Figures & data
Table 1. The three-cavity MMR micropump variables.
Figure 2. A schematic of the three-cavity MMR micropump at the beginning of the four steps of a pump cycle.
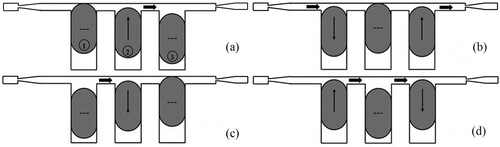
Figure 3. The electric current imposed to the (a) first, (b) second, and (c) third mercury slug during the four steps of the MMR micropump pumping cycle with . When the current is in the
and
direction, it has a positive and negative sign, respectively.
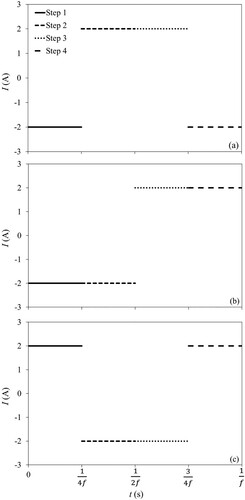
Table 2. Physical properties of air and mercury at .
Figure 4. The volume fraction contours, where the red and blue colors represent volume fractions of 1 (mercury) and 0 (air), respectively, for the four cases with (a) 17,880, (b) 40,302, (c) 72,100, and (d) 161,790 number of cells.
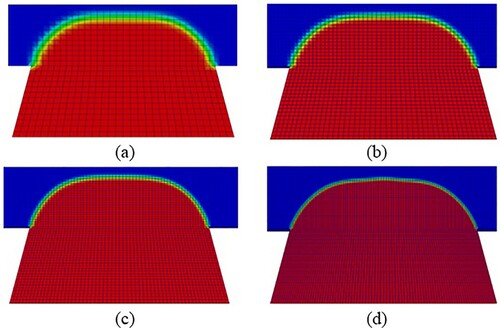
Table 3. Computational grid sensitivity study data.
Table 4. The micropump mean pumping flow rate predictions based on different maximum Courant numbers.
Figure 5. (a) The comparison of the MMR micropump pumping flow rate estimated by the numerical estimations with the experimental measurements (Karmozdi et al., Citation2013) at different back-pressures. (b) A schematic of a mercury slug in a rectangular channel.
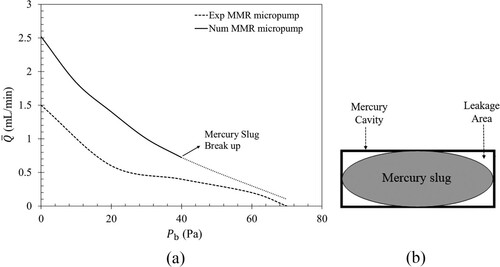
Table 5. The experimental prototype variables.
Figure 6. The comparison of the outlet flow rate of the MMR micropump with an excitation frequency of 10 Hz at a back-pressure of 10 Pa when the phase difference value is 90 and 120
.
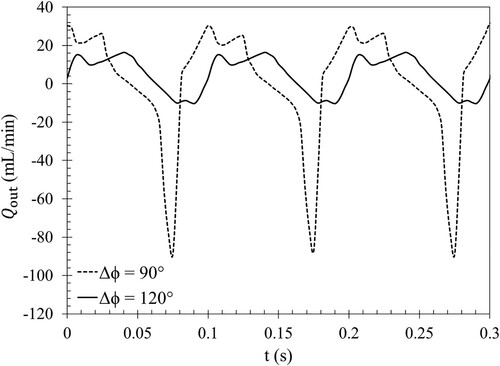
Figure 7. The variation of the mean flow rate of the MMR micropump with an excitation frequency of 10 Hz at a back-pressure of 10 Pa as a function of the electric current phase difference.
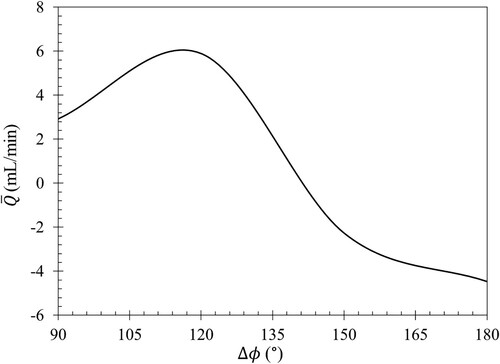
Figure 8. The mercury slugs configuration during the operation of the micropump with a frequency of 10 Hz and a phase difference of 30 at a back-pressure of 10 Pa.
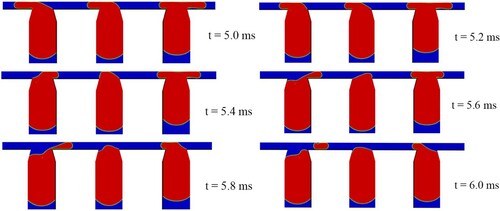
Figure 9. A snapshot at 0.14 s of the pressure contours of the micropump with a frequency of 10 Hz and a phase difference of 120 at a back-pressure of 30 Pa.
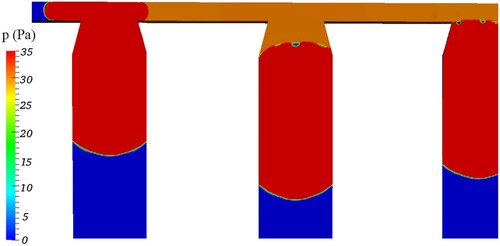
Figure 10. The time evolution of the outlet flow rate of the three-cavity MMR micropump with a phase difference of (a) 90 and (b) 120
and an excitation frequency of 10 Hz as a function of back-pressure.
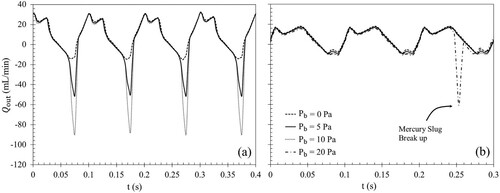
Figure 11. The mean flow rate of the micropump with an excitation frequency of 10 Hz as a function of the back-pressure for phase differences of 90 and 120
.
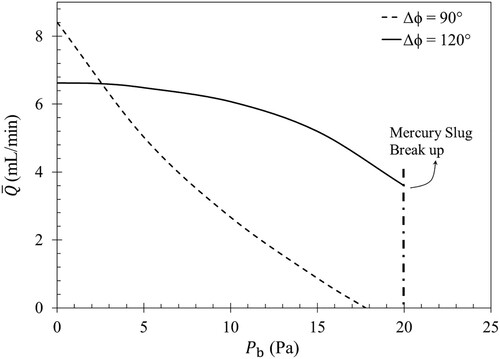
Table 6. The mean reverse flow rate of diffuser/nozzle valves at a back-pressure of 1.2 Pa as a function of their length and angle.
Figure 12. Comparison of three-cavity MMR micropump with and without the diffuser/nozzle valve in frequency of 10 Hz and phase difference of 90.
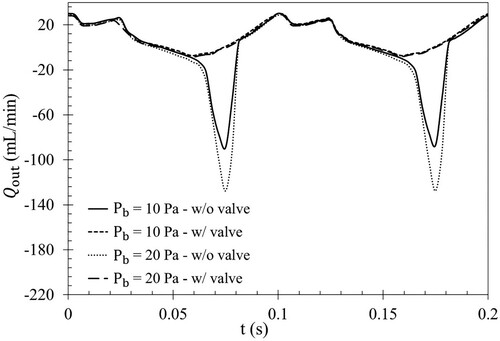