Figures & data
Figure 2. (a) Schematic overview of the experimental system. 1-water tank, 2,8-ball valve, 3,7-flow meter, 4,6-pressure sensor, 5-test pump, 9-thermal sensor, 10-data acquisition card, 11-computer, 12-air source, 13-switch, 14-pressure regulator, 15-solenoid on-off valve, 16-solenoid directional valve, 17,18-silencer, 19,20-quick exhaust valve, 21-cylinder, 22-laser displacement sensor. (b) Photography of the test pump containing a close-up view of the check valve at the bottom left.
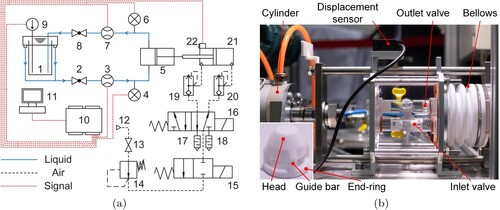
Table 1. Geometrical parameters of the test pump.
Table 2. Details of different test cases.
Table 3. Key parameters of the measuring instruments used in the experiment.
Figure 5. Structured mesh used for the simulation. Different domains are illustrated with different colours. Enlarged views show local refinements in the near-wall region and the region around the end-ring of the inlet valve.
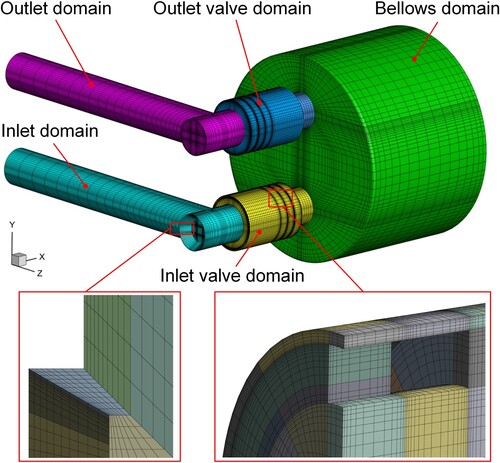
Table 4. Estimations of discretization error.
Table 5. Information of meshes used for grid independence analysis.
Figure 7. Schematic of the forces acting on the inlet check valve at the opening process and details of layering technique for mesh reconstruction.
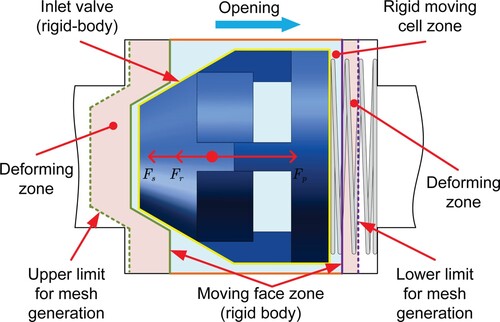
Table 6. Summary of the settings of the fluid solver.
Figure 8. Comparison of time-averaged flow rate computed by numerical model and that obtained from experimental measurement at different inlet pressure
. The bottom figure shows the error ϵ between the numerical results and the fitted values of the experimental results.
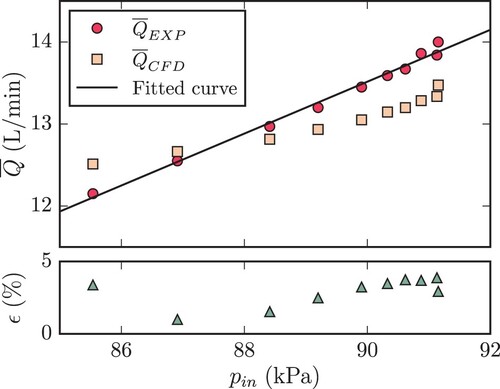
Figure 9. High-speed captures of typical vapour structures in PDBPs (Case 1). (a) Sheet-like cavities at the corner (intersection of the inlet pipe and the inlet channel). (b) Ribbon-like cavities at the core of the inlet channel. (c) Cavitation at the bottom of the inlet valve.
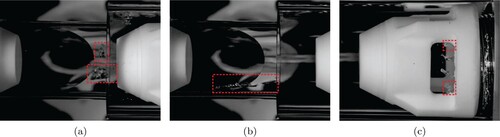
Figure 10. Initiation and development process of vapour structures (iso-surfaces of coloured by blue,
coloured by red) at the bottom of the inlet valve when it is fully opened (Case 1).
is the instant when cavitation incepts at the bottom of the inlet valve. (a)
. (b)
. (c)
. (d)
. (e)
and (f)
.
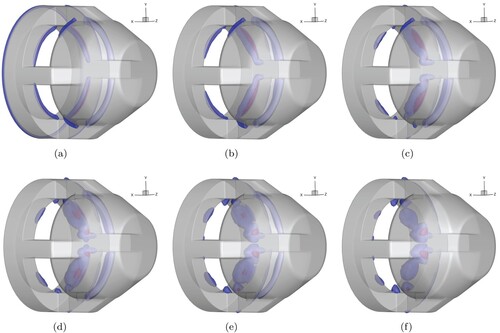
Figure 11. Typical evolution process of vapour structures at the bottom of the inlet valve captured by high-speed camera (Case 1). The vapour structures near the guide bar at the inner part of the end-ring are outlined by red dashed curves. The shed vapour filaments are indicated by orange dashed circles. The time interval between the two frames is .
