Figures & data
Table 1. Digital twin platform datasources.
Figure 4. Overall architecture of the geometry pipeline. The ‘Reduce’ steps highlighted are expanded upon in .
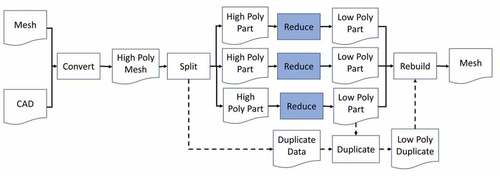
Figure 5. Geometry pipeline ‘reduce’ step. Copies of this process are run in parallel for every unique part in the model. The three components highlighted in blue are the three machine learning models.
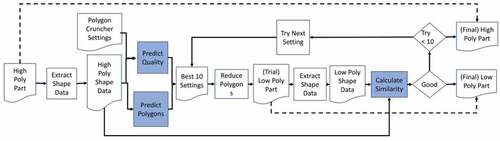
Table 2. Shape and similarity metrics used in the geometry pipeline to ensure mesh visual quality. Note that none of these metrics encode the scale of the object, to ensure the method is scale invariant.
Figure 6. Mesh quality training data collection application (original on the left, processed on the right).
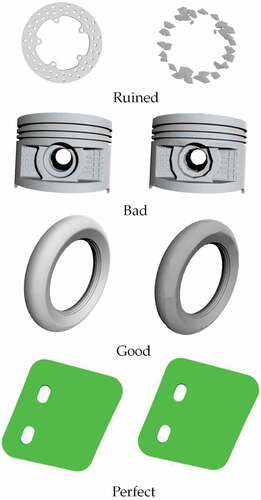