Figures & data
Table 1. Comparison of various channel fabrication techniques.
Table 2. Comparison of circular microchannel fabrication methods.
Figure 2. Copper wire mold image (a) SEM image (Zoom 200X) (b) SEM image (Zoom 1000X) (c) AFM image (maximum surface roughness 134.4 nm).
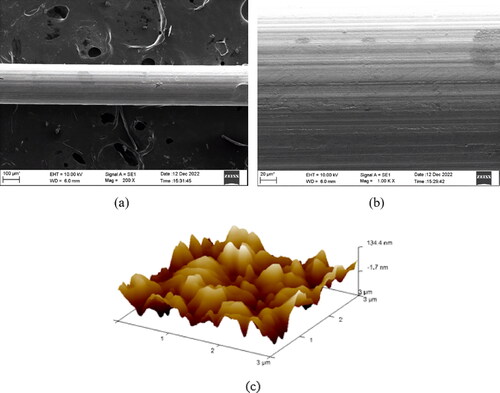
Figure 4. Plastic container for optimal use of PDMS: (a) Top view, and (b) Box in the open state (Tiwari et al., Filed on 18th December Citation2023).
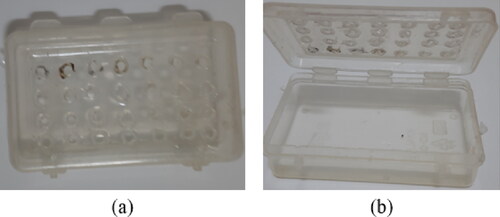
Figure 5. Plastic container with a layer of aluminum foil (Tiwari et al., Filed on 18th December Citation2023).
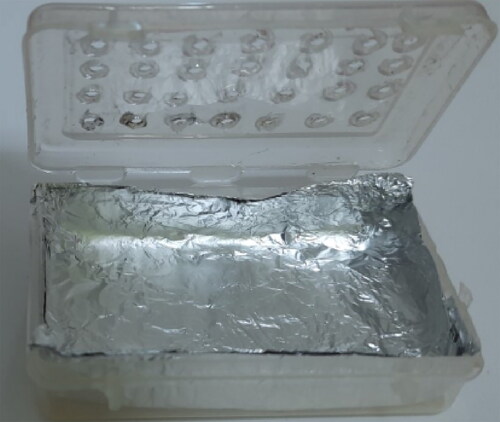
Figure 9. Velocity profile in the channel at various distance starting at 0 from inlet (a) Straight channel, and (b) Channel model with bending.
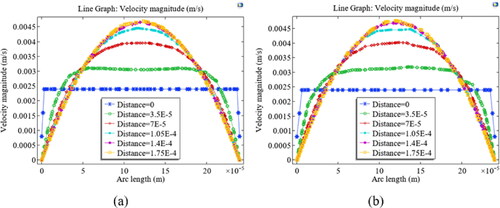
Figure 12. Poincaré map at the outlet of the straight channel (a) Time 11.70s (b) Time 11.75s, and (c) Time 20.00s.
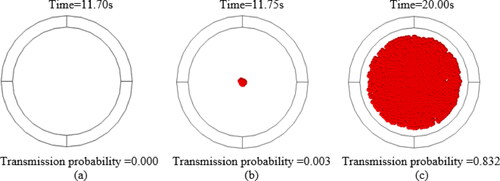
Figure 13. Poincaré map at the outlet of the channel with bending (a) Time 11.65s (b) Time 11.70s, and (c) Time 20.00s.
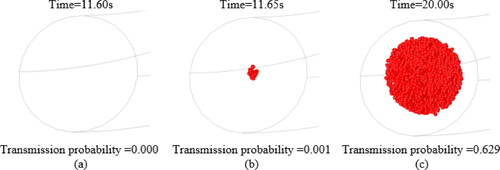
Figure 14. Residence time testing of channel (a) Empty channel (b) Half-filled channel, and (c) Completely filled.
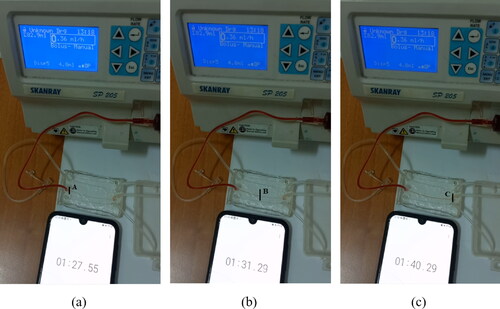
Table 3. Microfluidic channel and their applications.