Figures & data
Figure 1. Workpiece specimen (a) Image of coconut coir fiber (b) Image of CCFRP composite laminates (c) Microstructure of CCFRP composite laminates.

Table 1. Mechanical properties coir fiber (Hasan et al., Citation2021).
Table 2. Properties of epoxy resin and hardener (Hasan et al., Citation2021).
Table 3. Drilling test parameters and levels.
Figure 3. Main Effect Plot for Thrust force (N) against (a) Spindle Speed (RPM), (b) Feed Rate (mm/min), (c) Point Angle (Degrees), (d) Fiber Length (mm), (e) Fiber Volume (%), (f) Fiber Diameter (microns).
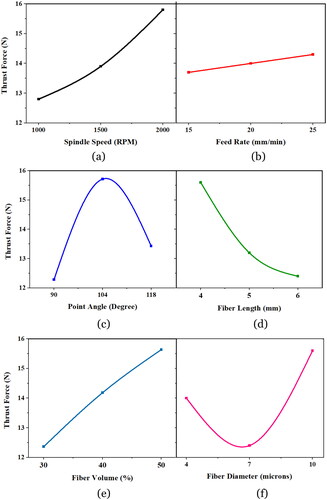
Figure 4. Main Effect Plot for Torque (N-m) against (a) Spindle Speed (RPM), (b) Feed Rate (mm/min), (c) Point Angle (Degrees), (d) Fiber Length (mm), (e) Fiber Volume (%), (f) Fiber Diameter (microns).
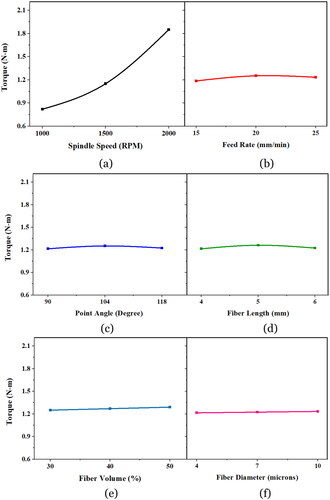
Table 4. Experimental values of Thrust Force (N) and Torque (N-m).
Figure 5. Images of drilled hole under different spindle speeds (a) 1000 rpm (b) 1500 rpm (c) 2000 rpm.
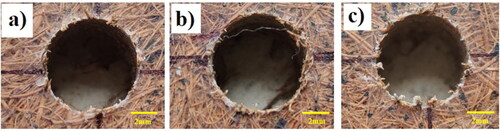
Figure 6. SEM images of drilled hole under different spindle speeds. (a) 1000 rpm (b) 1500rpm (c) 2000rpm.
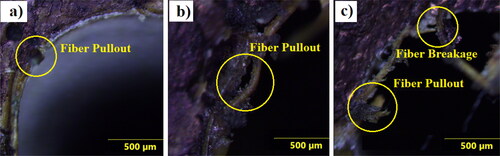
Figure 7. Images of chips formed under different spindle speed (a) 1000 rpm (b) 1500 rpm (c) 2000 rpm.
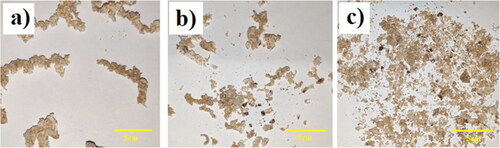
Table 5. Analysis of variance for SN ratios for Thrust force (N).
Table 6. Analysis of variance for SN ratios for Torque (N-m).
Figure 8. Thrust force (a) contour plot and (b) surface plot in spindle speed- fiber volume% plane at constant feed rate, point angle, fiber length and fiber diameter.
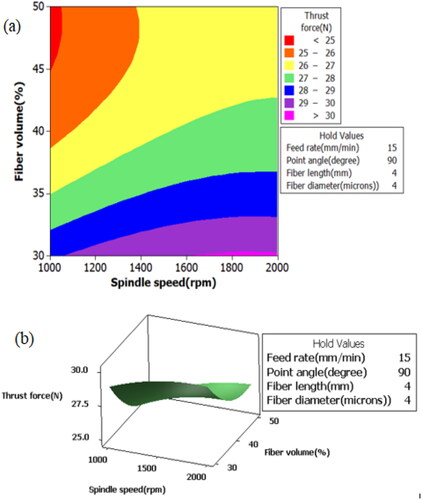
Figure 9. Torque (a) contour plot and (b) surface plot in spindle speed- fiber volume% plane at constant feed rate, point angle, fiber length and fiber diameter.
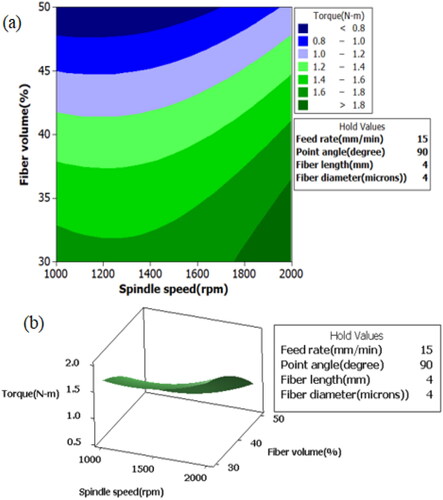
Figure 10. Thrust force signals for (a) Fiber volume of 50% (b) Fiber volume of 40% and (c) Fiber volume of 30% CCFRP composite.
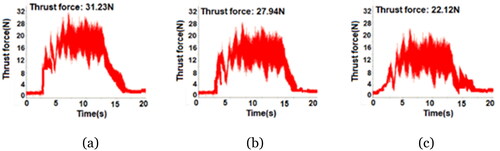
Figure 11. Torque signals for (a) Fiber volume of 50% (b) Fiber volume of 40% and (c) Fiber volume of 30% CCFRP composite.
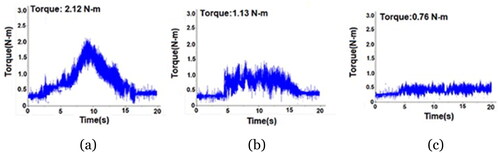
Table 7. Analysis of variance for Thrust force (N).
Table 8. Analysis of variance for Torque (N-m).
Table 9. Validation of MLP-ANN prediction results using experimental data.