Figures & data
Figure 1. The representation of the proposed unit, (a) three-dimension of the domain, (b) axisymmetric two-dimension as the simulated model.

Table 1. Fins sizes of the examined cases involving the number, length, thickness, and angle of the Y-fins head.
Table 2. Thermophysical characteristics of the PCM applied in this work, GmbH (Najim et al., Citation2022; Rubitherm, Citation2022).
Table 3. Impact of mesh and time step sizes on the melting period.
Figure 5. Melting time of the present work and the work of Longeon et al. (Citation2013).
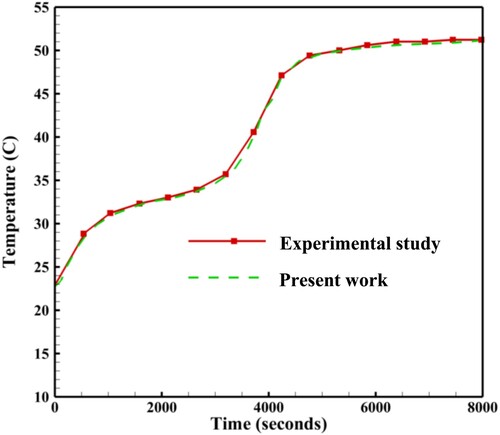
Figure 6. The PCM liquid and solid fractions for cases 0 and 2 (Straight and Y-shaped fins) at different times.
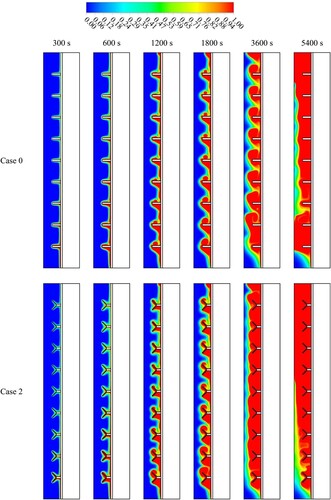
Figure 7. The PCM temperature profiles for the cases 0 and 2 (Straight and Y-shaped fins) at different time.
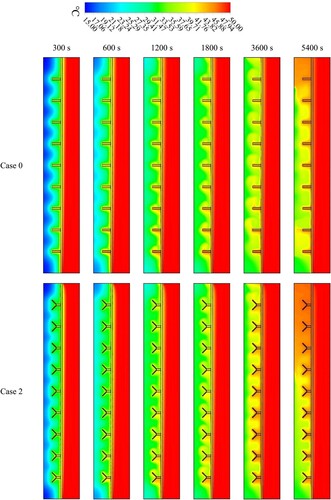
Figure 9. Development of the liquid fraction of the PCM for cases 0 and 2 (Straight and Y-shaped fins).
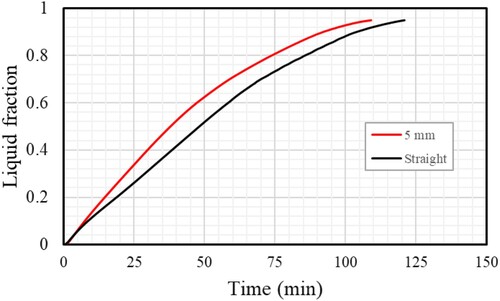
Figure 10. Development of the PCM temperature profile for cases 0 and 2 (Straight and Y-shaped fins).
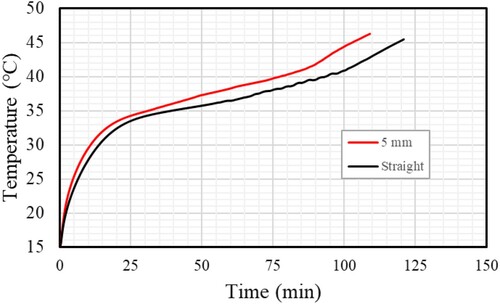
Figure 11. The melting period and the thermal storage rate of the PCM for cases 0 and 2 (Straight and Y-shaped fins).

Figure 12. The liquid and solid fractions of the PCM for the system with Y-shaped fins with various lengths at different time steps.
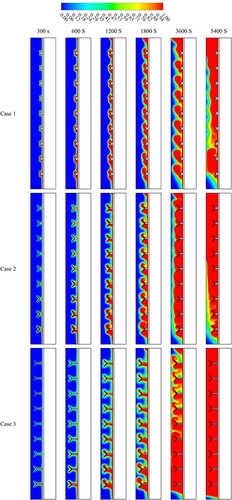
Figure 13. The temperature distributions of the PCM for the system with Y-shaped fins with various lengths at various time steps.
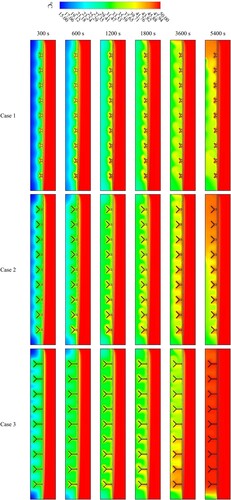
Figure 19. The PCM temperature distributions for cases 3, 4 and 5 using various angles of the fin’s tributaries at various times.
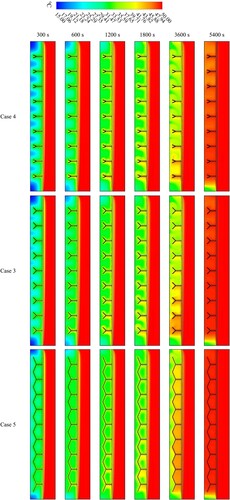
Figure 20. The PCM velocity counter for case 3, 4 and 5 with various angles of the fin’s tributaries at the 3600 s.
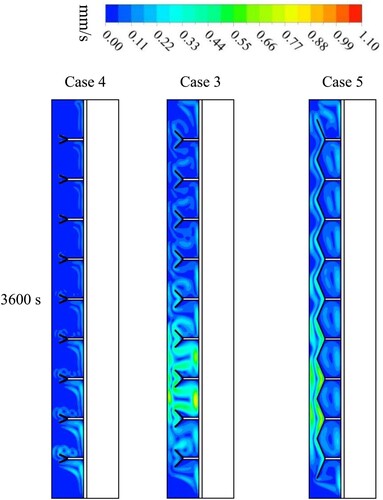
Figure 23. Melting time and heat storage rate of the PCM for various angles of the fin’s tributaries at different time
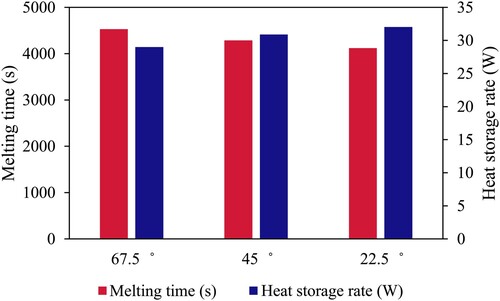
Table 4. PCM's melting time and heat storage rate for various values of Re.
Figure 33. Mean temperature of PCM with three different HTFs’ inlet temperatures (45, 50, and 55°C).
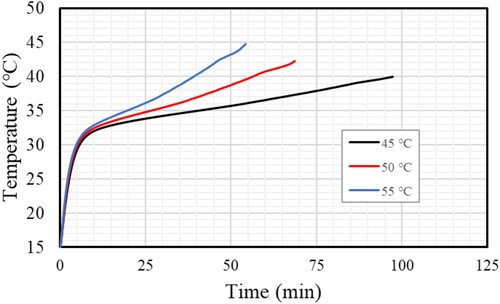
Table 5. PCM's melting time and the heat storage rate during the charging procedure for various values of inlet temperatures.