Figures & data
Table 1. Main technical data related to POM-60000/525-У1.
Table 2. Design sound pressure and power.
Table 3. Design characteristics and dimensions of the POM-60000/525-U1 reactor.
Figure 4. Installation of rubber gaskets on the 3D model of the reactor: (a) 1—between the packages of the magnetic system and (b) 2—between the beam and the yoke on the assembled reactor.
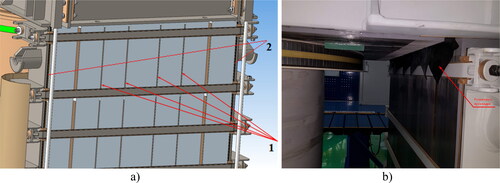
Figure 6. Points at which the sound levels of the reactor are measured: A—high-voltage lead and X1, X2—grounded side.
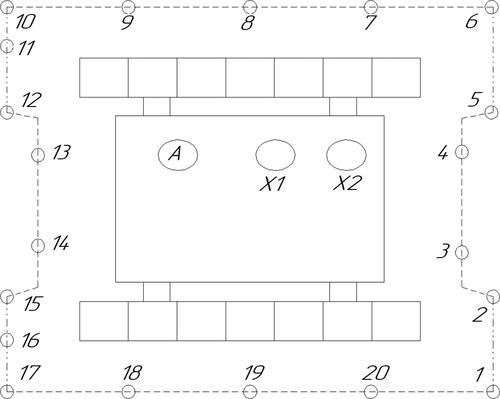
Table 4. Measured extraneous noise levels.
Table 5. Measured sound levels.
Table 6. Comparison between the calculated noise characteristics of РОМ-60000/525-У1 and those of РОМБСМ-60000/500-У1.
Figure 8. Process of measuring vibration displacements of the tank wall and the cooling system of РOM-60000/525-У1.
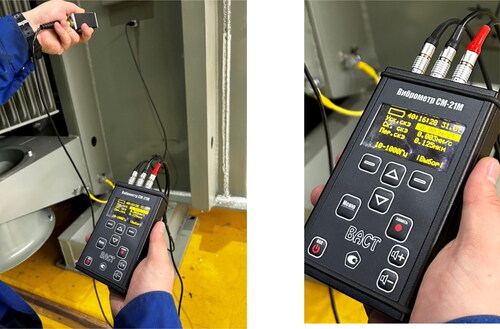
Figure 9. Points at which vibration displacements are measured on the tank wall (1–12) and the reactor cooling system (1–14).
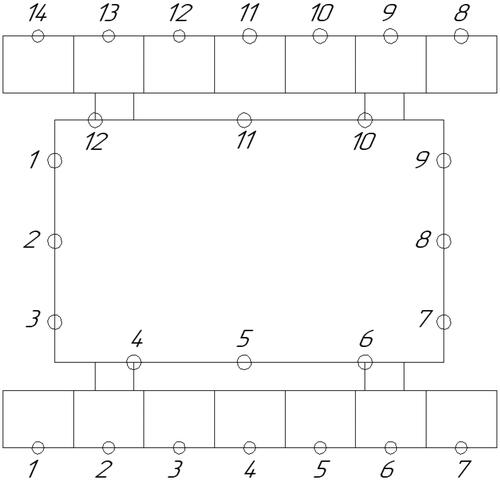
Table 7. Measured vibration displacements of the tank wall.
Table 8. Measured vibration displacements on the cooling system.
Figure 10. Vibration displacements (mm) of the tank walls at 100 Hz. (a) Calculation results and (b) 3D model of the tank.
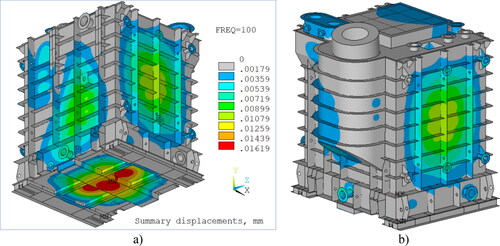