Figures & data
Figure 2. (a) The two tetrahedrons e and ep satisfy the EDP. (b) The two tetrahedrons do not satisfy the EDP.
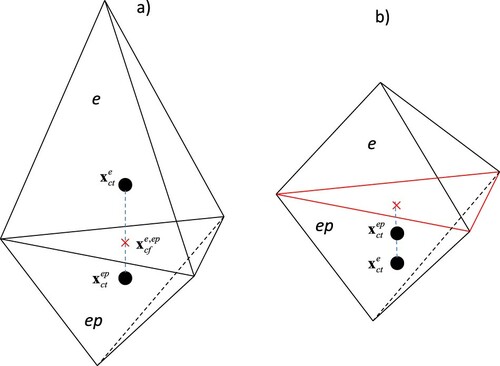
Figure 4. Solution of a single time step. (a) Scheme of the parallel solution of the MAST-fs (or MAST-bs). (b) Scheme of the parallel solution of traditional MArching in Time method (MTM).
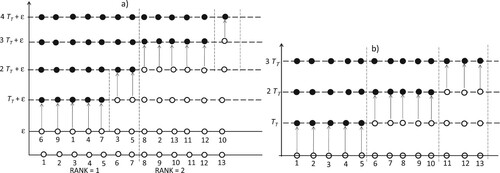
Figure 6. (a) 2D sketch of case = NT,m – 1. (b) 2D sketch case of
= NT,m. Blue solid lines are traces of the external faces of the cluster, and red dashed lines are traces of the internal faces of the cluster.
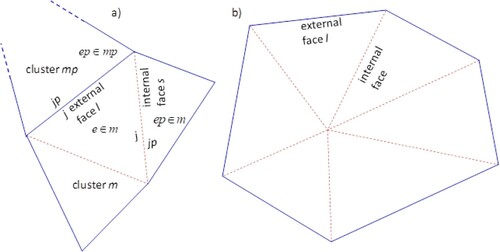
Table 1. Test 1. L2 norms of relative errors and spatial rate of convergence.
Table 2. Test 1. L∞ norms of relative errors and spatial rate of convergence.
Figure 8. Test 1. Investigation of the spatial and temporal accuracy. (a) Norms of relative errors vs. mean mesh size, (b) norms of relative errors vs. time step size.
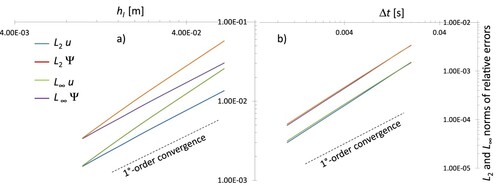
Table 3. Test 1. L2 norms of relative errors and time rate of convergence.
Table 4. Test 1. L∞ norms of relative errors and time rate of convergence.
Figure 10. Test 2. (a) set-up of the numerical test and BCs. (b) section of the mesh with a cutting plane.
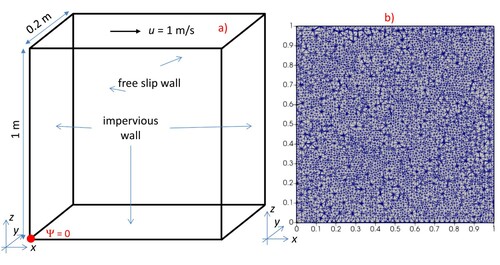
Figure 11. Test 2. Velocity streamlines (left panels), vorticity (ωz) (central panels), iso (kinematic) pressure (right panels). Top Re = 100, middle Re = 400, bottom Re = 1000.
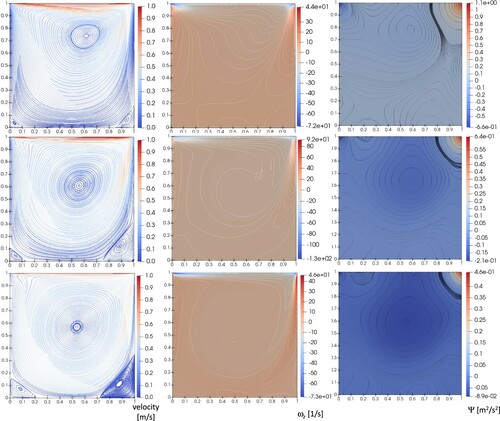
Figure 12. Test 2. x velocity component (top panel), z velocity component (bottom panel) (Nomenclature ‘Ref.’ are the results by Ghia et al. Citation1982).
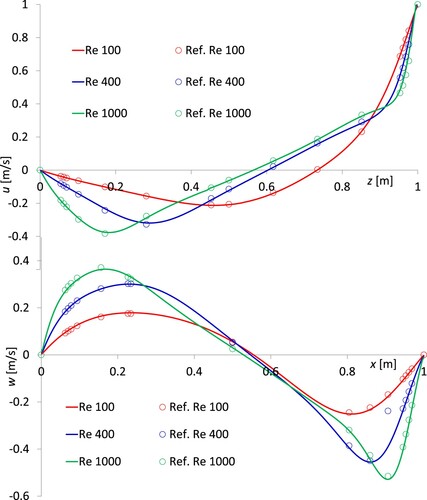
Figure 13. Test 3. Pattern of vortex shedding. Left panels Re = 300, (a) side view, (b) upper view. Right panel (c) 480 < Re < 800 (from Sakamoto & Haniu Citation1990)).
