Figures & data
Table 1. Concrete mix highlights.
Figure 4. (a) Demoulding of the pile with helical groove specimen. (b) Pile with the helical groove test specimen.
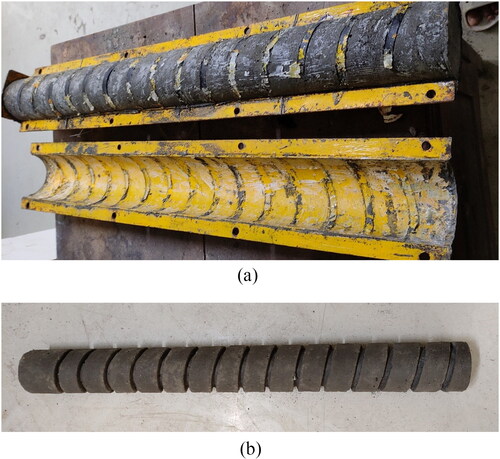
Figure 5. (a) Control pile P0, (b) RCC pile with helical grooves P50, (c) RCC pile with helical grooves P75, and (d) RCC pile with helical grooves P100.
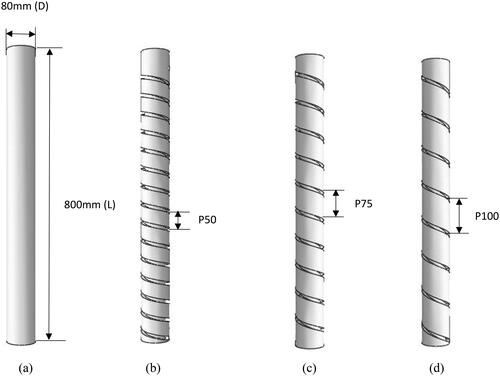
Figure 6. The axial load test setup (a) line diagram of the testing tank and (b) dial gauges, sand, and pile.
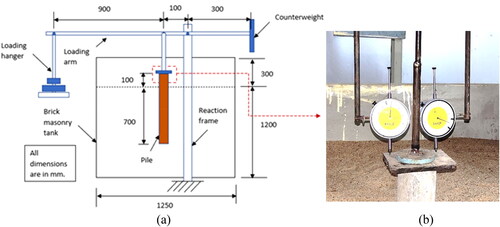
Table 2. Physical properties of cohesionless soil.
Figure 7. The lateral load test setup (a) line diagram of the setup and (b) steel rope, dial gauge, sand, and pile.
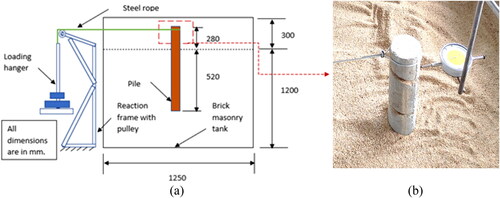
Table 3. Mechanical properties of cohesionless soil and pile.
Figure 14. (a) Control pile subjected to axial load showing displacement of soil particles and (b) end bearing as pressure bulb.
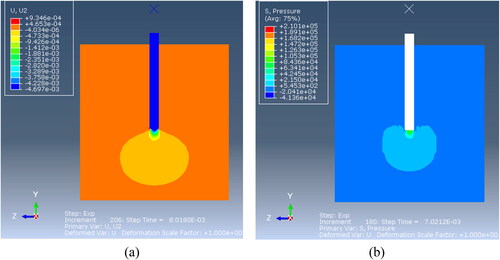
Figure 15. (a) P100 helical groove pile subjected to axial load showing displacement of soil particles and (b) end bearing pressure and pressure at groove interlocks.
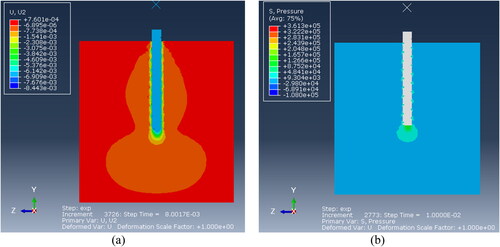
Figure 16. (a) P75 helical groove pile subjected to axial load showing displacement of soil particles and (b) end bearing pressure and pressure at groove interlocks.
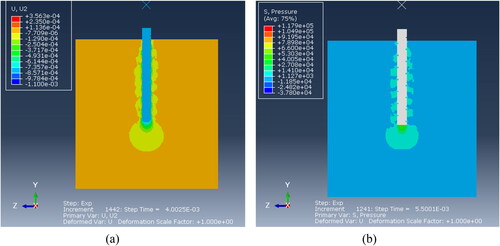
Figure 17. (a) P50 helical groove pile subjected to axial load showing displacement of soil particles and (b) end bearing pressure and pressure at groove interlocks.
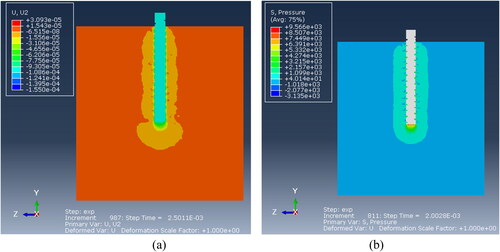
Table 4. The percentage volume of groove for a pitch of the helix.
Table 5. End bearing and shaft resistance.