Figures & data
Table 1. Site and HVAC system characteristics.
Fig. 2. Close-up of fouling at PSU site, upstream side of coil. Note the accumulation of fouling at the space between the tubes.
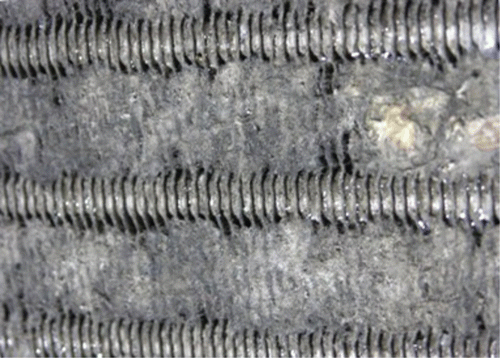
Table 2. Field site UV lamp information.
Table 3. Measurement instrumentation.
Fig. 3. Instrumentation schematic (T = temperature, RH = relative humidity, DP = pressure differential, CHW = chilled water piping).
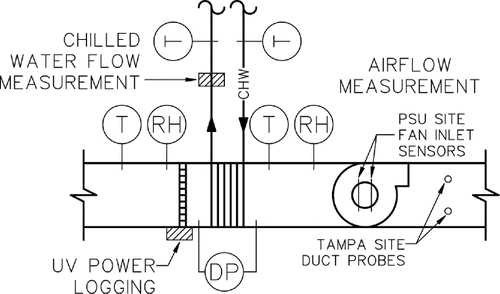
Table 4. UA model use of input variables in simulation software.
Table 5. Conditions for design UA value calculation.
Table 6. Binning range and interval for analysis of Tampa ΔP data.
Fig. 7. Tampa mean airside pressure drop versus time for example bins; a. 3800–4000 cfm and 44.4–47.8 kBTU/h (1.79–1.89 m3/s and 13–14 kW latent load); b. 4000–4200 cfm and 51.2–54.6 kBTU/h (1.89–1.98 m3/s and 15–16 kW). Error bars are ±2% of full scale for illustration, as the calculated standard deviations using the point measurement error of 0.14% full scale were too small to be visible.
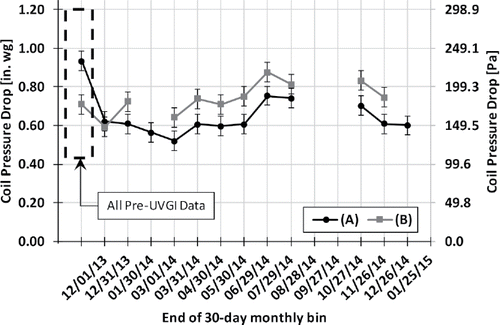
Table 7. Binning range and interval for analysis of PSU ΔP data.
Fig. 9. PSU mean air side pressure drop versus time for example bins; a. 14,200–14,400 cfm and 57.9–68.2 kBTU/h (6.61–6.70 m3/s and 17.5–20.0 kW); b. 14,200–14,400 cfm and 68.2–76.8 kBTU/h (6.61–6.70 m3/s and 20.0–22.5 kW). Error bars are ±2% of full scale for illustration, as the calculated standard deviations using the point measurement error of 0.14% full scale were too small to be visible.
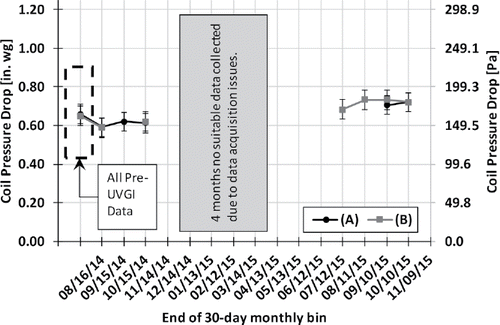