Figures & data
Table 1. Mechanical properties of CFRP
Table 2. Levels of variables
Table 3. Obtained data from experiments for modeling of machining process
Table 4. Comparison of RSM predictions with experimental data
Figure 6. Machining force versus feed rate for various spindle speeds; (a) DC = 2 mm, (b) DC = 6 mm, and (c) DC = 8 mm.
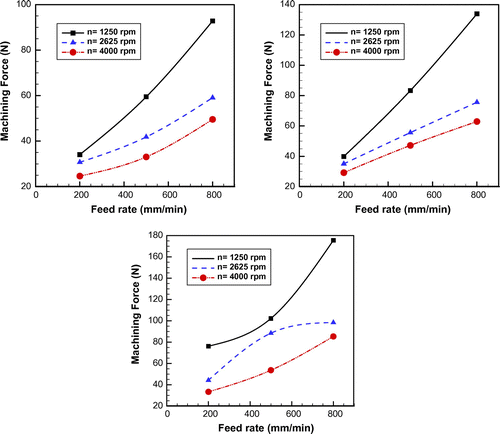
Figure 7. Surface roughness versus feed rate for various spindle speeds; (a) DC = 2 mm, (b) DC = 6 mm, and (c) DC = 8 mm.
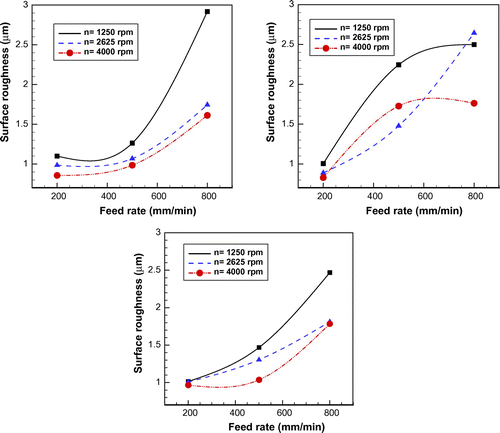