Figures & data
Figure 1. SEM micrographs taken at various locations in the friction stir-processed region. The locations are marked along with the location of cross-section of the mini-tensile sample gage on the macro view of the processed region.
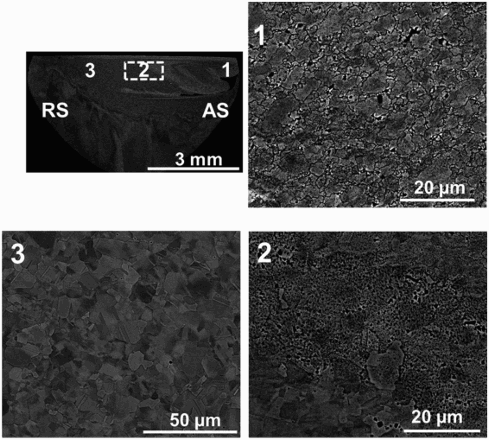
Figure 2. (a) The variation of hardness across the processed region on the transverse cross section and (b) the plastic stress–strain curves in both CG and FG conditions.
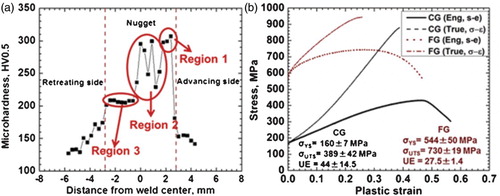