Figures & data
Table 1. Char yield values for samples with varying nanoclay concentrations.
Table 2. The gelation temperatures of different samples with varying nanoclay contents.
Table 3. Activation energies of the three different samples containing different amounts of nanoclay.
Figure 7. Printer modification with labeled axis. Arrows indicate positive direction of rotation or movement.
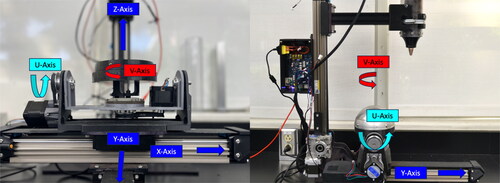
Supplemental Material
Download QuickTime Video (87.8 MB)Data availability statement
The authors confirm that the data associated with the results of this study are available within the article and its supplementary materials.