Figures & data
Figure 4. A schematic diagram of a two area interconnected power system with TCPS in series with tie-line.

Figure 13. Membership function for the two inputs and two outputs with gains of −1 to 1 and −10 to 10, respectively.

Table 1. Fuzzy rules for the inputs and outputs
Table 2. GWO optimized Fuzzy PID controller parameters of power system-1 without physical constraints
Figure 15. (a) Frequency deviation in Area 1 subjected to a step load change of 0.01 p.u. in Area 1, (b) Frequency deviation in Area 2 subjected to a step load change of 0.01 p.u. in Area 1 and (c) Tie-line power flow deviation subjected to a step load change of 0.01 p.u. in Area 1.
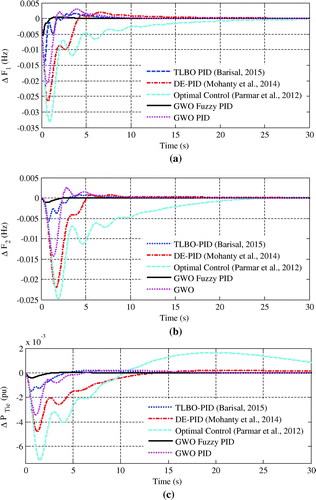
Figure 16. (a) Frequency deviation in Area 1 subjected to a step load change of 0.01 p.u. in Area 1 and their comparison for proposed GWO optimized Fuzzy PID control scheme with TLBO optimized Output feedback SMC scheme, (b) Frequency deviation in Area 2 subjected to a step load change of 0.01 p.u. in Area 1 and their comparison for proposed GWO optimized Fuzzy PID control scheme with TLBO optimized Output feedback SMC scheme and (c) Tie-line power flow deviation subjected to a step load change of 0.01 p.u. in Area 1 and their comparison for proposed GWO optimized Fuzzy PID control scheme with TLBO optimized Output feedback SMC scheme.
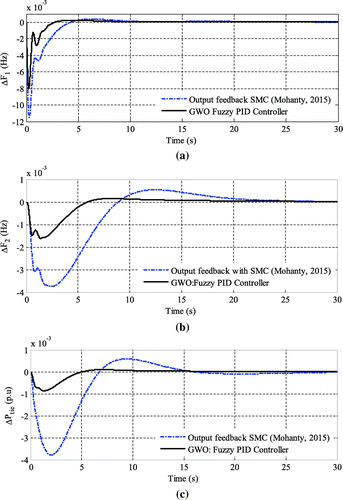
Table 3. GWO optimized Fuzzy PID controllers parameters of power system-2 with HVDC link, GRC and reheat turbine
Table 4. Performance evaluation of proposed GWO optimized Fuzzy PID controller by settling time, minimum undershoot and maximum overshoot
Figure 17. (a) Frequency deviation of Area 1 without and with SMES subjected to load change of 0.01 p.u. in Area 1, (b) Frequency deviation of Area 2 without and with SMES subjected to load change of 0.01 p.u. in Area 1 and (c) Tie-line power flow deviation without and with SMES subjected to load change of 0.01 p.u. in Area 1.
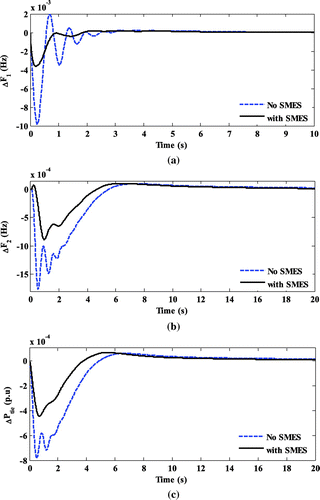
Table 5. System modes, minimum damping ratio, for multi-source multi area power system with HVDC link, GDB, GRC and Reheat turbine without and with SMES
Table 6. Performance evaluation of proposed GWO optimized Fuzzy PID controller by settling time, minimum undershoot and maximum overshoot of multi-source multi area nonlinear power system without and with SMES
Table 7. Optimal gains of controller for different FACTS devices
Figure 18. (a) Frequency deviation of Area 1 with SMES and FACTS subjected to a step load change of 0.01 p.u. in Area 1, (b) Frequency deviation of Area 2 with SMES and FACTS subjected to a step load change of 0.01 p.u. in Area 1 and (c) Tie-line power flow deviation with SMES and FACTS subjected to a step load change of 0.01 p.u. in Area 1.
