Figures & data
Table 1. The comparison of the available literature related to EV drivetrain
Table 2. Battery parameter specifications (Raghunath, Citation2021)
Table 3. Motor specifications [15]
Table 4. Modes of operation with specified speed, torque and power ratings
Table 5. Design Calculations of BD-qZSI
Figure 3. (a) Shoot through state and (b) non-shoot through state (Guo et al., Citation2013).
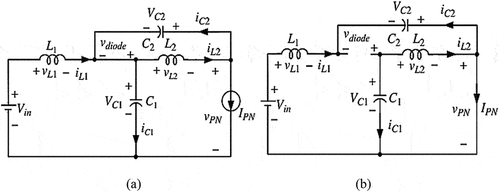
Figure 17. (a) The battery voltage Vbat and motor voltage Vm for reference of STHCC shoot through duty ratio Ds.
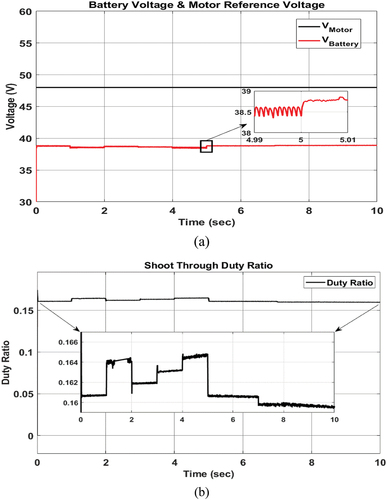
Table 6. Speed and torque ripple at different motor loading