Figures & data
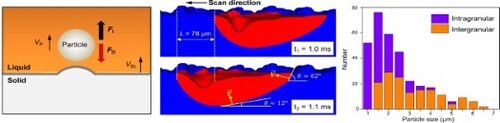
Figure 1. Theoretical analysis of particle engulfment in metal composites by SLM. (a) Schematic of particle motion. FI and FD stand for repulsive and drag force, respectively. VSL and VP are velocities of solidification front and particle motion, respectively. Gravity and buoyancy are not shown due to their small values. (b) The plot of net force as a function of VSL. Vc is critical pushing velocity. (c) The dependence of Vc on particle radius (R). The size ranges of TiB2 particles used in this work are shown. (d) Modeling results on VSL calculation. VSL = V sinθ. V is scanning speed (L/Δt). SD means scan direction. (e) The simulated 3D-temperature gradient profile. X, Y and Z are scan direction, transverse direction and sample building direction, respectively. Inset shows a schematic of melt flow during SLM.
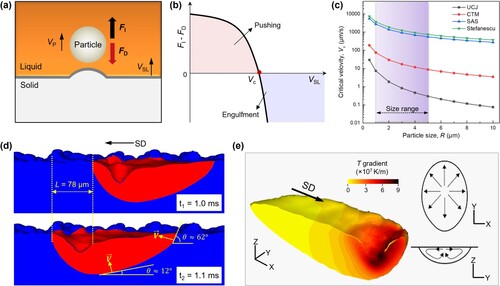
Figure 2. Microstructures of as-built TiB2-Al composites. Both SLM and PM TiB2-Al composites possess relative density of larger than 99.5%. (a) EBSD image showing the distribution of TiB2 particles (colored in green, 15 vol.%) in SLM composite. High-angle grain boundaries (HAGBs) with misorientation larger than 10° are superimposed. (b) EBSD image of comparing PM TiB2 (15 vol.%)-Al composite. The non-identified regions are shown in black. (c) EBSD image of PM composite after cold rolling. (d) Histogram showing the size distribution of TiB2 particles and their locations either in grain interiors or at GBs, as measured by EBSD. (e) A typical APT slice (thickness 10 nm) showing the atomic distributions across the TiB2-Al interface. The right panel shows the corresponding 1D compositional profiles.
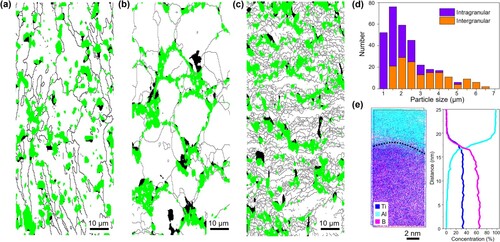
Figure 3. Crystallographic relationship between TiB2 and Al in SLM TiB2-Al composite. (a) and (b) are inverse pole figures showing the orientation of Al matrix parallel to the [0001] direction of the intragranularly and intergranularly distributed TiB2 particles, respectively.
![Figure 3. Crystallographic relationship between TiB2 and Al in SLM TiB2-Al composite. (a) and (b) are inverse pole figures showing the orientation of Al matrix parallel to the [0001] direction of the intragranularly and intergranularly distributed TiB2 particles, respectively.](/cms/asset/1632483b-2639-47fd-bd5b-a933f0533b03/tmrl_a_2153630_f0003_oc.jpg)
Figure 4. Mechanical properties and deformation mechanisms. (a) The representative tensile stress–strain curves of SLM composite and PM TiB2-Al composite. (b) The plots of strain hardening rate as a function of true strain. Note that the strain hardening rate data after necking (which corresponds to true strain values of 1.4% and 3.9% for PM and SLM TiB2-Al composite, respectively) are not shown due to the non-uniform deformation. Inset shows the representative TEM image of the deformed SLM composite. Numerous dislocations, as indicated by black arrows, are present at the interface. (c) and (d) are fracture surfaces of PM and SLM composite, respectively. TiB2 are found at the fracture surface of PM sample, as indicated by the white dashed circles. (e) Ex-situ EBSD measurements for SLM composite with different strains (tensile strain: 0%, 1.5% and 3.0%). A, B and C are typical TiB2 particles that are distributed inside Al grains. They are selected for further EBSD examinations. KAM maps, measured in degrees, are used to illustrate the heterogeneous deformation inside Al grains. Local misorientations (or GNDs) show obvious increments with strain nearby the intragranular TiB2 particles, as indicated by the yellow dashed circles.
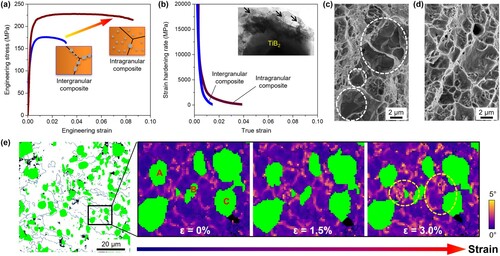