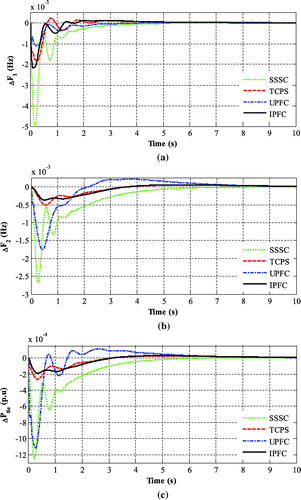
Table 8. Performance criteria for multi-source multi area nonlinear power system with SMES and FACTS
Table 9. System modes, minimum damping ratio, for multi-source multi area nonlinear power system with SMES and FACTS
Figure 20. (a) Frequency deviation in Area 1 subjected to random load in Area 1 with GWO optimized Fuzzy PID controller, (b) Frequency deviation in Area 2 subjected to random load in Area 1 with GWO optimized Fuzzy PID controller and (c) Tie line power deviation obtained subjected to random load in Area 1 with GWO optimized Fuzzy PID controller.
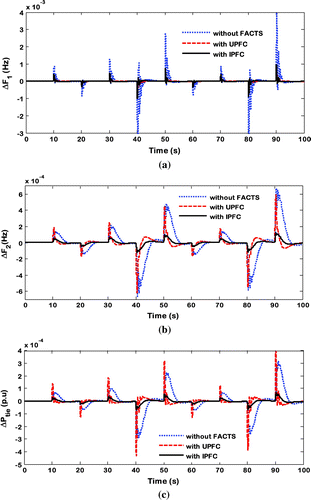
Figure 22. (a) Frequency deviation in Area 1 subjected to sinusoidal load pattern in Area 1 with GWO optimized Fuzzy PID controller with and without FACTS, (b) Frequency deviation in Area 2 subjected to sinusoidal load pattern in Area 1 with GWO optimized Fuzzy PID controller with and without FACTS and (c) Tie line power deviation subjected to sinusoidal load pattern in Area 1 with GWO optimized Fuzzy PID controller with and without FACTS.
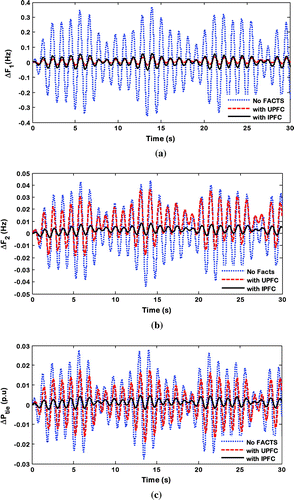
Table 10. Optimal gains of controller for different FACTS devices for three area thermal power system
Figure 26. (a) Frequency deviation in Area 1 subjected to SLP of 1% in Area 1 with GWO optimized Fuzzy PID controller with and without FACTS, (b) Frequency deviation in Area 2 subjected to SLP of 1% in Area 1 with GWO optimized Fuzzy PID controller with and without FACTS and (c) Frequency deviation in Area 3 subjected to SLP of 1% in Area 1 with GWO optimized Fuzzy PID controller with and without FACTS.
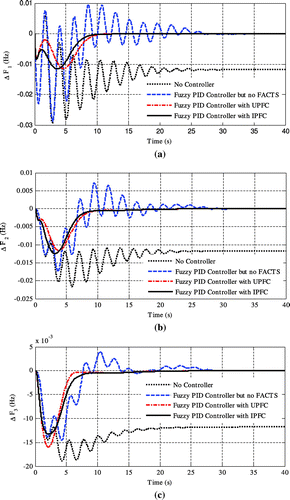