Figures & data
Table 1. Mechanical properties of materials
Table 2. Failure sequences of specimen T-1
Figure 26. Distribution of pressure between the flange-plate and beam bottom flange caused by bolt pretension force.
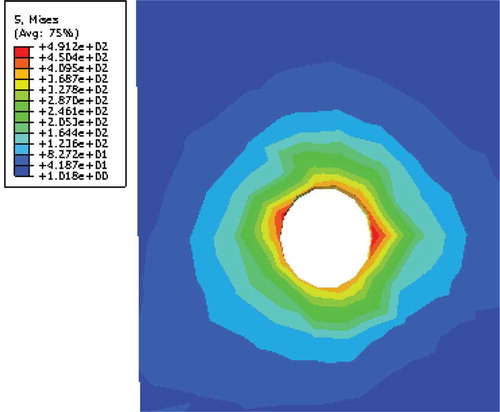
Figure 27. Distribution of force between the flange-plate and beam bottom flange at the ultimate load (T-2).
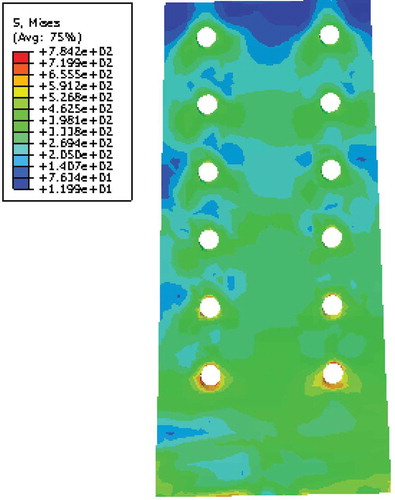
Figure 28. Distribution of force between the flange-plate and beam bottom flange at the ultimate load (T-3).
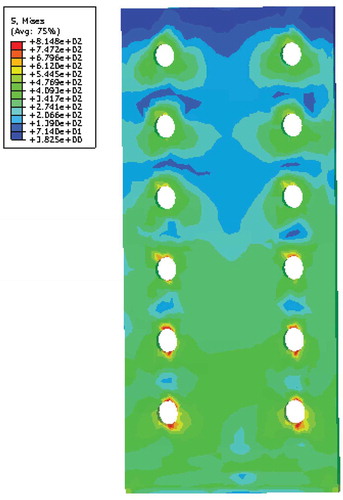
Table 3. Failure sequences of specimen T-2
Table 4. Failure sequences of specimen T-3
Table 5. The tensile capacity comparison between the test and prediction results