (d) filling 300 m in stage II; (e) filling 160 m in stage III; (f) filling 300 m in stage III; (g) filling 160 m in stage IV; and (h) filling 300 m in stage IV.
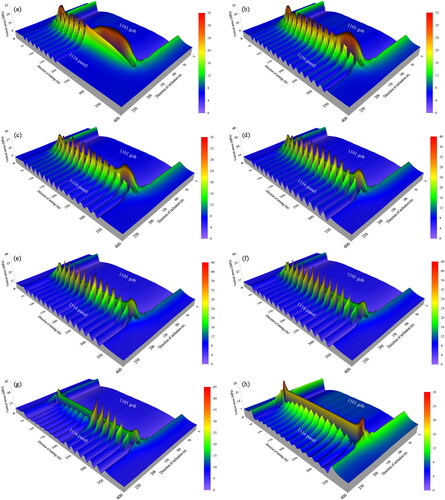
Data availability statement
Data will be made available on request.