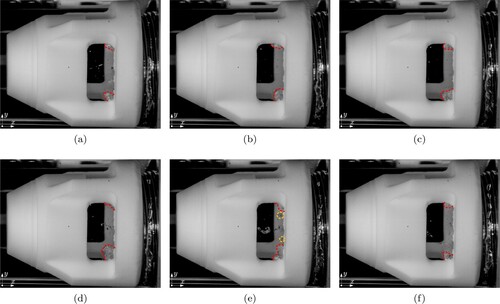
Figure 12. Time series of volume-averaged shear rate in different parts of PDBPs from the beginning of the suction stroke (Case 1).
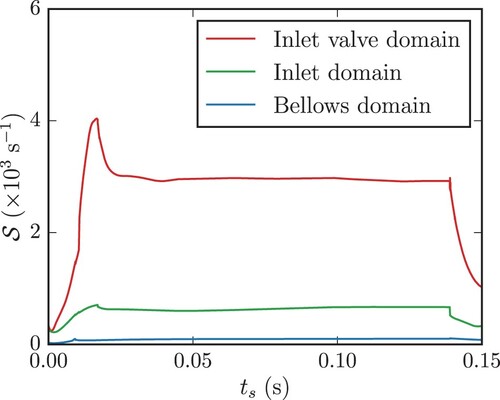
Figure 13. Histograms of time-averaged shear rate in the inlet valve case during the suction stroke (Case 1).
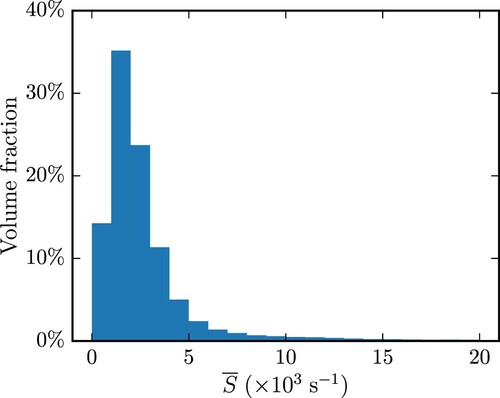
Figure 14. Contour of time-averaged shear rate at different slices of the inlet valve during the suction stroke (Case 1).
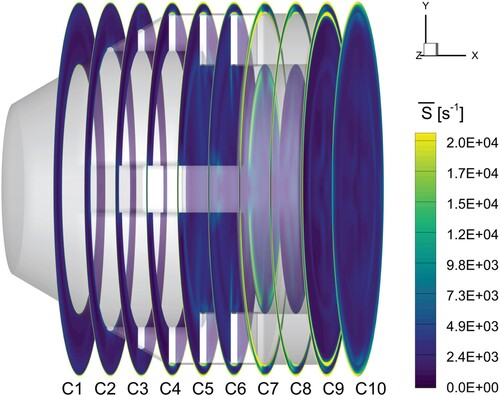
Figure 15. Evolution process of vortical structures (iso-surfaces of coloured by green) at the bottom of the inlet valve when it is fully opened (Case 1).
is the instant when cavitation incepts at the leading edge of the end-ring. (a)
. (b)
. (c)
. (d)
. (e)
and (f)
.
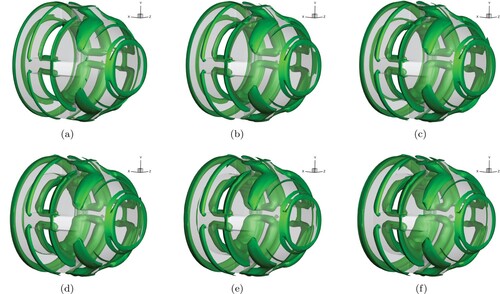
Figure 16. Evolution of the distribution of shear rate S at a cylindrical slice of the inlet valve case, which cuts through the cavities and the vortices at (Case 1).
is the instant when cavitation incepts at the leading edge of the end-ring. A cylindrical coordinate system is established to facilitate the analysis. (a)
. (b)
. (c)
. (d)
. (e)
and (f)
.
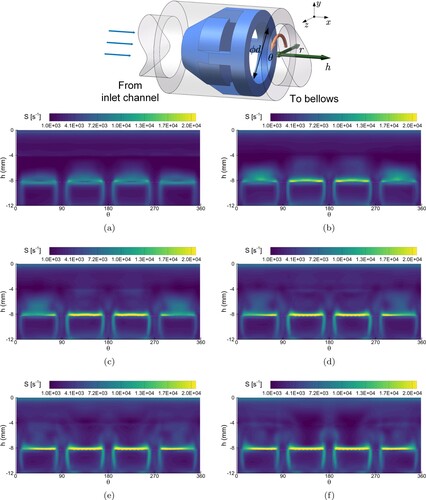