Figures & data
Figure 1. Schematic of temperature measurement for an Al2O3 uniaxially pressed sample, using PTCR in a (a) conventional furnace and (b) microwave furnace.
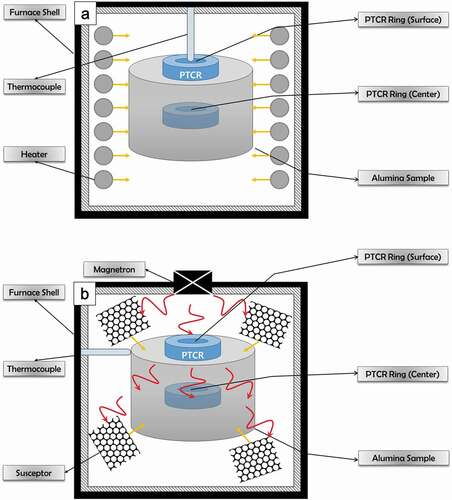
Table 1. Temperature measurement results
Figure 2. Schematic of an Al2O3 slip cast sample and the points of interest (s: surface; c: center).
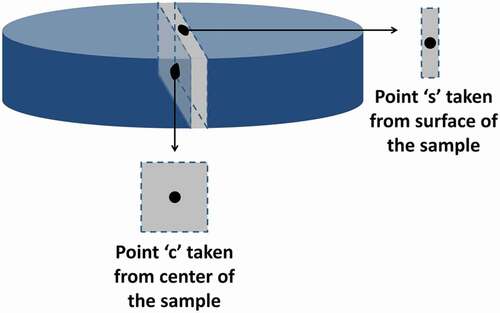
Figure 5. Measured temperature versus set temperature of the (a) conventionally sintered samples and (b) microwave-hybrid-sintered samples.
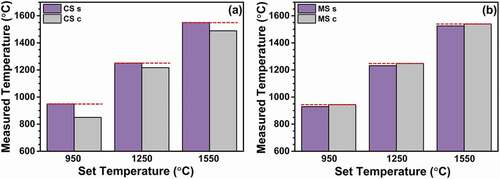
Figure 10. Grain-size distributions of (a) conventionally sintered samples and (b) microwave-hybrid-sintered samples, (c) average grain sizes at the surface and center points after different holding times, and (d) schematic showing the directions of the temperature gradient and grain growth during conventional and microwave sintering.
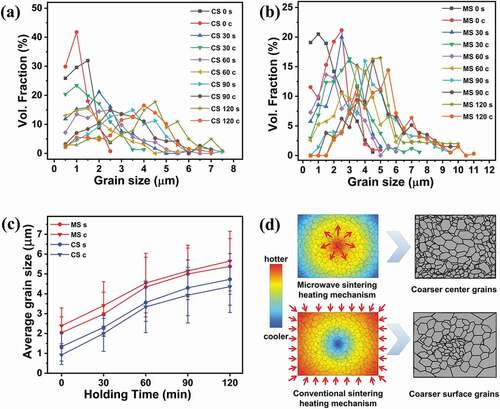
Table 2. Estimated temperatures from the measured temperatures using PTCRs
Figure 12. FE–SEM images showing the microstructures of the conventionally sintered samples at different set temperatures with no holding time (s: surface; c: center).
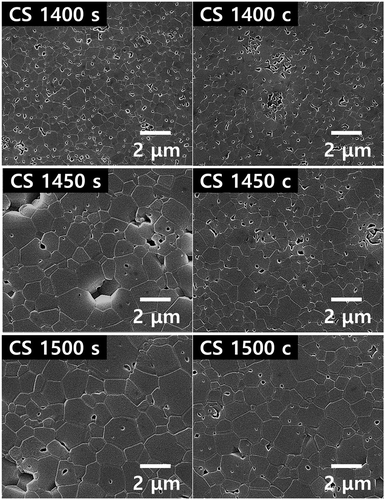
Figure 13. FE–SEM images showing the microstructures of microwave-hybrid-sintered samples at different set temperatures with no holding time (s: surface; c: center).
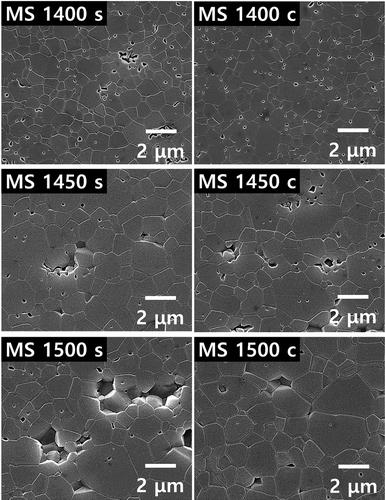
Figure 14. Average grain sizes at the surface and center points after sintering at different estimated temperatures.
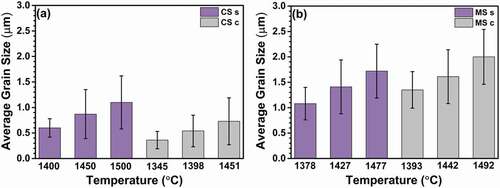