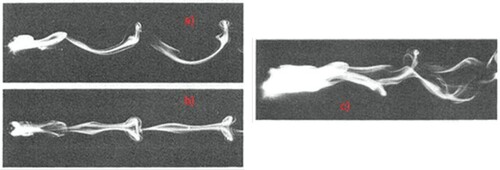
Table 5. Test 3. Values of the drag and lift coefficients.
Figure 17. Test 3, Re = 300. Periodic time evolution of the velocity streamlines (left panels) and kinematic pressure (right panels), (x–z) plane.
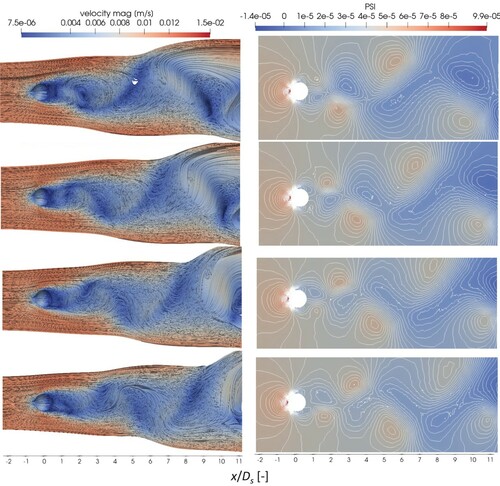
Figure 18. Test 3, Re = 300. Periodic time evolution of the velocity streamlines (left panels) and kinematic pressure (right panels), (x–y) plane.
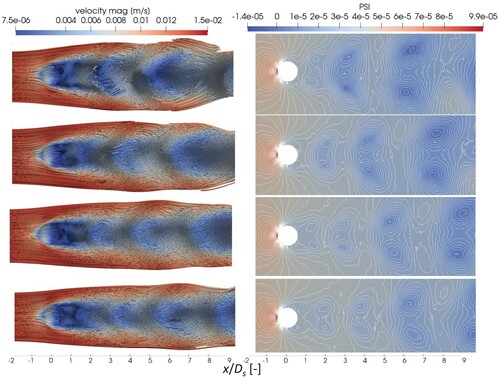
Figure 19. Test 3, Re = 600. (a) 3D vortical structure at τ* = 35. (b) Time evolution of the drag, lift and side coefficients.
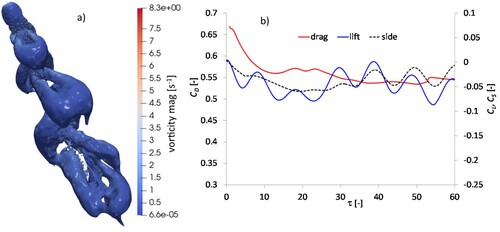
Table 6. MAST solution time vs. no. of processors.
Figure 20. (a) Test 4. Real and computational domain. (b) computational mesh. (c) Section of the mesh with a generic plane.
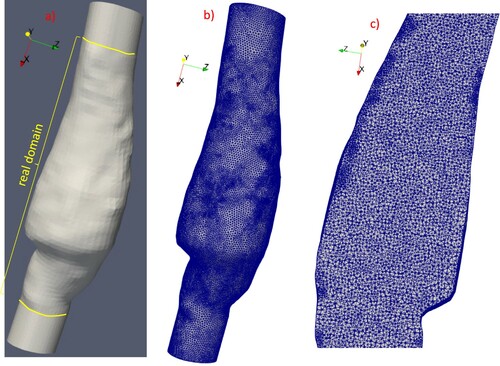
Figure 21. Test 4. (a) waveforms of mean-in-time inflow velocity and outlet pressure. (b) Womersley inflow velocity profiles at four significant times (from Aricò et al., Citation2020).
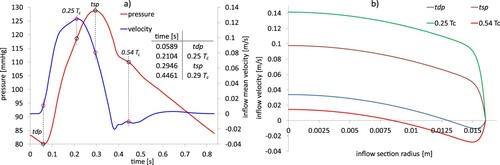
Figure 22. Test 4. Computed velocity vectors and kinematic pressure at the significant times in Figure .
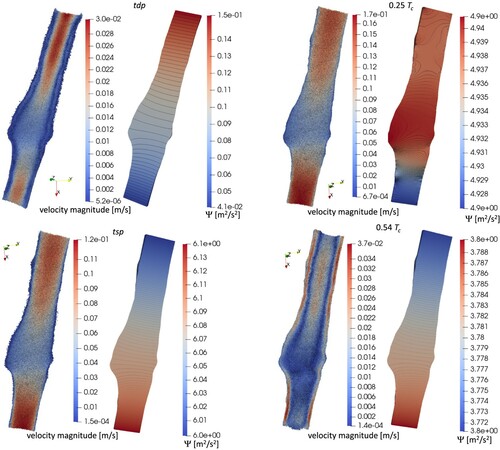