Figures & data
Figure 1b. Integmac User Interface Snapshots of Remedial Actions. (c) Integmac Snapshot of Computed Integrity.
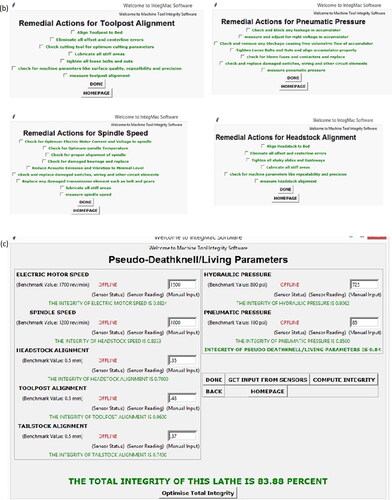
Table 1. Comparison between machine tools.
Table 2. Probe locations and measurement.
Figure 3(a). LDR Circuit Diagram, (b) Direct connection of LDR to the Arduino Board, (c) LDR Grid with a multiplexer and Jumper cables.
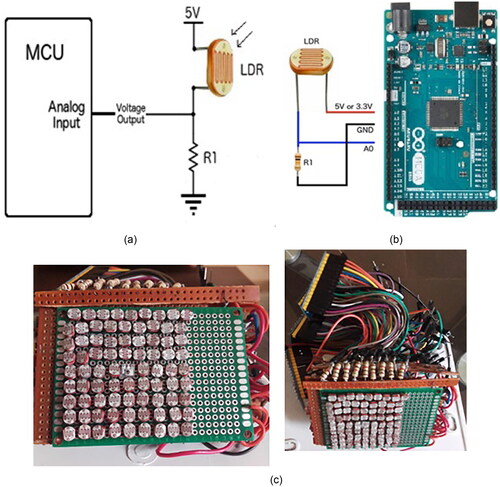
Figure 4. The alignment module is mounted onto the headstock, and the laser beam points towards the tailings stock.
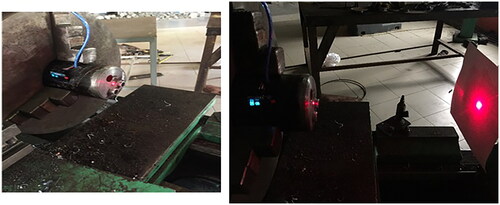
Table 3. Results of component calibration.
Table 4. Total machine integrity.
Table 5. Results of performance evaluation on developed mechatronic system.
Table 6. Machine tool accuracy assessment.
Data availability statement
The data that support the findings of this study are available from the corresponding author upon reasonable request.