Figures & data
Figure 2. Microstructure of workpiece materials (a) Nitrile Rubber (b) Polyurethane Rubber (c) Neoprene Rubber.
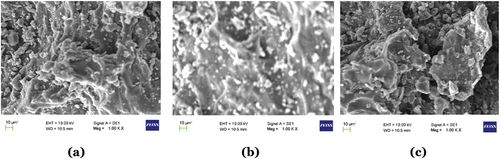
Table 1. Specifications of the cutting tool
Table 2. Statistical data for selection of learning algorithm
Figure 10. Microscopic image of PU elastomer material under (125 m/min) cutting speed, (0.18mm/rev) feed, (0.50 mm) depth of cut and LN2 conditions.
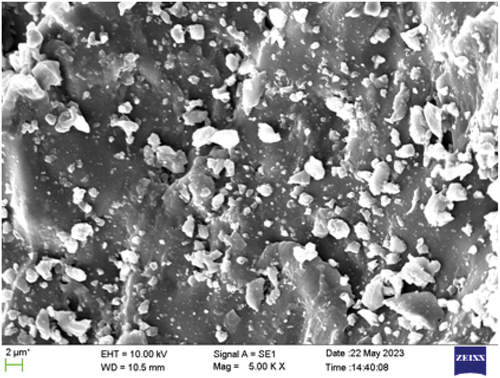
Figure 11. Cutting force (N) signals for PU elastomer material under (125m/min)cutting speed, (0.18mm/rev)feed, (0.50mm)depth of cut and LN2 conditions.
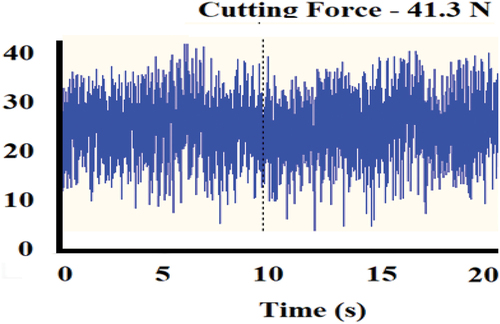
Table 3. ANOVA for cutting force (N)
Figure 16. Microstructure of turned surfaces of (a) Nitrile Rubber (NBR) (b) Polyurethane Rubber (PU) (c) Neoprene Rubber (CR) under (125m/min)cutting speed, (0.18mm/rev)feed, (0.50mm)depth of cut and LN2 cooling conditions.
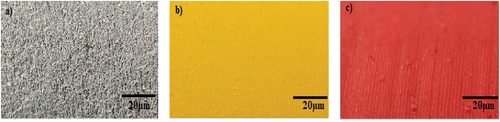
Table 4. ANOVA for surface roughness
Table 5. Training set for BPANN
Table 6. Test set for BPANN prediction
Table 7. Observations of output response