Figures & data
Figure 7. Complete arrangement of ESP system. (a) Complete arrangement of ESP installation within laboratory. (b) inter-stage assembly of ESP. (c) Air admission device.
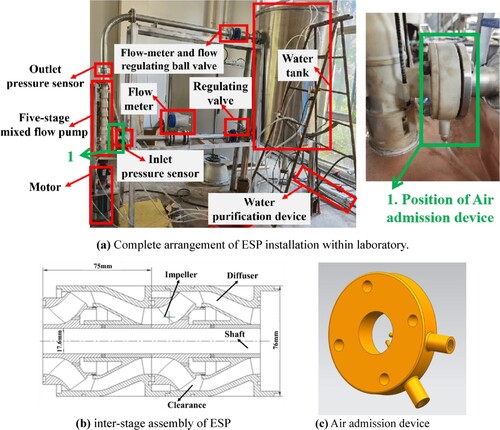
Table 1. Designed parameters of the prototype pump model.
Figure 12. Head characteristic curve of ESP at different flow rates under two-phase flow conditions.
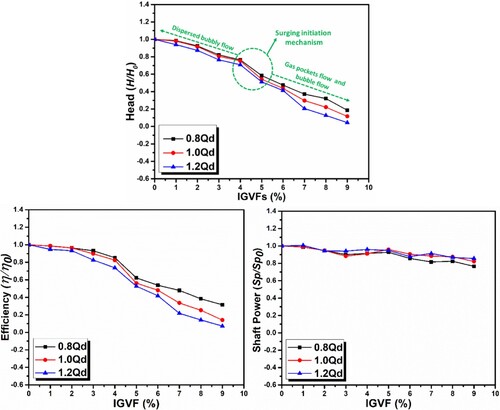
Figure 17. Comparison of test and simulation performance curves under two-phase flow. (a) Head; (b) Efficiency; (c) Shaft power.

Figure 18. Simulated outcomes for ESP-performance on each stage impeller. (a) pure water condition; (b) two-phase flow conditions when Qd = 7.5 m3/h (φ = 0.152).

Figure 19. Gas distribution trend in middle section of 1st stage impeller of ESP at distinct IGVF and flowrate.
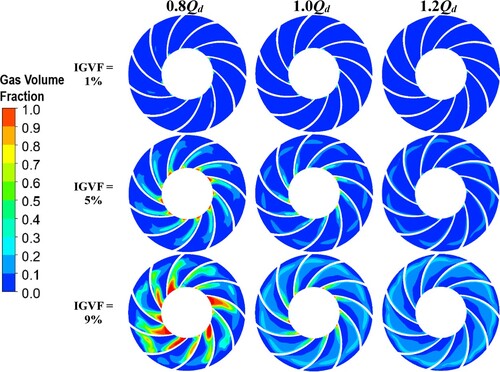
Figure 20. Volume distribution of the gas contents on the first stage impeller’s cross-section at various rotational positions.
Note: Working conditions (IGVF = 9%, and 1.0Qd). (a) 0°; (b) 30°; (c) 60°; (d) 90°; (e) 120°; (f) 150°.
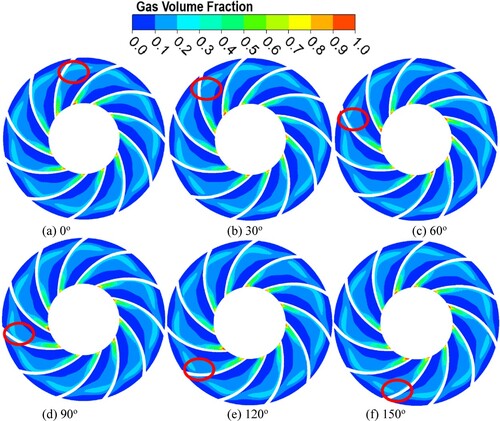
Data availability
The data supporting this study’s findings are available from the corresponding author upon reasonable request.