Figures & data
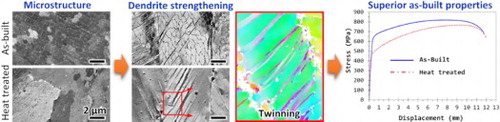
Table 1. Major elemental composition of the Hastelloy X powder used for this study measured by Praxair Surface Technologies Inc. using ICP and X-ray fluorescence.
Table 2. Details for each heat treatment designation utilized in this study.
Figure 1. Microstructures of the non-heat-treated (NHT) and heat-treated Hastelloy X examined on the transverse (x-y plane) cross-section: (a)–(e) BSE micrographs of grain interior and grain boundaries, (f)–(j) inverse pole figure (IPF) maps showing overall grain morphology. The colors in (f)–(j), as indexed by the legend, indicate the crystallographic orientation along the normal direction (also the build direction z). The numbers in (f)–(j) indicate the average grain size.
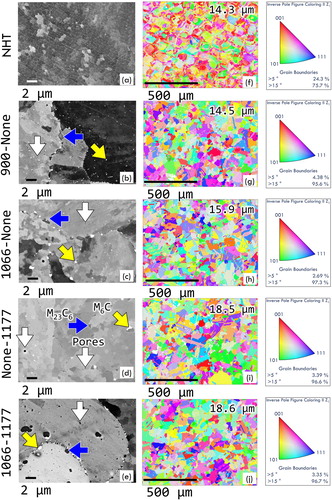
Figure 2. Tensile test results for L-PBF Hastelloy X superalloy in various heat treatments: (a) engineering stress - displacement curves and (b) the corresponding column charts for YS, UTS, HR and EL. Selected data from (b) is compared with L-PBF as well as wrought data from literature in (c).
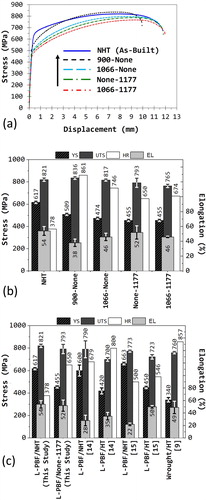
Figure 3. Micrographs obtained by FIB imaging on longitudinal (x-z plane) polished sections of failed tensile specimens (about 500 μm below line of fracture on surface), showing morphologies of deformation bands as affected by the microstructure resulting from various heat treatments.
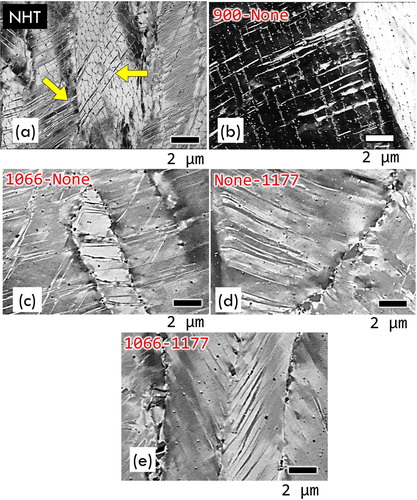
Figure 4. (a) A typical IPF map of ‘deformation bands’ in the failed tensile specimen heat-treated under the 1066-None condition obtained by the EBSD scan on the longitudinal (x-z) plane. The Thompson’s tetrahedra shown in (b) and (c) illustrates the orientations of individual domains. The colors in the IPF maps, as indexed by the legend, indicate the crystallographic orientation along the normal direction (also the build direction z). (d) and (e) show the misorientation angle profiles along the solid lines in the ‘b’ and ‘c’ boxes in (a), respectively.
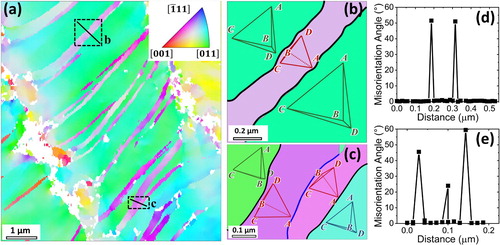