Figures & data
Figure 1. P20 Prototype image; (a) 3D view and (b) top view with pressure point (Pi, P1 – P6, Po); T1: Turbine 1, T2: Turbine 2; scale 1:8.
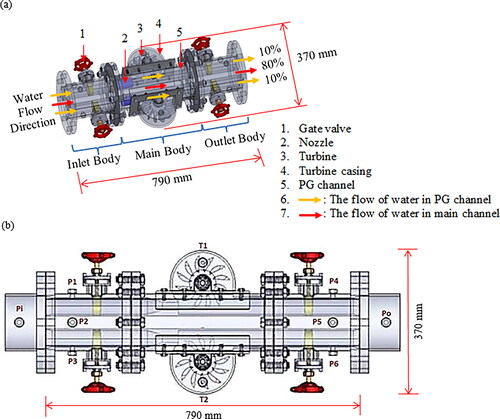
Table 1. Material selection for P20.
Figure 8. Relationship between hydraulic power and flow rate (from EquationEquation (1)(1)
(1) ).
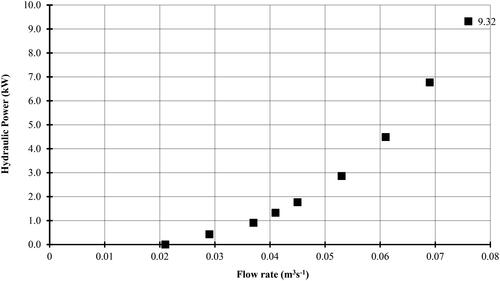
Table 2. Flow and turbine properties.