Figures & data
Table 1. Independent variables selected for optimization process for ice cream mixture as feed.
Table 2. Geometrical characteristics of SSF.
Figure 4. Model fitted curve for the variation of (a) specific heat, (b) density, (c) thermal conductivity, and (c) viscosity with static temperature obtained in ANSYS Fluent.
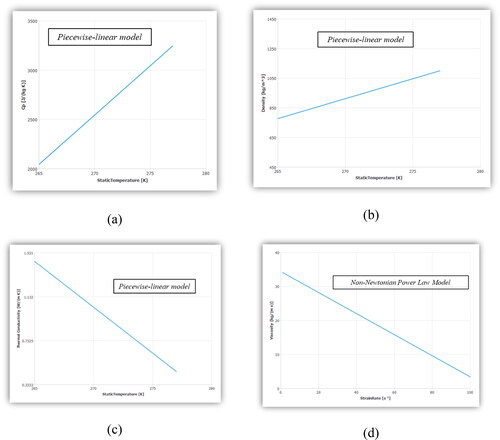
Table 3. Thermal properties of LN2 obtained from fluent database.
Table 4. Thermal properties of solid material (steel) applied from the fluent database.
Figure 5. Tetrahedral meshing of (a) blade and rotor assembly (b) around the surface of heat transfer tube and the jacket.
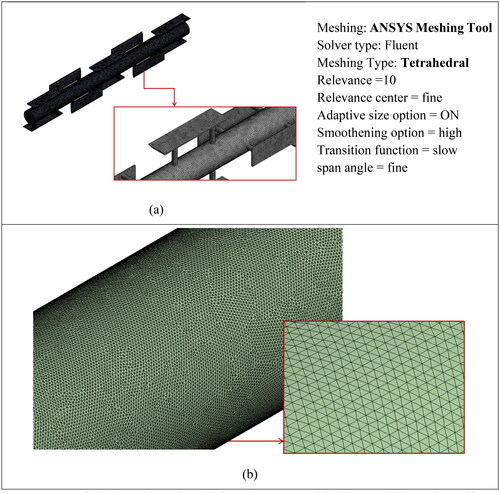
Figure 7. Effect of feed flow rate and LN2 temperature on the (a) drawing temperature and (b) overall heat transfer coefficient at scraper speed of 125 rpm.

Figure 8. Scatter plot illustrating the relationship between internally studentized residuals and Predicted values for the (a) drawing temperature and (b) overall heat transfer coefficient as the response variables.
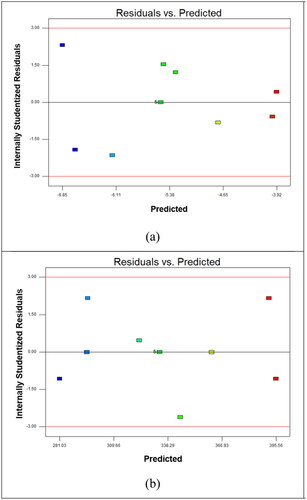
Figure 9. CFD parametric results obtained for the (a) output temperature condition, (b) velocity, and (c) pressure drop with varying feed flow rate and scraper speed.
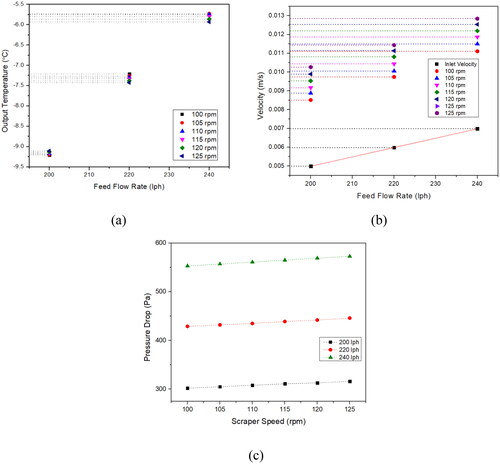
Figure 10. Velocity field in SSF obtained under reference operating conditions as predicted by numerical modeling.
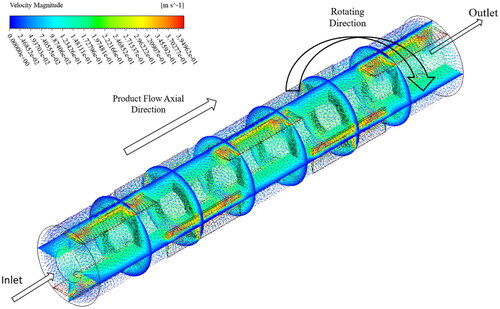
Figure 11. Velocity profile distribution under reference operating conditions V̇mix = 240 lph, TR = −95 °C, and Nrotor =125 rpm in the sectional plane A–A (right side) and B–B (left side).
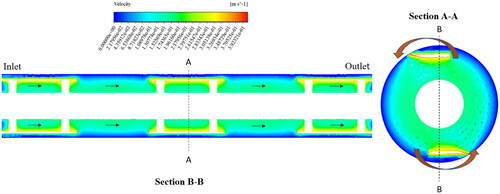
Figure 12. Temperature profile distribution under reference operating conditions V̇mix = 240 lph, TR = -95 °C, and Nrotor =125 rpm in the sectional plane A–A (right side) and B–B (left side).
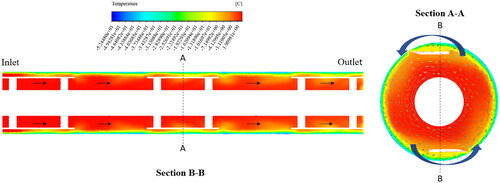
Figure 13. Pressure distribution under reference operating conditions V̇mix = 240 lph, TR = −95 °C, and Nrotor =125 rpm in the sectional plane A–A (right side) and B–B (left side).
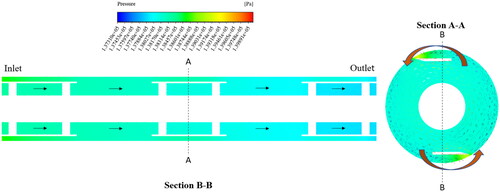
Figure 14. Temperature variation along axial distance of SSF for reference operating conditions V̇mix = 240 lph, TR = −95 °C, and Nrotor =125 rpm.
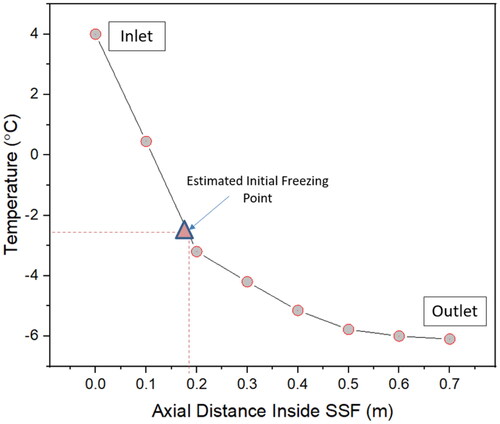
Data availability statement
All data used for this research is included in this manuscript.