Figures & data
Table 1. Chemical composition of ER-5356 and Al6061-T6.
Table 2. Welding Parameters of GMAW welding for Al 6061-T6 as per WPS.
Table 3. X-ray radiography films.
Figure 4. (a) The detailed specification of tensile and bending test specimens and (b) tensile and bending test specimens.

Table 4. The tensile test result of Al 6061-T6 GMAW welded samples.
Table 5. The parameters used in the FCG test.
Table 6. FCG Test result of Al 6061 T-6 GMAW welded specimen.
Table 7. Fitting constant obtained from experimental data.
Figure 21. Micrograph of BM. (a) R = 0.1 at Kth region, (b) R = 0.1 at Kc region, (c) R = 0.3 at Kth region, (d) R = 0.3 at Kc region, (e) R = 0.5 at Kth region, (f) R = 0.5 at Kc region.
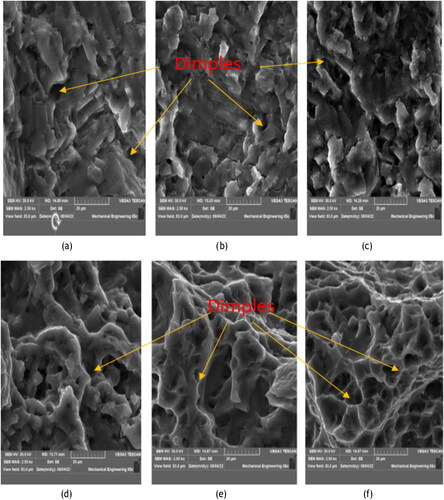
Data availability statement
The author confirmed that the data supporting the findings of this study are within the article. Raw data supporting the findings of this study are available from the corresponding author upon reasonable request.