Figures & data
Table 1. Details of the fabric used
Table 2. Details of the matrix used
Figure 2. Fibre orientation and stacking arrangement of the fabricated laminate (1 and 8 represent the top and bottom layers).
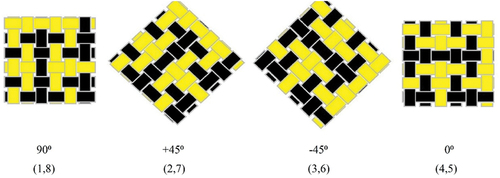
Table 3. Specimen coding and test details
Table 4. Moisture diffusion parameters
Table 5. Tensile properties of the specimens
Figure 11. SEM micrographs of fractured (a) Pristine (b) Ambient (c) Sub-zero and (d) Humid aged tensile test specimens.
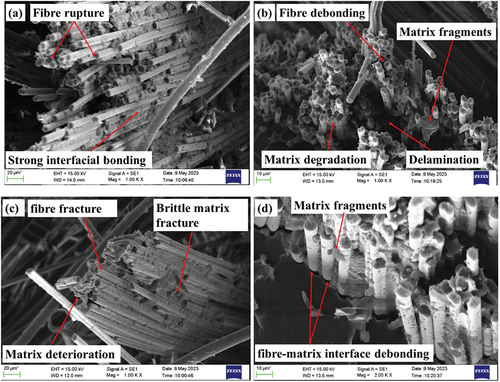
Figure 15. Light microscope pictures of fractured (a) Pristine (b) Ambient (c) sub-zero and (d) humid aged SBS test specimens.
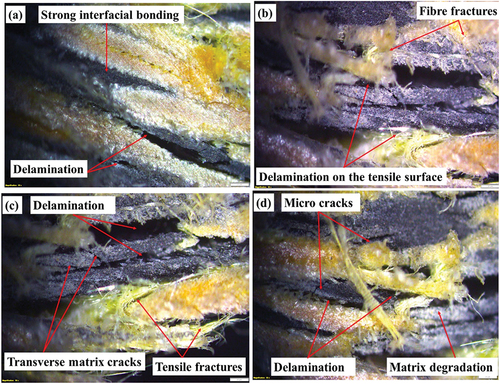
Table 6. Damping properties of pristine and aged specimens
Figure 16. Damping characteristics of pristine specimens (a) Acceleration amplitude vs frequency (b) Acceleration amplitude vs time.
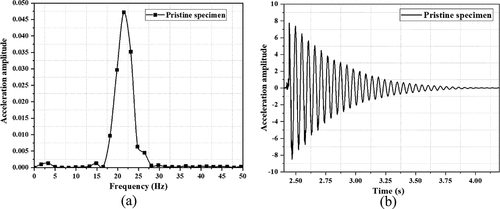
Figure 17. Damping characteristics of ambient aged specimens (a) Acceleration amplitude vs frequency (b) Acceleration amplitude vs time.
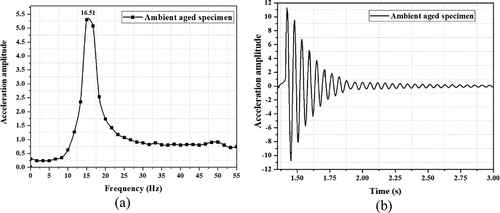