Figures & data
Figure 1. (A) GPS module; (B) Hall effect sensor; (C) Rotary potentiometer; (D) Three-point hitch dynamometer.
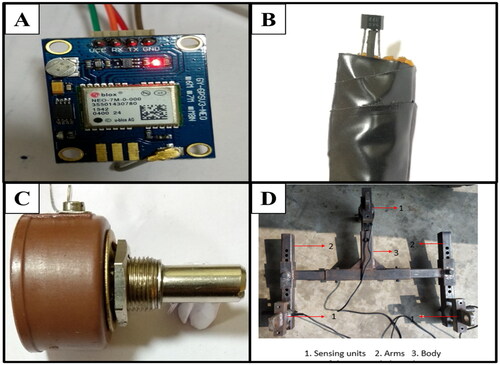
Table 1. Transducers and their specifications.
Figure 4. Calibration setup for (A) load cell in compression; (B) load cell in tension; (C) depth measurement.
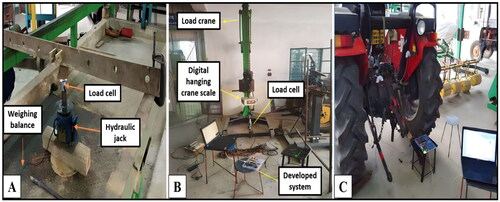
Figure 5. Calibration curve (A) load cell in compression; (B) load cell 1 in tension; (C) load cell 2 in tension; (D) for depth measurement.
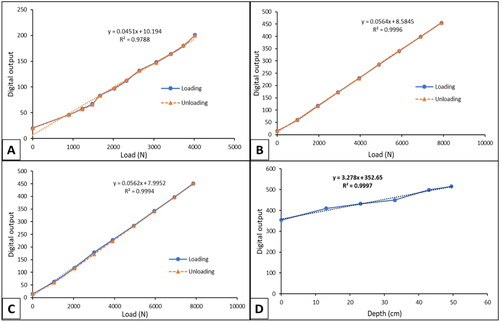
Data availability statement
The original contributions presented in the study are included in the article; further inquiries can be directed to the corresponding author.