Figures & data
Figure 1. Dust explosion of conventional DTH air hammer drilling (left) and fine dust control performance of reverse circulation DTH air hammer drilling (right).
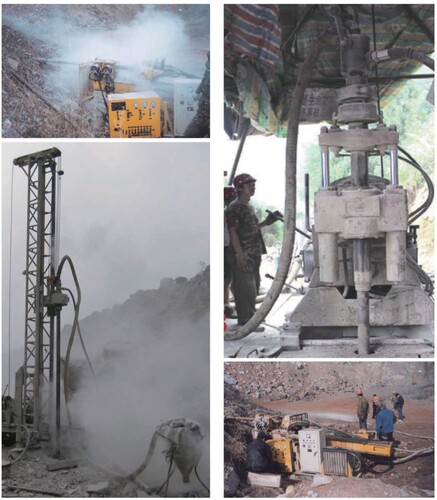
Table 1. Analysis of grid sensitivity and grid type.
Figure 3. (a) Influence of air compressibility on the suction capacity. (b) Influence of the input air volume flow rate using compressible air (ideal gas) on suction capacity.
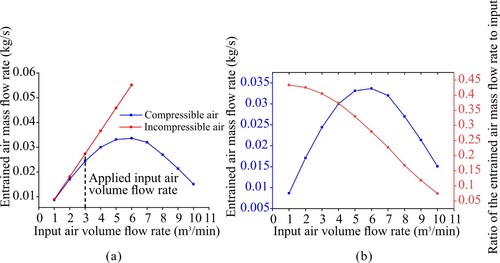
Table 2. Part of parameters used in the simulations.
Figure 6. Typical distribution of cuttings: (a) volume fraction contour plot of X-Y section, (b) streamline distribution plot of X-Y section, (c) volume rendering of isometric view, (d) volume fraction contour plot of bottom borehole, and (e) streamline distribution plot of bottom borehole.
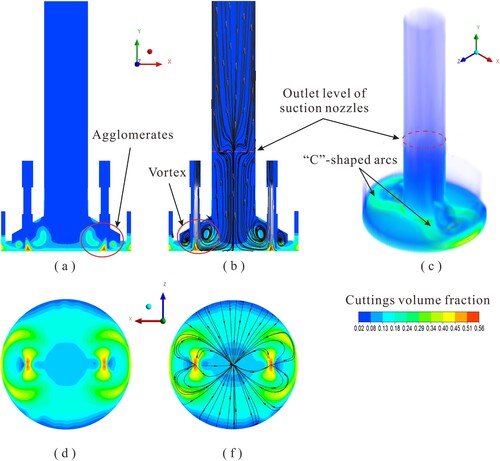
Figure 8. (a) Effect of the input air volume flow rate on the suction capacity. The negative values represent the air released to the atmosphere from the annular gap. (b) Static pressure distribution along the centerline.
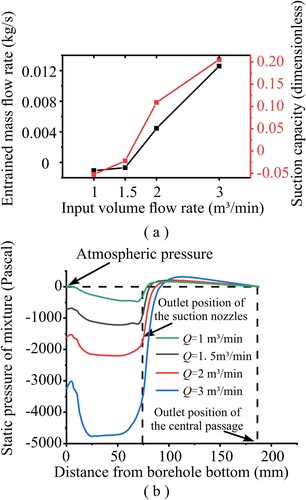
Figure 10. Volume fraction contour plots showing the distribution of cutting particles with different rotary speed (Y = 2 mm).
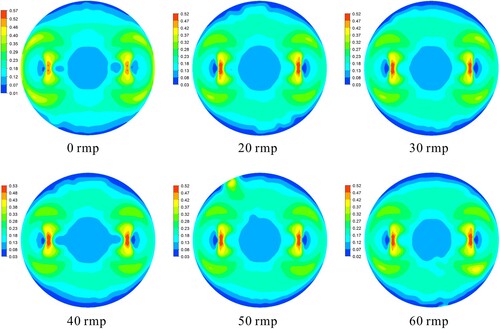
Figure 11. Volume fraction line plots showing the distribution of cutting particles in radial position with different rotary speed (Y = 2 mm).
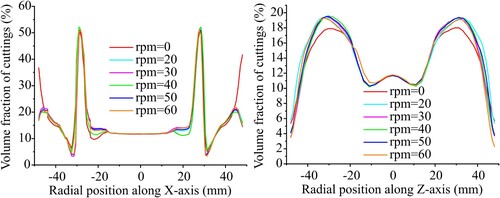
Figure 12. Volume fraction contour plots showing the distribution of cutting particles with different feed concentration: (a) Y = 2 mm, (b) Y = 4 mm, (c) Y = 6 mm, (d) X-Y section.
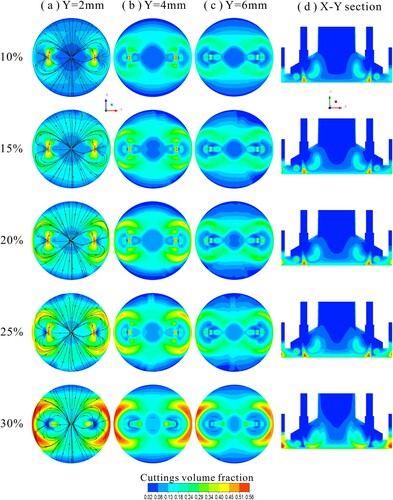