Figures & data
Figure 1. Comparison between experimental result from Taleb et al. and the calculated results based on Desalos’s, Abrassart’s, Leblond’s and ex-modified functions.
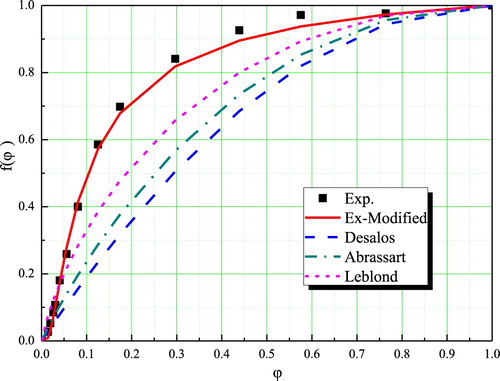
Table 1. Various expressions of 
functions.
Figure 2. Measured and calculated residual stress distributions based on various TP equations of 60 mm-diameter 40CrNiMo after water quenching: (a) tangential stress and (b) axial stress.
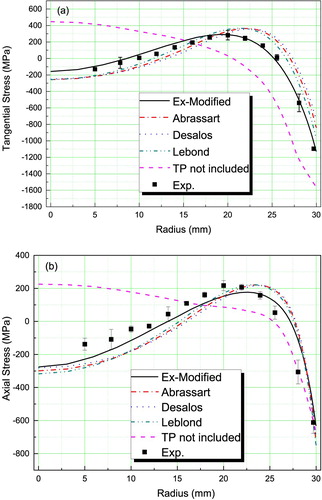
Figure 4. Finite element simulation of radial quenching stress of the driving shaft in different quenching ways: DQ (a), ATQ1 (b), and ATQ2 (c).
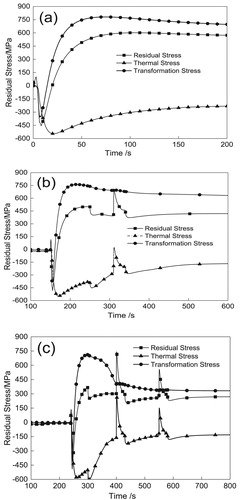